When it comes to semiconductors, testing is paramount. This article answers the pivotal question of why semiconductor test processes are essential and how they are carried out, from wafer testing to packaged chip evaluations, highlighting the challenges and technological advancements that define their critical role in the electronics industry.
Key Takeaways
- Semiconductor testing is crucial for ensuring the quality, reliability, and functionality of semiconductor devices, which is vital for safe and effective integration into various applications across industries.
- The testing process for semiconductors varies according to the type of device (e.g., integrated circuits, memory chips, wireless devices) and involves advanced Automated Test Equipment (ATE) to handle the complexities and ensure devices meet stringent standards.
- The future of semiconductor testing includes adopting new non-destructive techniques like the laser scanning confocal infrared microscope (LSCIRM) and virtual testing methodologies to enhance reliability and reduce market lead times.
The Importance of Semiconductor Testing
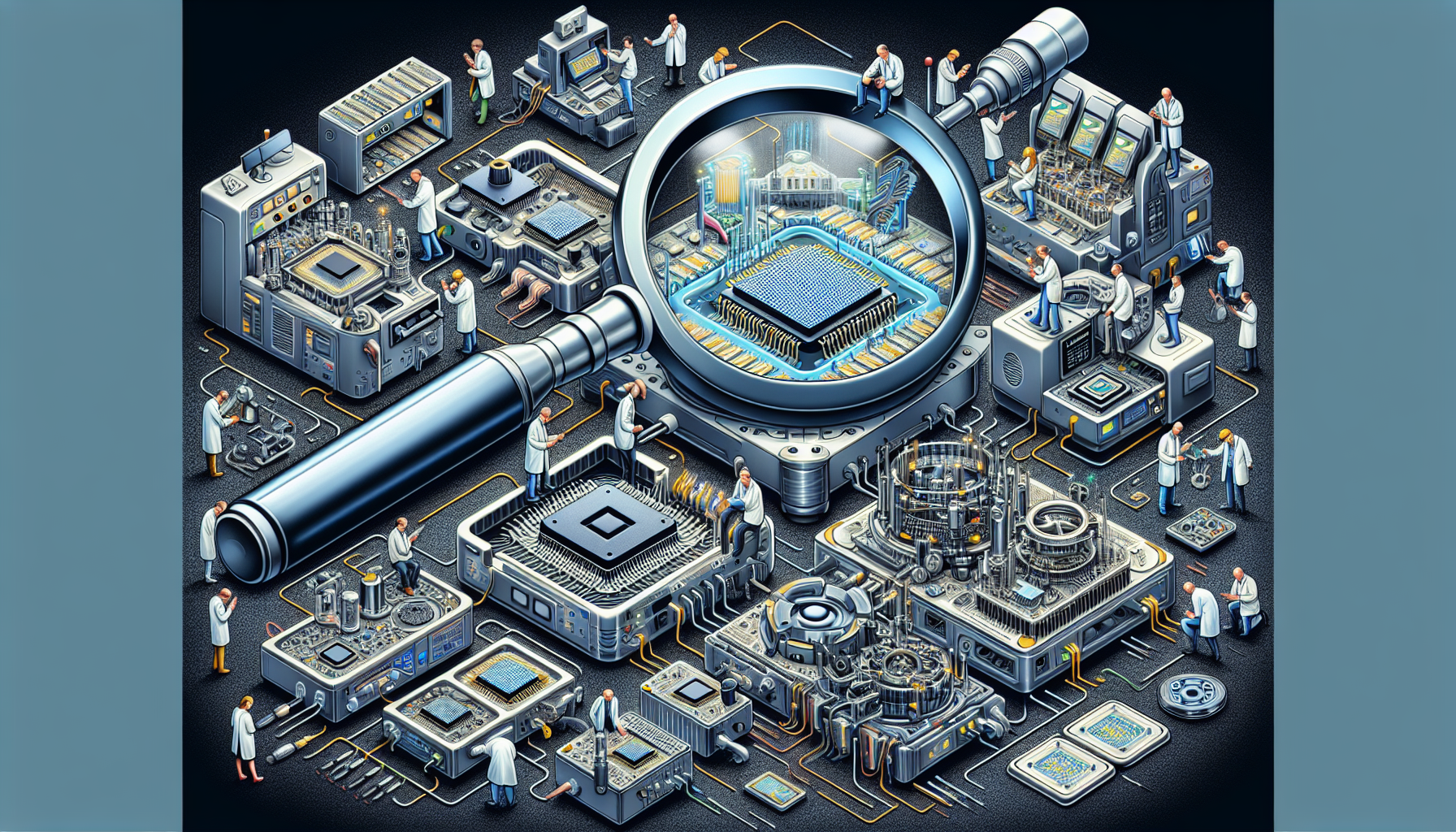
Why do we test semiconductors with such rigor? It is evident that the successful integration of semiconductor devices into numerous applications across different industries hinges on their quality, reliability, and functionality. Imagine the ramifications if an autonomous vehicle’s semiconductors failed to perform as expected. It’s not just about avoiding massive recalls and financial losses; it’s about preventing safety hazards that could put lives at risk.
