Modern vehicles have come a long way from their simple mechanical beginnings. Today, they are complex systems of integrated electronics, all thanks to the revolutionary advent of Printed Circuit Boards (PCBs). The role of PCBs in today’s automotive industry is as diverse as it is crucial, controlling everything from powertrain systems to infotainment. In this exciting journey, we will explore the integration of PCB in automotive applications, the stringent industry standards they adhere to, and the promising future they hold, especially in the realm of electric vehicles and smart car technologies. So buckle up as we delve into the fascinating world of automotive PCBs!
Key Takeaways
- Automotive PCBs are essential components integrated into various systems of modern vehicles, such as safety, infotainment, and engine controls. Their design must account for environmental challenges, reliability, and compliance with automotive standards.
- Automotive PCB manufacturing involves rigorous testing, including thermal shock and vibration tests, to ensure reliability. PCB design must consider thermal management, signal integrity, and component placement to optimize performance.
- Advancements in automotive PCBs, particularly in response to electric vehicle technology, require innovative design approaches to manage power and thermal performance. Electric vehicles drive the need for PCBs that can operate in compact spaces with high efficiency.
Exploring the Integration of PCB in Modern Vehicles
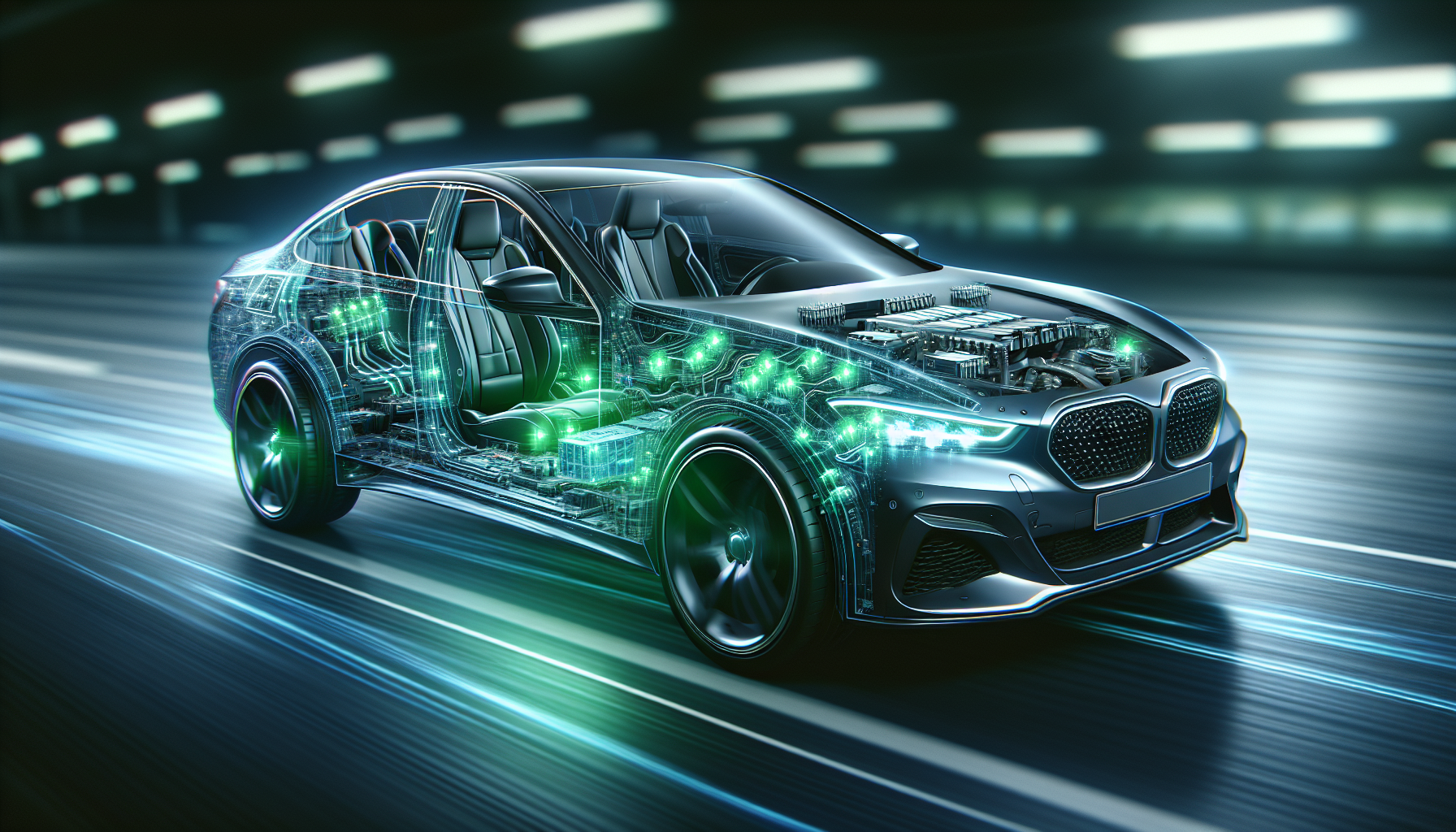
The automotive industry has swiftly embraced PCB technology, embedding it in a broad spectrum of vehicle systems, including automotive electronic systems. From the core functions of engine controls and powertrain systems to the comfort-enhancing aspects like infotainment and automatic locking systems, automotive PCBs serve as the backbone of modern vehicles’ functionality. They are even found in meticulous safety features such as electronic clutch pressure control, service brake sensors, and anti-lock brake systems, constantly ensuring a safe journey for the passengers.
