Wondering why semiconductor silicon carbide (SiC) is revolutionizing power electronics? If efficiency and high-voltage operation are your concerns, SiC delivers exceptional performance. This article breaks down SiC’s superior characteristics, its edge over traditional silicon, and its transformative use in sectors like automotive and energy. Understand the reasons that make SiC semiconductors crucial for a high-efficiency future.
Key Takeaways
- Silicon carbide (SiC) semiconductors offer significant advantages over traditional silicon, including higher breakdown voltages, superior thermal conductivity, and improved electrical conductivity with impurities, marking a revolution in power device design.
- SiC power devices, such as MOSFETs and diodes, enhance energy efficiency across various applications, including electric vehicles and renewable energy systems, by providing higher power density, reduced losses, and improved high-temperature performance.
- Emerging SiC technologies are driving advancements in power electronics, with the fourth-generation SiC MOSFETs reducing system size and power consumption, paving the way for increased adoption in automotive and industrial applications.
Exploring the Basics of SiC Semiconductors
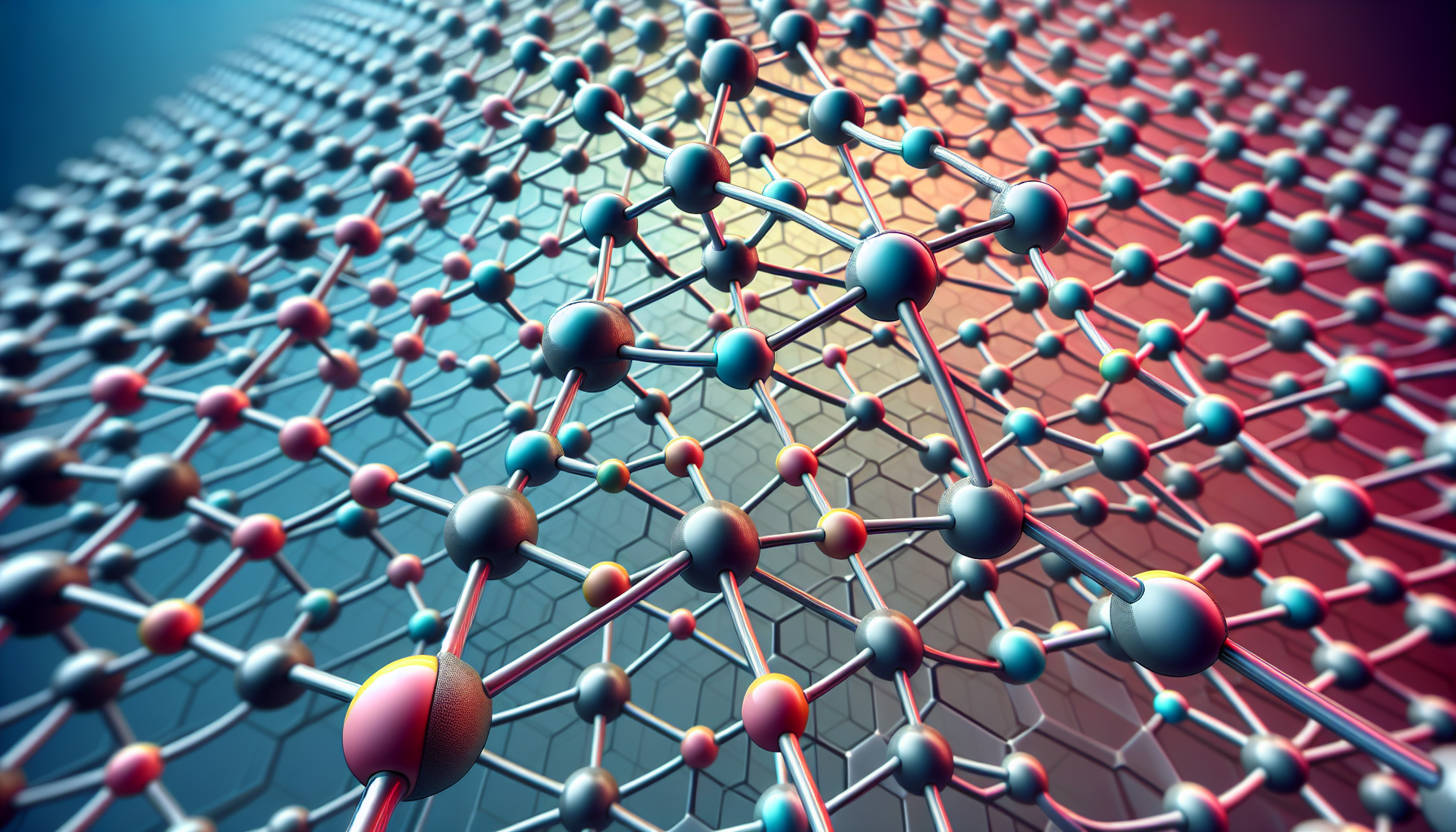
Silicon carbide, a crystalline compound of silicon and carbon, revolutionizes the semiconductor world. Its inherent properties, like its ability to withstand high breakdown voltage of several thousand volts, make it a perfect material for power devices handling high voltages. But that’s not all. SiC also boasts a thermal conductivity of around 1490 W/m-K, far surpassing that of silicon, which stands at about 150 W/m-K. This superior thermal management capability is a significant advantage in semiconductor devices.