The journey of semiconductor testing has evolved from simple functionality checks to complex assessments across multiple parameters. Such evolution is imperative, allowing devices to meet their specified purpose and perform reliably under real-world conditions. With every defect identified early in the testing process, the likelihood of failure in the final product dwindles, bolstering the overall reliability of semiconductor devices. It is this relentless pursuit of excellence that underpins every aspect of the semiconductor industry.
Types of Semiconductor Devices
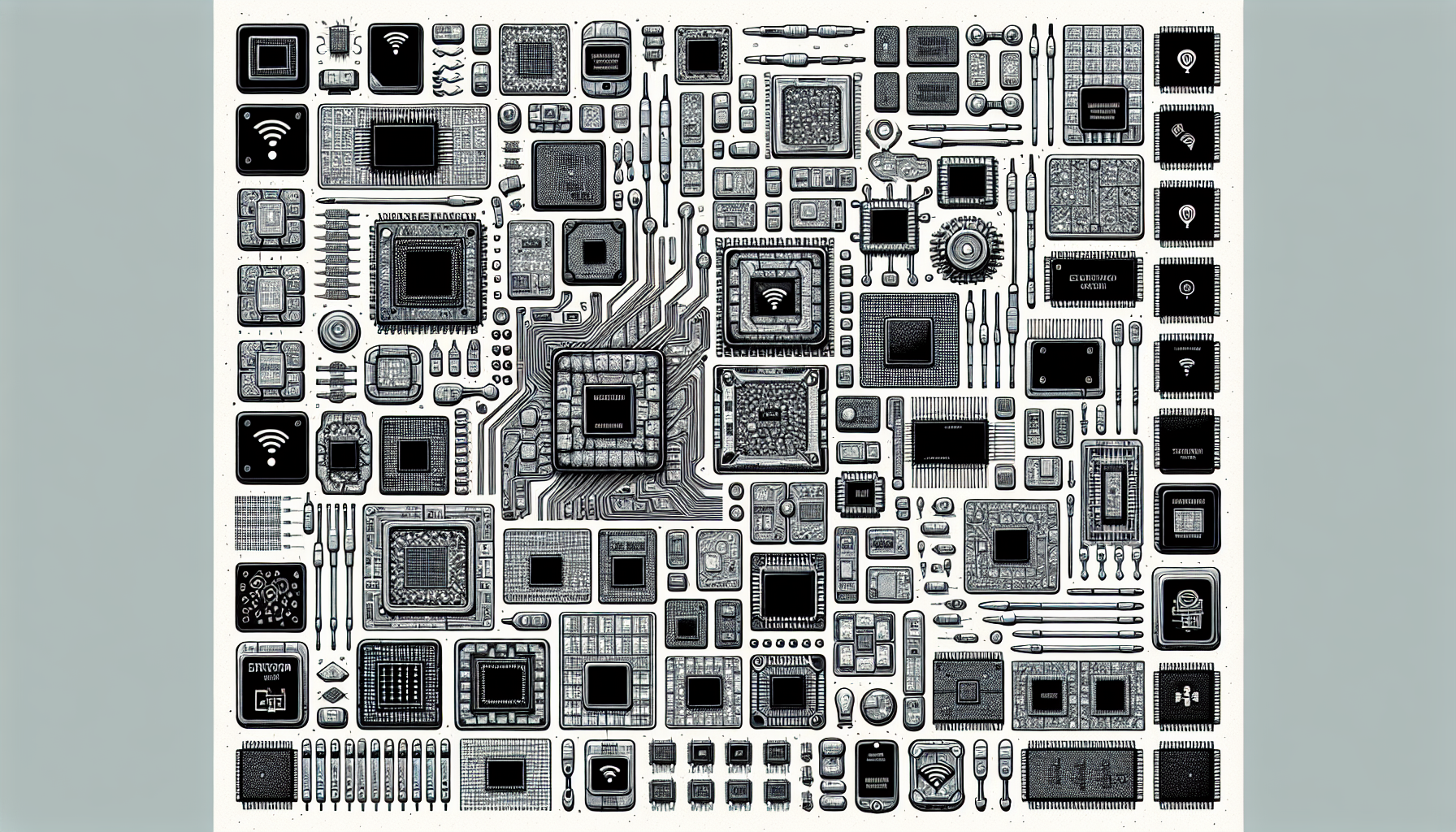
Semiconductor devices come in a variety of forms, each with its own set of complexities and testing requirements. From the brain-like integrated circuits that control most of our electronic devices to the memory chips that store our precious data, and the wireless devices that keep us connected, the semiconductor industry is a tapestry of innovation. The process of semiconductor assembly plays a crucial role in bringing these technologies to life, and semiconductor companies are at the forefront of this progress.