The push for connectivity, electrification, and autonomous driving features fuels the integration of PCBs in modern vehicles. As vehicles become more advanced, the demand for automotive sensors - which heavily rely on PCBs - has skyrocketed. Nonetheless, the process of designing PCBs for automotive applications presents considerable challenges. It involves addressing:
- challenging environmental conditions
- ensuring high reliability and longevity
- managing mixed signals
- meeting stringent electromagnetic compatibility and international automotive standards
Most importantly, safety remains the prime concern in the design and manufacturing of automotive PCBs.
The Evolution of Automotive Printed Circuit Boards
Over the years, automotive PCBs have evolved to cater to the specific requirements of the automotive industry, ensuring reliability and performance in vehicles. The manufacturing of these PCBs incorporates an IATF 16949-certified quality management system, and ensures component adherence to AEC standards, as well as compliance with IPC standards. To ensure reliability, automotive PCBs undergo various tests, including:
- The thermal shock test, which assesses their ability to withstand rapid temperature changes
- The vibration test, which evaluates their resistance to mechanical stress and vibrations
- The humidity test, which measures their performance in high humidity environments
- The salt spray test, which checks their resistance to corrosion
This rigorous testing is crucial as automotive PCBs are integral parts of products that demand high reliability. Understanding the PCB’s ability to endure repeated temperature fluctuations, mechanical stress, humidity, and corrosion is thus a key step in validating its quality and reliability.
Standards like AEC-Q100 Rev-H and other AEC standards have played a crucial role in outlining the reliability and performance criteria for various types of automotive PCBs, including rigid and flexible PCBs. This has guaranteed their ability to endure the rigorous conditions of automotive use, thereby shaping their development and dependability over time.
Essential Design Principles for Automotive PCBs
Designing PCBs for automotive applications is a process that requires the mastery of certain principles, the most essential of which are signal integrity, thermal management, and component placement. Each of these principles plays a major role in the performance and reliability of the PCB, and thus, the overall function of the vehicle. But what do these principles entail, and how do they impact the design of automotive PCBs?
We will examine these principles further in the following subsections.
Ensuring Signal Integrity in Vehicle Electronics
Signal integrity is crucial for the proper functioning of vehicle electronics. Poor signal integrity can lead to:
- Interference
- Inaccuracies
- Operational issues
- Diminished performance or potential breakdown of vehicle electronics
One of the key factors that can degrade signal integrity is noise. Noise has the potential to alter or deform the signal’s shape, leading to a decline in signal quality. Maintaining significantly lower noise levels than signal levels is key to preserving signal integrity in automotive PCB design.
Grounding assumes a pivotal role in the effort to maintain signal integrity. It helps prevent poor impedance of various circuits, which can arise from the electronic components and their connectivity. Furthermore, proper routing techniques are employed in automotive PCB design to maintain signal integrity. These include implementing power and ground planes, a specific layer configuration, controlling trace width and clearance for impedance sensitive traces, adhering to high-speed PCB routing best practices, and employing techniques such as auto-router moderation and wider traces.
Thermal Management Techniques in PCB Design
Another significant design principle in automotive PCB design is thermal management. Components that absorb more than 10 mW or conduct more than 10 mA generate heat, which needs to be effectively dissipated to ensure the reliability and longevity of the PCB. Initiating thermal management requires identifying the components that give off the most heat. Once identified, these components need to be strategically positioned for optimal heat distribution or concentration.