But SiC’s remarkable attributes don’t end there. Its ability to handle high breakdown voltages is, in part, due to its dielectric breakdown intensity, which is about ten times higher than that of silicon. Furthermore, SiC semiconductors exhibit high mechanical, chemical, and thermal stability. The presence of impurities such as nitrogen and aluminum can even alter the material’s electrical conductivity, offering additional flexibility in device design.
Some key attributes of SiC semiconductors include:
- High dielectric breakdown intensity
- High mechanical, chemical, and thermal stability
- Ability to alter electrical conductivity with impurities like nitrogen and aluminum
Silicon Carbide vs. Conventional Silicon Devices
Despite the reliable service of conventional silicon devices, the emergence of silicon carbide (SiC) has set new standards in the semiconductor industry. SiC stands out with its wide band gap, high thermal stability, and greater electron mobility. These physical properties contribute to lower power and switching losses, setting new standards in power electronics applications.
Envision a world where our devices outperform yet consume less power. That’s the promise of SiC. By offering superior performance, SiC semiconductors are transforming the landscape of power electronics, paving the way for a more energy-efficient future.
The Unique Advantages of SiC Power Devices
SiC power devices are radically changing the power electronics landscape. Their inherent material properties enable them to support high voltages and fast operation with low turn-on resistance, making them ideal for demanding power applications. Take, for instance, Toshiba’s 1200V SiC MOSFETs. These devices offer high-speed switching capabilities and low ON-resistance, enhancing overall efficiency.
In addition, SiC power devices are designed to function at temperatures higher than conventional silicon devices. This ability is crucial for higher power density applications, where managing thermal loads can be challenging.
The combination of high power density, increased efficiency, and high-temperature operation underscores the unique advantages of SiC power devices in power electronics.