Rigorous testing is mandatory for each type of device to confirm they meet the stringent standards required for their particular applications.
Integrated Circuits
At the forefront of electronic components are integrated circuits (ICs), the complex assemblies of transistors, resistors, and capacitors interconnected on a semiconductor wafer to form complete electronic systems. These tiny powerhouses come in various types, including:
- logic gates
- op-amps
- voltage regulators
- microprocessors
Each tailored for specific tasks within a broad range, including flat panel display technology, that keep our digital world ticking.
ICs, whether powering a smartphone or guiding a satellite, play a crucial role in our daily lives and require a sophisticated package test process, matching their design complexity, to guarantee flawless functionality in every scenario, from the industrial floor to the pockets of consumers.
Memory Chips
Memory chips are the custodians of information in the digital age, with types like DRAM and flash memory serving different storage needs. Each type of memory chip has its unique characteristics, necessitating tailored test solutions. For instance, testing for flash memory often involves ensuring data retention and endurance, while DRAM tests focus on access speed and refresh rates.
However, the advent of technologies like 3D NAND has compounded the complexity of testing, presenting new challenges such as increased test costs and extended test times due to scaling densities and faster data rates. Nevertheless, specialized Automated Test Equipment (ATE) has stepped up, capable of performing parallel tests to increase throughput and guarantee that these memory guardians function perfectly throughout their lifespan.