Thermal vias and copper planes play a significant role in enhancing thermal conductivity in PCBs, thereby contributing to the efficient heat dissipation process. Components that produce significant heat should be positioned at the center of the board to facilitate even heat dissipation in all directions. The operating temperature of automotive PCB components is affected by several factors, including:
- Trace thickness
- Number of layers
- Continuity of thermal paths
- Surface area of the board
Component Placement for Optimal Performance
The performance of automotive PCBs significantly depends on the orientation and placement of components. Proper component placement enhances circuit efficiency, reduces physical size, and influences signal integrity and EMI. This is particularly crucial for high-frequency components. When considering the size and type of components in automotive PCB design, the following factors are essential to consider:
- Effective thermal management
- Appropriate component placement
- Adherence to specific layout guidelines, such as ensuring adequate space for inductors and aligning them at right angles
By taking these factors into account, you can optimize the performance of your automotive PCB design.
When placing inductors on automotive PCBs, it is advisable to:
- Allocate as much space as possible
- Orient them at right angles
- Arrange all inductors in close proximity within the circuit
- Minimize coupling balance
These practices are considered best practices.
Types of PCBs Utilized in the Automotive Industry
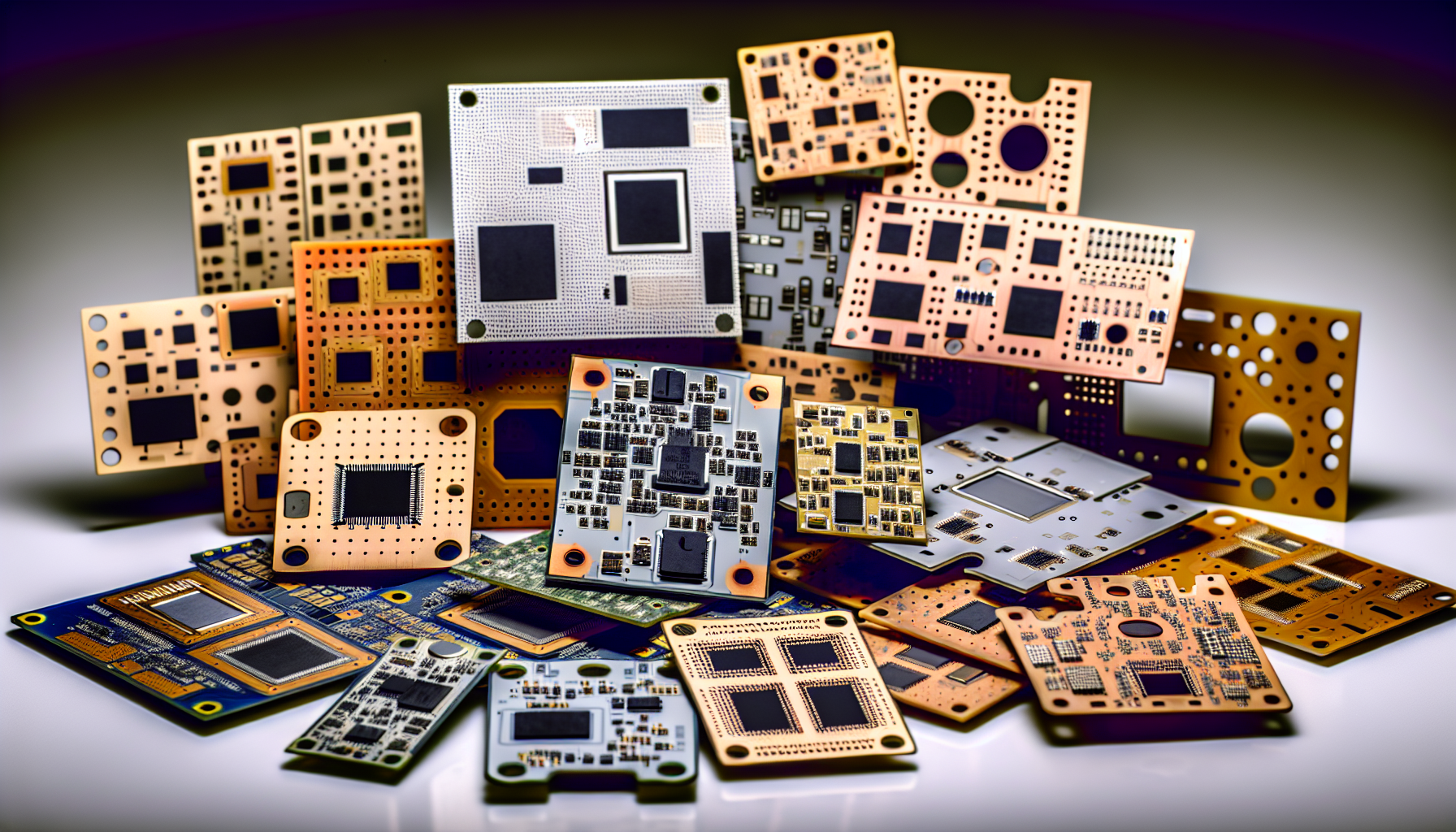
The automotive industry utilizes a variety of PCB types, each with its unique characteristics and applications. These include:
- Rigid boards, constructed from solid laminates like FR4, commonly employed in applications such as display monitors and rear-view cameras
- Flex PCBs, used in cell contact assemblies, battery management systems, vehicle sensors, and car lights
- Rigid-flex PCBs, which combine the benefits of both rigid and flexible boards
- HDI (High Density Interconnect) boards, designed for high-density circuitry and miniaturization
- Heavy copper boards, used for high-power applications and thermal management
- Ceramic substrate boards, known for their excellent thermal conductivity and high-frequency performance