SiC Power Components Unveiled
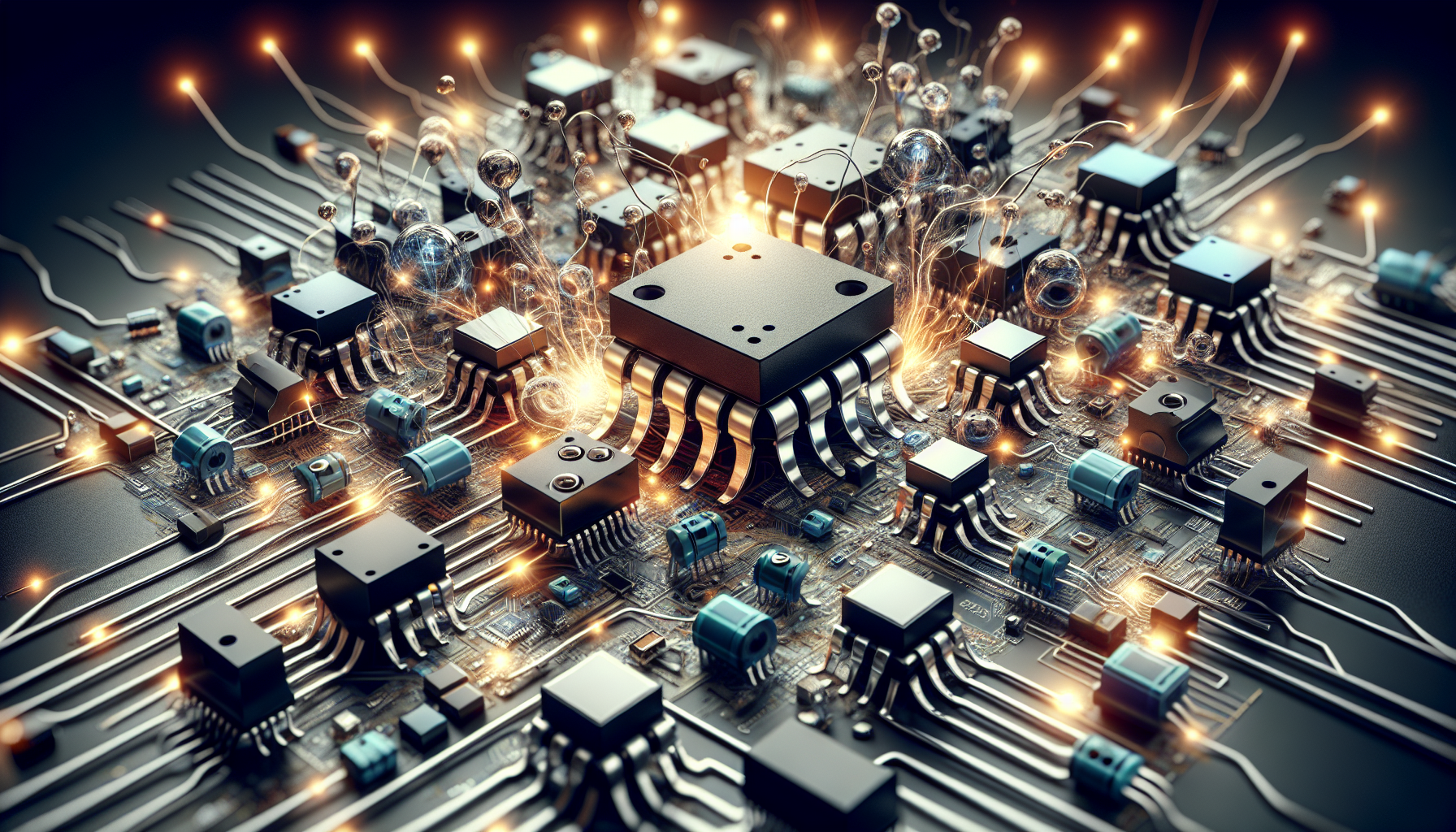
Exploring the realm of SiC power components reveals two key participants – MOSFETs and diodes. SiC MOSFETs have superior performance over IGBTs, particularly at high frequencies due to reduced switching losses. They contribute significantly to the enhanced motor efficiency and increased power density in electric vehicles, as seen in the Lucid Air.
On the other hand, SiC diodes are integral components in power supplies, enabling power conversion efficiencies of over 97%. The high power conversion efficiency of these SiC power components is pivotal in reducing operational costs and fulfilling quality and regulatory standards in various applications.