Wireless Devices
Wireless devices are the conduits of modern communication, yet they present unique testing challenges that researchers and companies like NI are striving to overcome. With a focus on industry-leading bandwidth for wireless standards like 5G NR and Wi-Fi 6, solutions are being developed to meet the demands of innovative products and accelerate their path to market.
The escalating complexity of these devices necessitates advanced test equipment capable of:
- validating their performance
- ensuring a harmonious operation of hardware, software, and services
- providing the seamless connectivity expected by customers.
Key Stages in Semiconductor Testing
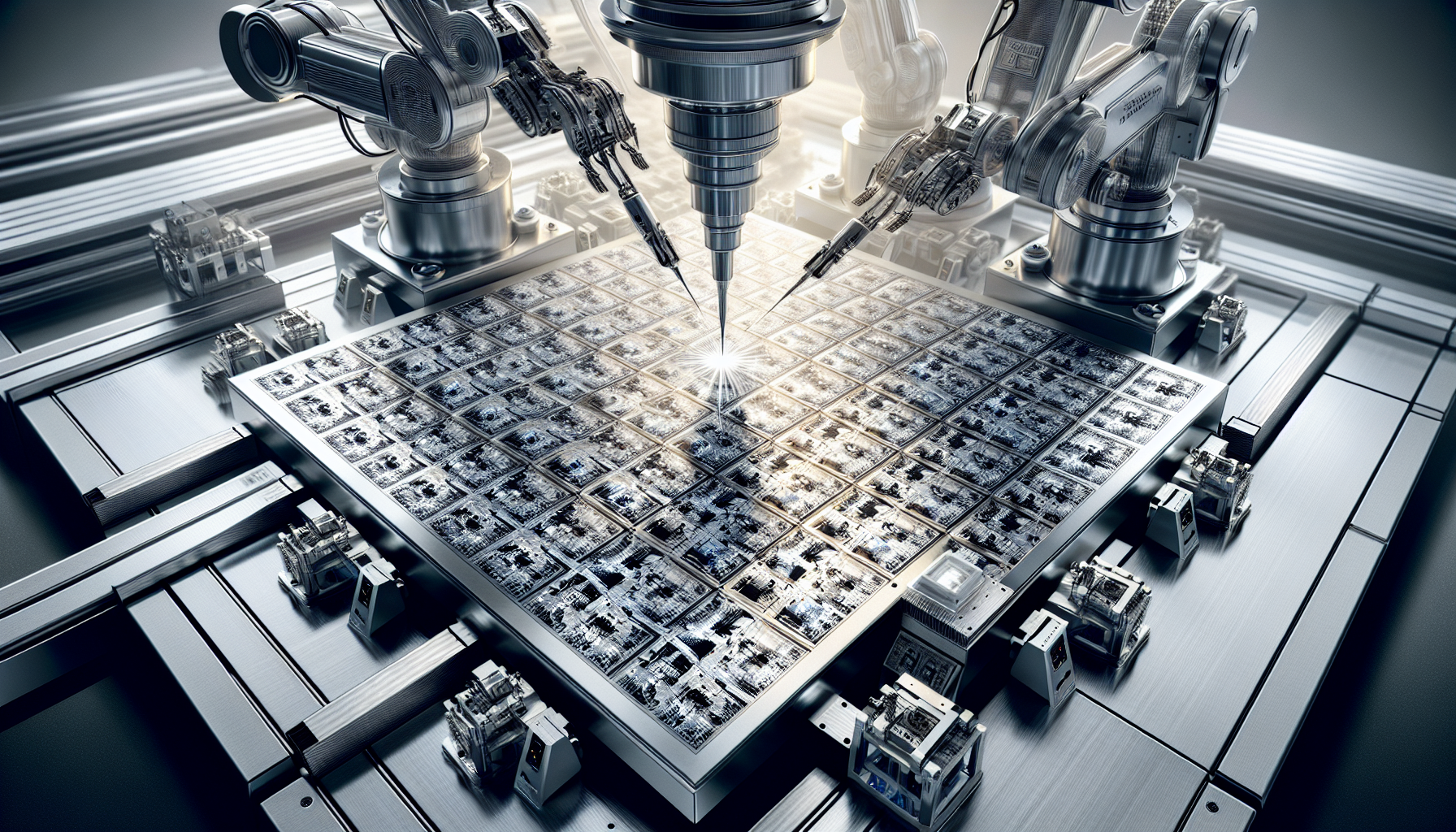
Semiconductor testing is a multi-stage odyssey, beginning with wafer testing, where the die undergoes scrutiny directly on the semiconductor wafers using Automatic Test Equipment (ATE) to check its electrical properties. This stage is pivotal in determining the yield—a metric influenced by variables such as process nodes, defects, and environmental factors. A series of tests, including Scan, Power Integrity, and Thermal Tests, are conducted to guarantee the supreme quality and efficiency of the semiconductor devices.
Following wafer testing, package testing takes center stage, where encapsulated chips are validated for functionality and performance within their intended environments. Metrics like defective parts per million (DPPM) and defect density (DD) are employed to gauge the reliability necessary for critical applications, ensuring that the semiconductors are up to the task for sectors demanding the utmost precision, such as aerospace and automotive.