- Metal core boards, featuring a metal core for improved heat dissipation
- High-frequency boards, optimized for high-speed signal transmission
Each type of PCB has its own advantages and is chosen based on the specific requirements of the automotive application.
Not only do these different types of PCBs cater to various applications, but they also offer unique advantages. For instance:
- HDI automotive PCBs are frequently utilized in in-vehicle computers and audio-video systems
- High-frequency automotive PCBs are utilized in advanced systems such as parking distance control, forward collision warning systems, and vehicular communication systems
- Ceramic PCBs are utilized in engine controls, brake systems, power control units, and lighting due to their notable high heat resistance, making them ideal for high-temperature settings such as the engine compartment and turbochargers.
Meeting Automotive Industry Standards with PCB Design
Designing and manufacturing automotive PCBs involves not only achieving optimal performance but also conforming to stringent industry standards. Some of these standards include:
- IATF 16949
- IPC-6012 class 3
- AEC-Q100
- SAE J3016_201401
These standards are crucial to ensure high reliability and traceability. For example, IPC-6012 class 3 provides guidelines for crucial aspects of manufacturing parameters, such as pattern, solder mask thickness, and copper thickness, among others.
In addition to these standards, the automotive functional safety framework is of great importance for PCB design. This framework provides a structured approach with requirements traceability, which has a significant impact on design validation and ensures reliability. It is thereby evident that meeting these industry standards is not just a compliance requirement but an essential step in delivering high-quality, reliable PCBs for the automotive industry.
Innovations in PCB for Electric Vehicle Technology
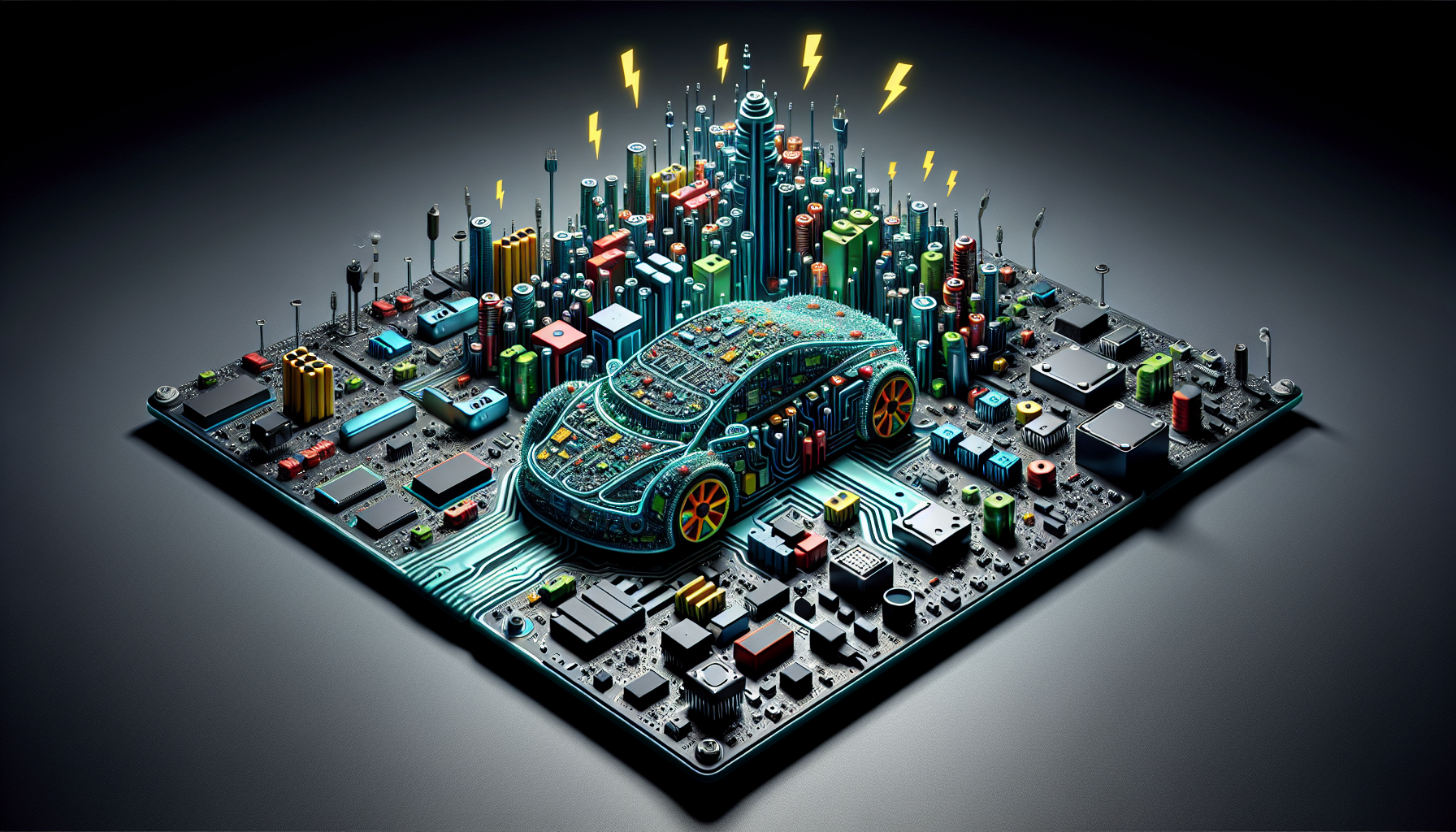