The Role of SiC MOSFETs in Power Conversion
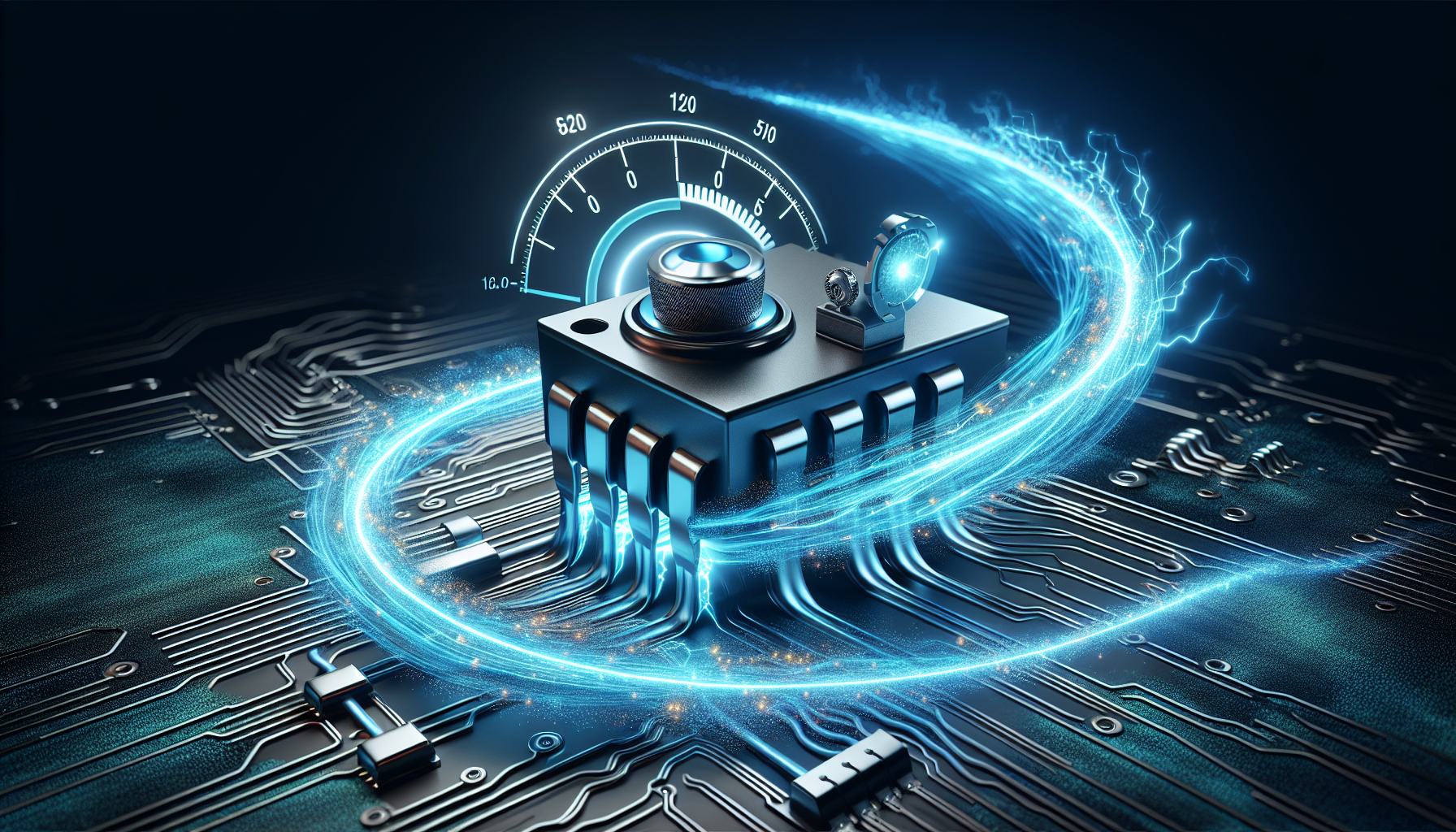
SiC MOSFETs are instrumental in power conversion, offering considerable advantages:
- They reduce turn-off loss
- They contribute to the miniaturization of power conversion systems due to their smaller chip area
- The intrinsic body diode in SiC MOSFETs offers a much faster reverse recovery time than silicon-based MOSFETs, enhancing the switching performance of power supplies.
The 4th generation SiC MOSFETs by ROHM have the following features:
- Double-trench structure design, which significantly reduces energy losses and accelerates switching speeds
- Short circuit robustness, maintaining high performance
- Lower on-resistance and reduced saturation current, optimizing power conversion
In high-frequency operations, such as in wireless power transfer systems, these MOSFETs demonstrate improved efficiency, critical for the transfer performance of wireless charging technology.