Semiconductor Test Equipment and Technologies
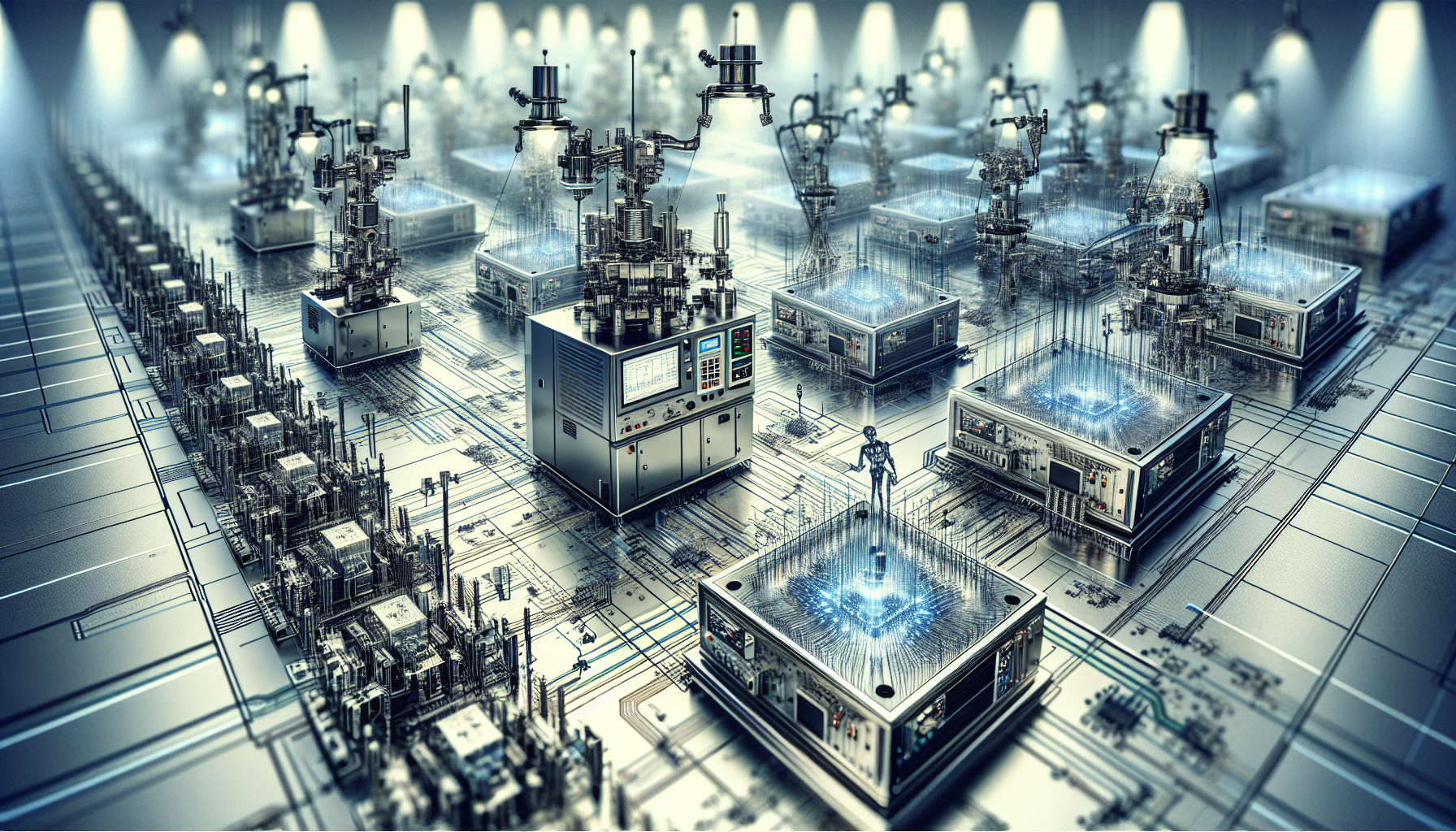
Automated Test Equipment (ATE), complex systems controlled by computers or workstations that enable simultaneous testing of multiple devices, form the core of semiconductor testing. These systems are designed to be flexible, exemplified by platforms like the Semiconductor Test System (STS), which cater to the testing of RF, mixed-signal, and MEMS semiconductor devices. Tests are broadly categorized as functional, ensuring that a chip performs all its intended functions, and structural, aimed at uncovering any manufacturing flaws.
Parametric tests measure critical electrical parameters, such as current and voltage levels, which are essential in interpreting electrical signals. These tests play a significant role in the testing process. ATE is particularly advantageous in sectors like 5G communications and high-performance computing, where it not only reduces testing times but also ensures uniformity, thereby generating cost savings and guaranteeing consistent quality.
Challenges and Solutions in Semiconductor Testing
Semiconductor testing is riddled with challenges, but there is a solution to be found for every obstacle. Artificial Intelligence (AI) optimization, for instance, has revolutionized the testing landscape by reducing the number and volume of test patterns, making the process more cost-efficient and beneficial for both producers and consumers. AI-driven Design for Testability (DFT) planning has compressed design cycles from months to days, streamlining semiconductor production and enhancing cost-effectiveness.
Cost-effectiveness extends to the equipment itself, with a keen eye kept on budget constraints to ensure that the investment aligns with the financial goals of the company. In the wireless sector, particularly, AI optimizations have proven vital in enhancing production test throughput, addressing the pressing time-to-market demands. Moreover, environmental and mechanical stress testing has become essential in verifying the resilience of semiconductors under extreme conditions, ensuring that these tiny components can withstand the rigors they’re subjected to.