Within the sphere of electric vehicle technology, PCB design innovations are making notable advancements. These advancements focus on enhancing power management and thermal management, optimizing components and routing paths for improved space utilization, and designing efficient power distribution networks. Automotive PCBs play a crucial role in electric vehicle battery systems, ensuring safety, enhancing performance, and providing reliable power management. They monitor and regulate power flow, manage complex electronic systems, and support voltage conversions, thus forming a critical part of the vehicle’s operation.
Recent developments in PCB design for electric vehicle charging systems encompass:
- The creation of more intricate and refined designs
- The incorporation of flexible PCBs
- Enhancements in cell balancing
- Expanded vehicle range
- Improved heat dissipation
- High-density integration in PCBs
- More circuitry in a smaller area
- A greater number of interconnections
- Facilitation of crucial functions within the spatial limitations of electric vehicles
These advancements contribute to the overall performance and efficiency of electric vehicles.
Addressing Electromagnetic Interference in Automotive PCBs
Designing automotive PCBs often involves confronting the common challenge of electromagnetic interference (EMI). EMI can cause significant problems, including interference, inaccuracies, operational issues, and diminished performance of vehicle electronics. Typical sources of EMI in automotive PCBs encompass design flaws that result in interference among the traces, circuits, vias, and PCB coils.
To mitigate EMI, automotive PCBs utilize various shielding techniques. For instance, circuit grounding with ground wires and copper ground planes or straps can help prevent interference. Furthermore, EMI and RF shielding can be applied using copper layers, silver ink, and shielding films. Thus, addressing EMI is a critical aspect of automotive PCB design, essential for the optimal functioning of the vehicle’s electronic systems.
Advanced Materials and Manufacturing Processes for Automotive PCBs
When it comes to materials and manufacturing processes, the automotive PCB industry boasts numerous advancements. For instance, heavy copper is often used in automotive PCBs due to its excellent electrical conductivity and resistance to thermal strain. Ceramic substrates, with their high heat resistance and stability, are also utilized, particularly in high-temperature settings such as engine systems.