SiC Diodes: Paving the Way for Higher Efficiency
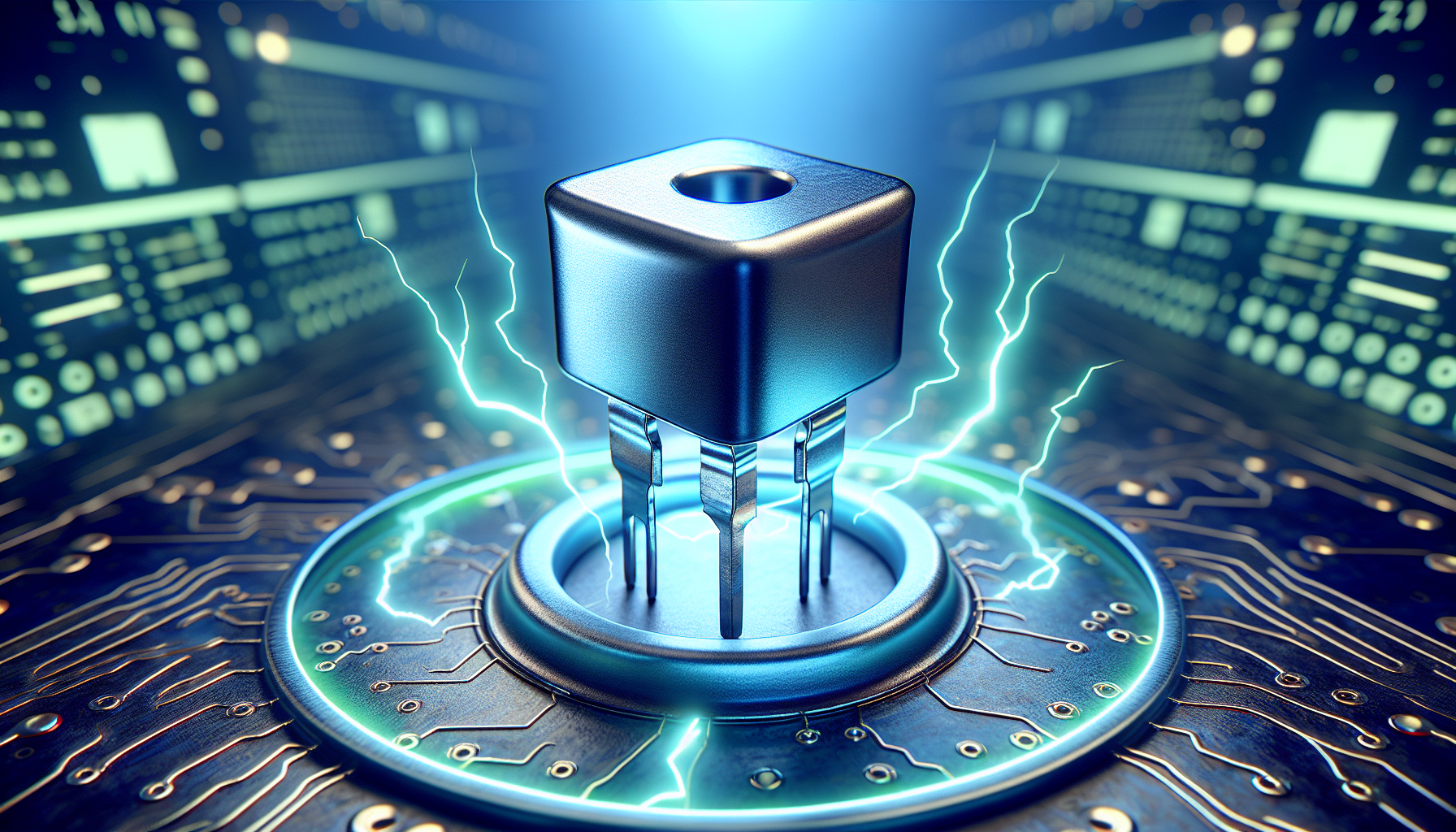
SiC Schottky barrier diodes are setting the stage for a future driven by higher efficiency in power electronics. One such schottky barrier diode is Toshiba’s 3rd generation SiC Schottky barrier diodes, which feature an industry-leading lowest forward voltage of 1.2V, resulting in substantial energy savings in power electronic systems. These diodes also exhibit a low temperature dependence of forward voltage, enhancing device reliability and preventing thermal runaway in parallel connection applications, crucial for high power settings.