The Future of Semiconductor Testing
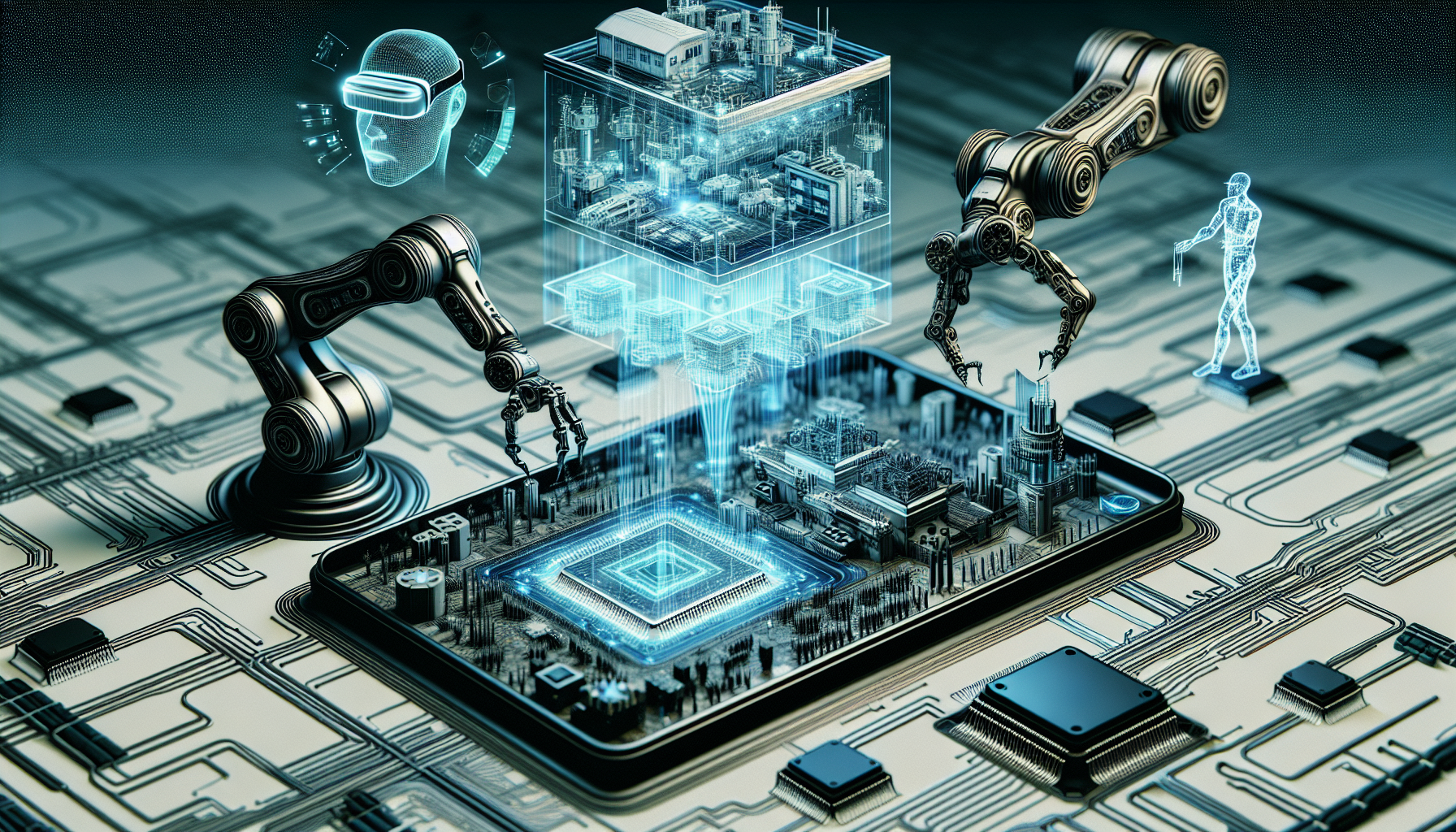
Alongside the progress of the semiconductor industry, the future of testing promises exciting advancements and innovative methodologies. With devices becoming smaller and performance expectations soaring, new testing techniques are being developed to ensure the reliability and quality of semiconductors. One such innovation is the laser scanning confocal infrared microscope (LSCIRM), which promises non-destructive testing of semiconductor structures, capable of detecting internal defects without special environmental conditions.