Metal core PCBs, characterized by their good thermal conductivity and dimensional stability, are ideal for automotive LED applications and can reduce the overall weight of the board. Another advanced material used in automotive PCBs is PTFE (Polytetrafluoroethylene). With its excellent chemical stability, high resistance to corrosion, exceptional sealing capabilities, high lubrication, wide service temperature range, high thermal stability, and resistance to heat, chemicals, and electricity, PTFE offers stable and consistent dielectric properties and a low dielectric constant, enabling faster signal transmission.
The Role of PCBs in Automotive Safety and Comfort Features
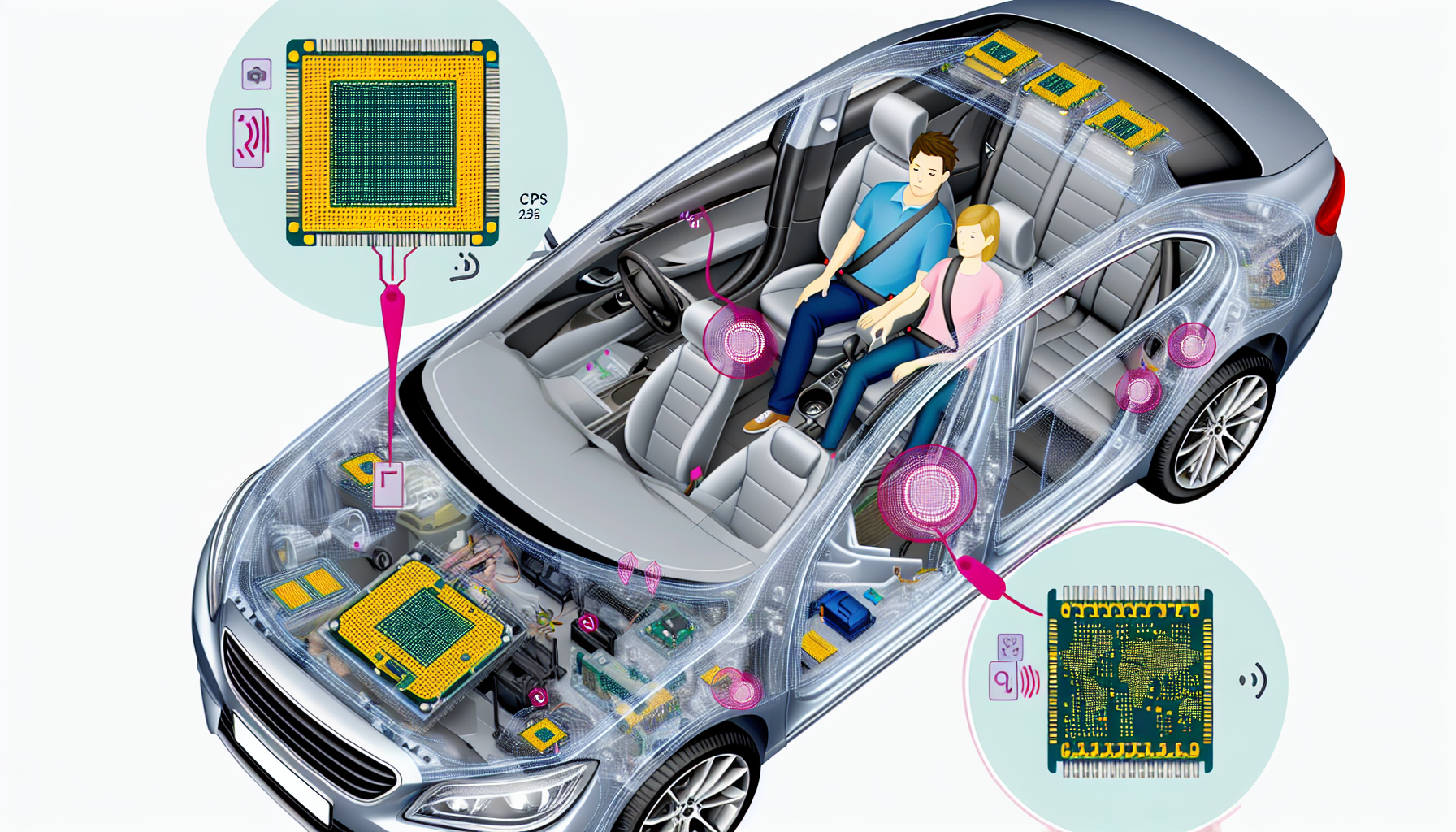
Automotive PCBs are instrumental not only in a vehicle’s performance but also in augmenting the safety and comfort of its occupants. These PCBs are embedded in various safety features such as:
- Engine controls
- Airbag sensors
- Anti-lock brake management
- GPS support
They play a vital role in ensuring a safe journey. For instance, in automotive GPS systems, PCBs manage the GPS module, transmit location data to the microcontroller, and minimize interference such as noise levels and crosstalk to ensure accurate navigation.