Comprehending the function of SiC diodes extends beyond their technical specifications. It’s about seeing their impact in real-world applications. For instance, their use in electric vehicle HVAC compressors exemplifies the performance benefits, including improved energy efficiency in demanding climates.
Application Spotlight: SiC in Electric Vehicles and Renewable Energy
Silicon Carbide (SiC) technology goes beyond improving device performance; it revolutionizes industries. For instance, it plays a paramount role in enhancing the energy efficiency of electric vehicles, their charging stations, and high voltage systems. SiC devices help to diminish power losses in automotive applications, contributing to improved energy density and efficiency.
Moreover, advancements in the 4th generation SiC MOSFETs offer a competitive edge over traditional silicon IGBTs by enhancing efficiency and power density in EV power systems. And it’s not just the automotive industry that’s benefiting. SiC devices, particularly Schottky barrier diodes and MOSFETs, enable efficiency gains in charging stations and improved performance in solar inverters for renewable energy applications.
Traction Inverters and EV Charging Stations
In the field of electric vehicles, SiC semiconductors are creating a significant impact. They:
- Improve power factor correction and overall efficiency in EV charging stations
- Play a key role in traction inverters, enabling the use of higher battery voltages, like 800V
- Contribute to faster EV charging times and reduced energy losses in the system
These advanced SiC MOSFETs are not just about performance; they’re about quality and durability. Optimized for the high standards necessary for electric vehicle powertrain systems, they enhance performance and reliability, ensuring that your ride is as efficient as it is smooth.
Boosting Solar Inverter Performance with SiC
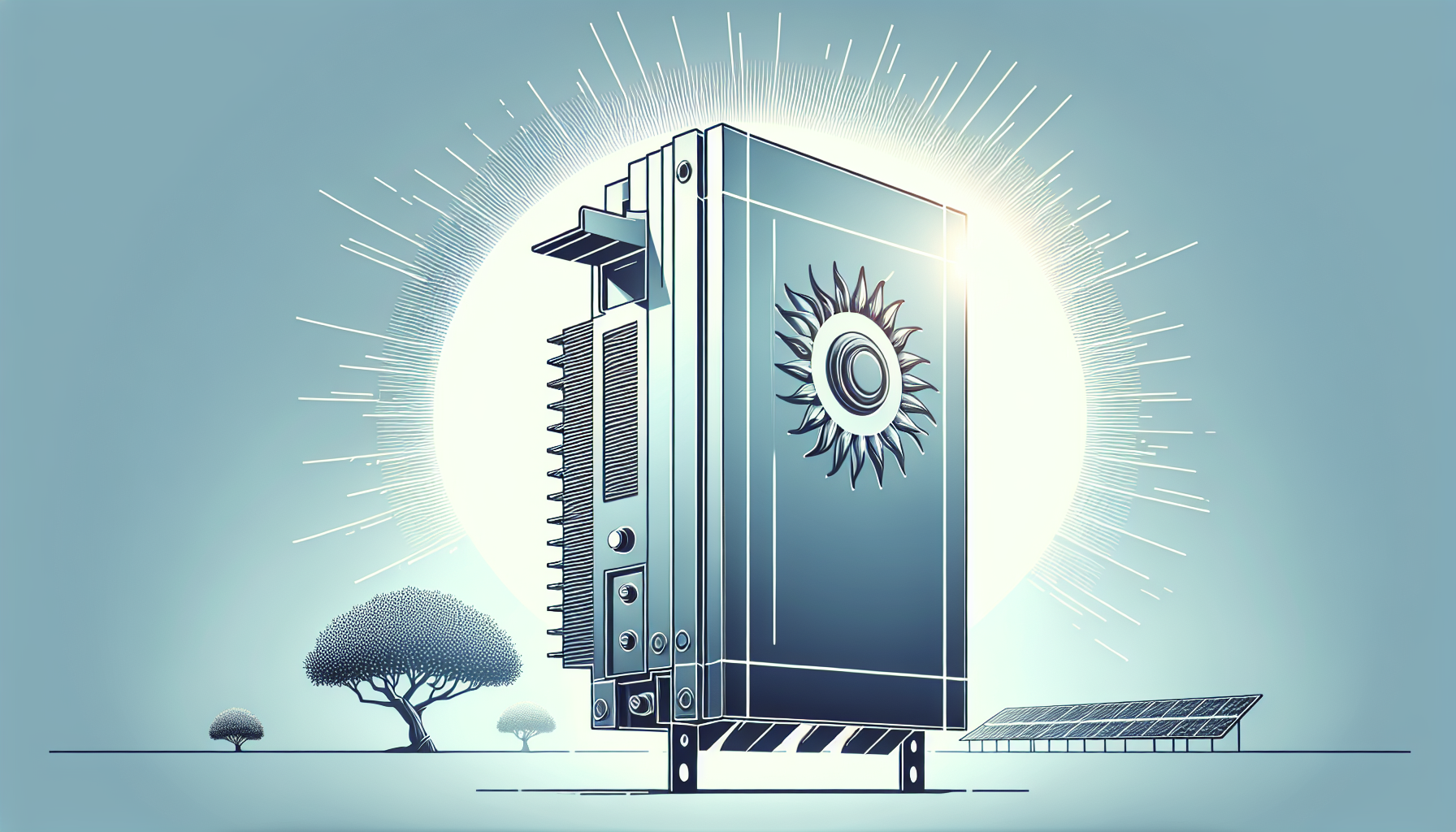