Staying updated with industry standards and emerging technologies is paramount for informed decision-making regarding semiconductor fabrication inspection equipment. Virtual testing methodologies are poised to revolutionize product development, allowing for the early detection of potential issues and reducing time to market for semiconductors.
Selecting the Right Test Solutions for Your Needs
The selection of appropriate test solutions, including analog testers, requires a careful balance between customization needs and scalability. Selecting test equipment that can accommodate various production demands is as crucial as the tests themselves. Custom tests, designed to assess specialized features of semiconductor devices, are tailored to meet the unique requirements of a diverse array of applications.
Flexible production test platforms, like STS, offer scalability that can adapt to growing production demands or be dialed back to fit within budget constraints, making them ideal for microcontroller-based IoT devices and other semiconductor products.
Case Studies: Successful Semiconductor Test Implementations
Real-world success stories offer compelling evidence of the impact optimization and quality control can have on semiconductor testing. IBM’s Bromont facility, for instance, developed a next-generation optimization-based planning system, leading to enhanced efficiency and optimized production. Similarly, a major chip manufacturer leveraged IBM Decision Optimization technology to improve their long-term planning, thereby optimizing production efficiency and enabling partial order fulfillment.
Some examples of how companies have utilized optimization-based systems and strategies to improve their manufacturing processes include:
- A PCB manufacturer addressed bottlenecks in manufacturing by considering sequencing rules and material availability for effective production planning.
- A semiconductor company increased their test equipment utilization to avoid the costs associated with acquiring new equipment.
- Nexperia implemented rigorous quality control measures, resulting in a significantly low product failure rate.
These examples demonstrate the benefits of a well-executed testing strategy, including functional tests, and optimization-based systems in improving manufacturing efficiency.
Best Practices for Optimizing Semiconductor Test Processes
The optimization of semiconductor test processes is a craft that necessitates profound technical knowledge, strategic process enhancement, and a teamwork approach. A profound understanding of manufacturing processes and device behavior is essential for enhancing yield and reducing test time. By eliminating redundant steps in manufacturing and testing, process optimization can be achieved, leading to more efficient semiconductor test operations.
Cross-functional collaboration between design, manufacturing, and quality assurance teams is critical for holistic improvements in semiconductor test processes. Staying abreast of the latest technologies and methodologies ensures continuous yield improvement and reduced test times. Furthermore, making data-driven decisions based on test data is a cornerstone practice for improving design and overall manufacturing processes within the semiconductor production ecosystem.
Summary
As we’ve navigated through the complex world of semiconductor testing, one thing remains clear: the meticulous process of testing is the backbone of the semiconductor industry, ensuring that every device performs to its highest potential. From the varied types of semiconductor devices to the advanced equipment and technologies that test them, each aspect of this process plays a critical role in maintaining the integrity and reliability of the electronics that power our lives.
The future of semiconductor testing is bright, with innovations on the horizon that promise to further enhance the quality and efficiency of these crucial processes. As technology continues to evolve, so too will the methods by which we test and validate the semiconductors at its core. It’s a never-ending quest for perfection that drives the industry forward, ensuring that the digital world remains a safe, reliable place for all.
Frequently Asked Questions
What is semiconductor testing?
Semiconductor testing is a crucial process involving assessing functionality, performance, and reliability of semiconductor devices before integration into electronic products. It ensures that semiconductor chips meet specified standards before being shipped to customers.
What is a function test for a semiconductor?
A function test for a semiconductor involves determining if the chip performs its intended functions correctly by verifying its operation according to design specifications and checking features like logic, input/output functionality, and overall performance in real-world scenarios.
Why is semiconductor testing important?
Semiconductor testing is important because it ensures high-quality devices enter the market, preventing subpar components from compromising electronic systems' reliability and reducing the likelihood of device failures. This ultimately increases their overall reliability.
What are some of the different types of semiconductor devices?
Some of the different types of semiconductor devices include integrated circuits, memory chips, and wireless devices enabling communication technologies such as 5G and Wi-Fi. These devices play vital roles in electronic systems and data storage.
What equipment is used in semiconductor testing?
In semiconductor testing, Automated Test Equipment (ATE) is primarily used. ATE includes complex computer-managed systems capable of testing multiple devices simultaneously and can be tailored to test a wide range of semiconductor devices for various parameters.