PCBs also play a significant role in vehicle radar systems by facilitating functionalities such as signal processing, data transmission, and control. They support the integration of antennas and radio frequency components, which are vital for radar operation.
Further enhancing the driving experience are automotive infotainment systems, where PCBs enable advanced features such as:
- smartphone connectivity
- touchscreen controls
- voice recognition
- in-car Wi-Fi
PCB Assembly Techniques for the Auto Industry
The automotive industry employs a series of PCB assembly techniques to guarantee the PCBs’ reliability and longevity. The process includes:
- DFA (Design for Assembly) verification
- SMT (Surface Mount Technology) assembly using pick and place machines
- Application of solder paste
- Precise component placement
- Reflow soldering
To ensure the PCBs’ compliance with the rigorous performance and durability criteria set by the automotive industry, they undergo various reliability tests, including:
- Thermal cycling test
- Shock and vibration testing
- Humidity and bias testing
- High Temperature Operating Life (HTOL) assessments
How PCBs Empower Smart Car Technologies
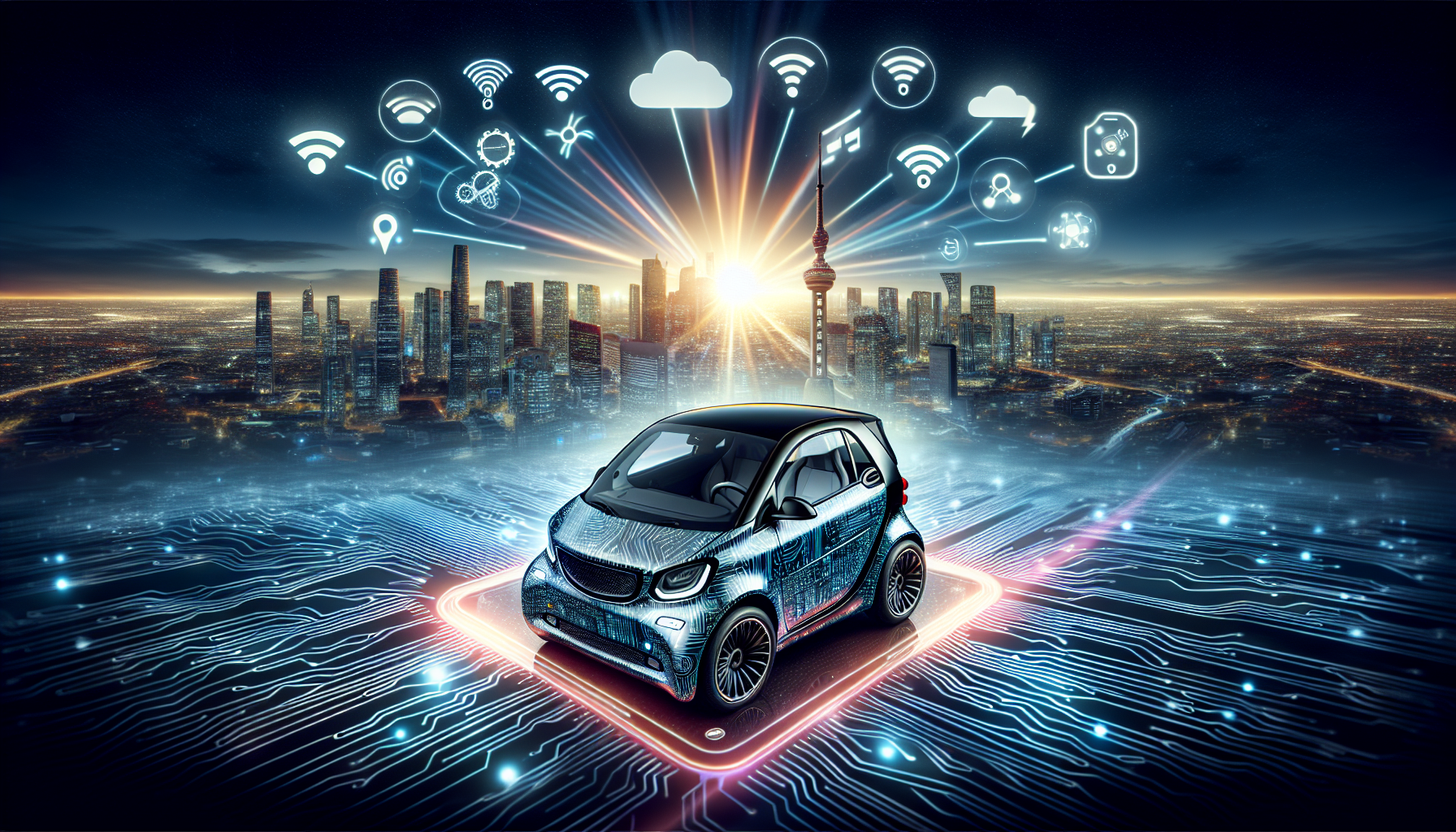
As vehicles progress towards being smart cars, the role of PCBs in facilitating this evolution becomes increasingly significant. PCB technology facilitates autonomous driving in smart cars by regulating multiple aspects of the car’s operation, such as safety, passenger comfort, and convenience. Flexible PCBs, with their intricate communication interfaces and antennas, enable high-speed data transmission, which is crucial for autonomous vehicles to make instantaneous decisions.
In automotive infotainment systems, the design of PCBs significantly influences the integration of sophisticated features such as entertainment systems, digital displays, and GPS. PCBs also play a crucial role in providing mechanical support and electric connections to various vehicle components essential for smart car connectivity. Furthermore, advancements in PCBs, such as the creation of complex circuits on Flex PCBs, the use of miniaturization, flexible designs, and advanced materials, are shaping the future of mobility.
The Future of Automotive PCBs: Trends to Watch
The future of automotive PCBs promises excitement as various trends drive the demand for advanced PCB designs. One of these trends is panel scale manufacturing, which facilitates the amalgamation of PCBs and ICs, leading to enhanced performance and the downsizing of components. Another significant trend is high-density integration, which allows for more circuitry in a smaller area, facilitating higher signal integrity, faster transmission speeds, and enhanced overall performance.