The use of SiC extends beyond vehicles, reaching into the sector of renewable energy. SiC semiconductors offer superior efficiency and thermal conductivity, making them an attractive option for solar inverter systems. Some benefits of SiC semiconductors in solar inverter systems include:
- Improved voltage handling capabilities
- Higher power density
- Reduced power losses
- Increased system efficiency
These advantages contribute greatly to the performance of string inverters used in solar power supply systems.
For instance, Infineon’s 1500V PV string inverter utilizes SiC MOSFET technology to operate at higher frequencies, offering a more cost-effective solution compared to traditional IGBT-only systems. These SiC-based solar inverters not only show higher reliability but also provide the potential for reduced losses, leading to enhanced long-term performance.
Thermal Management and SiC
A noteworthy advantage of SiC is its potential for enhanced thermal management. Here are some key benefits:
- SiC boasts a high thermal conductivity of 120 W/m•K, allowing it to dissipate heat efficiently.
- It maintains its mechanical strength at elevated temperatures, enduring up to 1400°C.
- This makes SiC highly beneficial for thermal management needs.
SiC semiconductors offer several advantages over silicon:
- They can operate at junction temperatures higher than silicon, potentially exceeding 200°C without performance degradation.
- This ability to operate consistently at higher temperatures, frequencies, and voltages enables more efficient management of thermal loads in power applications.
- SiC MOSFETs allow for efficient operation of high-speed and wheel hub machines due to their fast switching speeds and high-temperature capability.
- Operating at higher frequencies leads to smaller passive components and cooling systems, optimizing the design of industrial motor drives.
Furthermore, the low coefficient of thermal expansion of SiC minimizes stress and risk of damage from thermal shock, contributing to durable electronic designs.