The increasing prevalence of electric vehicles is also influencing the demand for advanced PCB designs. These vehicles necessitate PCBs that can fit into compact spaces while delivering reliable and efficient performance to meet their specific demands. As electric vehicles continue to gain popularity, the demand for advanced PCBs designed to meet their specific requirements is set to rise, driving further innovation in the field.
Summary
In conclusion, PCBs have become an integral part of the automotive industry, underpinning the functionality of modern vehicles from powertrain systems to infotainment. With advancements in PCB design and manufacturing, coupled with the increasing demand for electric and smart vehicles, the future of automotive PCBs is poised for exciting developments. As we continue to embrace the era of smart mobility, the role of PCBs in shaping this future becomes increasingly significant. As technology continues to evolve, we can look forward to more advancements in automotive PCBs, driving the next wave of innovation in the automotive industry.
Frequently Asked Questions
What is a PCB used in automotive?
A PCB in automotive is used for connecting lighting systems like interior cabin lights, headlights, and fog lamps to the car's battery, through a metal core PCB (MCPCB) made of aluminum or copper. Additionally, PCBs are used in vehicles for stereo systems, video displays, and global positioning systems (GPS).
What is PCB and its purpose?
PCBs, or printed circuit boards, provide mechanical support and electrical connection for electronic components in devices. They are made from non-substrate materials with copper circuitry layers, and are easily recognizable as the green-colored boards in electronic devices.
How is signal integrity maintained in automotive PCB design?
In automotive PCB design, signal integrity is maintained through proper grounding, routing, and shielding techniques such as controlling trace width and using shielding films to prevent electromagnetic interference. These measures ensure the integrity of signals within the design.
What are the essential design principles for automotive PCBs?
The essential design principles for automotive PCBs include signal integrity, thermal management, and component placement, which are crucial for ensuring proper functioning and reliability of the vehicle's electronics.
How do PCBs contribute to the safety and comfort features of vehicles?
PCBs significantly contribute to the safety and comfort of vehicles by being integrated into crucial safety features like airbag sensors and anti-lock brake management, as well as enabling advanced functionalities in infotainment systems. Overall, they play a vital role in enhancing the overall vehicle experience.