Designing with SiC: Considerations for Device Designers
Designing with SiC comes with its own set of challenges. These devices require high-temperature processing, with dopant activation surpassing 1500°C, presenting unique challenges compared to silicon. Some of the challenges include:
- High-temperature annealing for forming ohmic contacts on SiC
- Optimization of contacts to withstand high temperatures
- Influence on subsequent device processes
Moreover, ensuring high yield and performance in SiC devices involves meticulous management of defects such as micropipes, screw dislocations, and basal plane defects. SiC devices offer the ability to operate at thinner dimensions due to the material’s wide bandgap, enhancing switching speeds, reducing heat, and increasing power supply efficiency.
The design of SiC power components is advancing to address high electric field-related challenges, such as reducing electromagnetic interference and crosstalk, as well as thermal management. In addition, ROHM is developing gate drivers optimized for driving SiC devices, catering to the unique switching characteristics of SiC MOSFETs. SiC MOSFETs’ susceptibility to thermal breaks due to high current density in a small area necessitates careful design considerations such as soft turnoff for short circuit protection.
SiC's Impact on Power Density and Energy Savings
SiC power devices are causing a stir in the industry with their potential for:
- Increased efficiency in switching power supplies
- Accelerated switching
- Reduced losses
- Improved thermal management
The robustness of SiC allows it to operate at high temperatures and high withstand voltage, increasing the reliability and service life of power supplies by resisting thermal stress.
The high efficiency and thermal conductivity of SiC offer several benefits, including:
- Minimizing the need for additional cooling components, which reduces operational and cooling costs, particularly in continuous-run industrial settings
- Providing versatile and cost-effective solutions for various industries
- Balancing the demands for power density and flexibility without increasing system costs
SiC technology is a valuable option for industries looking to optimize their operations.
Advanced SiC Technologies and Future Trends
The outlook for SiC technologies is promising. The development of unique high-temperature crystal growth processes has provided access to large and high-quality SiC wafers, essential for high-power applications. Furthermore, the 4H-SiC polytype with a hexagonal crystal structure is currently the most suited for high-power and efficiency applications due to its superior properties.
The 4th generation SiC MOSFETs offer drastic reductions in system size and power consumption, with a significant 6% electricity consumption reduction over IGBT solutions in specific scenarios. Experimental tests for these MOSFETs have included their use in step-down DC-DC converters, simulation in EV traction inverters, and a Totem-pole PFC circuit, demonstrating their versatility.
Major automotive firms, such as General Motors, Jaguar Land Rover, and Mercedes-Benz, are incorporating Wolfspeed’s silicon carbide semiconductors into their upcoming electric vehicle platforms.
Summary
In conclusion, Silicon Carbide (SiC) is redefining the semiconductor industry and shaping the future of power electronics. It offers superior efficiency, faster switching, lower losses, and better thermal management, paving the way for a more energy-efficient world. Whether it’s enhancing the energy efficiency of electric vehicles, improving the performance of solar inverters, or providing cost-effective solutions in various industries, SiC is at the forefront, leading the way. As technology continues to advance, we can only expect SiC to play an even more significant role in shaping our energy-efficient future.
Frequently Asked Questions
What is SiC in semiconductors?
SiC stands for silicon carbide and it is a semiconductor material that consists of pure silicon and pure carbon, utilized in MOSFETs and Schottky diodes. It can be doped to form different types of semiconductors.
What is the downside of silicon carbide?
The downside of silicon carbide is that it is expensive to manufacture due to high production costs and requires complex production processes, such as high temperature and high pressure. This can make it challenging for widespread adoption.
How does SiC compare to conventional silicon devices?
SiC offers superior performance in power electronics applications due to its wider band gap, higher thermal stability, and greater electron mobility compared to traditional silicon. This leads to lower power and switching losses.
What role do SiC MOSFETs play in power conversion?
SiC MOSFETs play a crucial role in power conversion by reducing turn-off loss, contributing to miniaturization, and offering faster reverse recovery time compared to silicon-based MOSFETs. These qualities make them essential for efficient power conversion systems.
How does SiC enhance the energy efficiency of electric vehicles and charging stations?
SiC technology enhances the energy efficiency of electric vehicles and charging stations by improving power factor correction, overall efficiency, and enabling higher battery voltages in traction inverters, leading to faster charging times and reduced energy losses.