Understanding carbon composite resistors, critical components in various electronics, means looking at their construction and utilization of the “carbon composite resistor.” They are built from carbon particles and nonconductive materials and are valued for both their performance and affordability. This article dives into the intricacies of the carbon composite resistor, compares them with alternatives, and suggests ways to maintain them effectively, thereby offering a clear picture for anyone invested in the practical aspects of electronic design.
Key Takeaways
- Carbon composite resistors are made from a mix of fine carbon particles, binder, and undergo a manufacturing process that includes pressing the materials under high pressure and temperature, attaching leads, applying a protective coating, and finalizing resistance values.
- The performance characteristics of carbon composite resistors include their ability to handle high energy pulses, the impact of temperature on resistance (negative temperature coefficient), and low inductance, making them suitable for applications with high power surges and fluctuations.
- Despite newer technologies, carbon composite resistors remain relevant due to cost-effectiveness and ability to withstand high energy pulses, with specific applications in surge protection, high voltage power supplies, and medical devices.
Unveiling the Carbon Composite Resistor
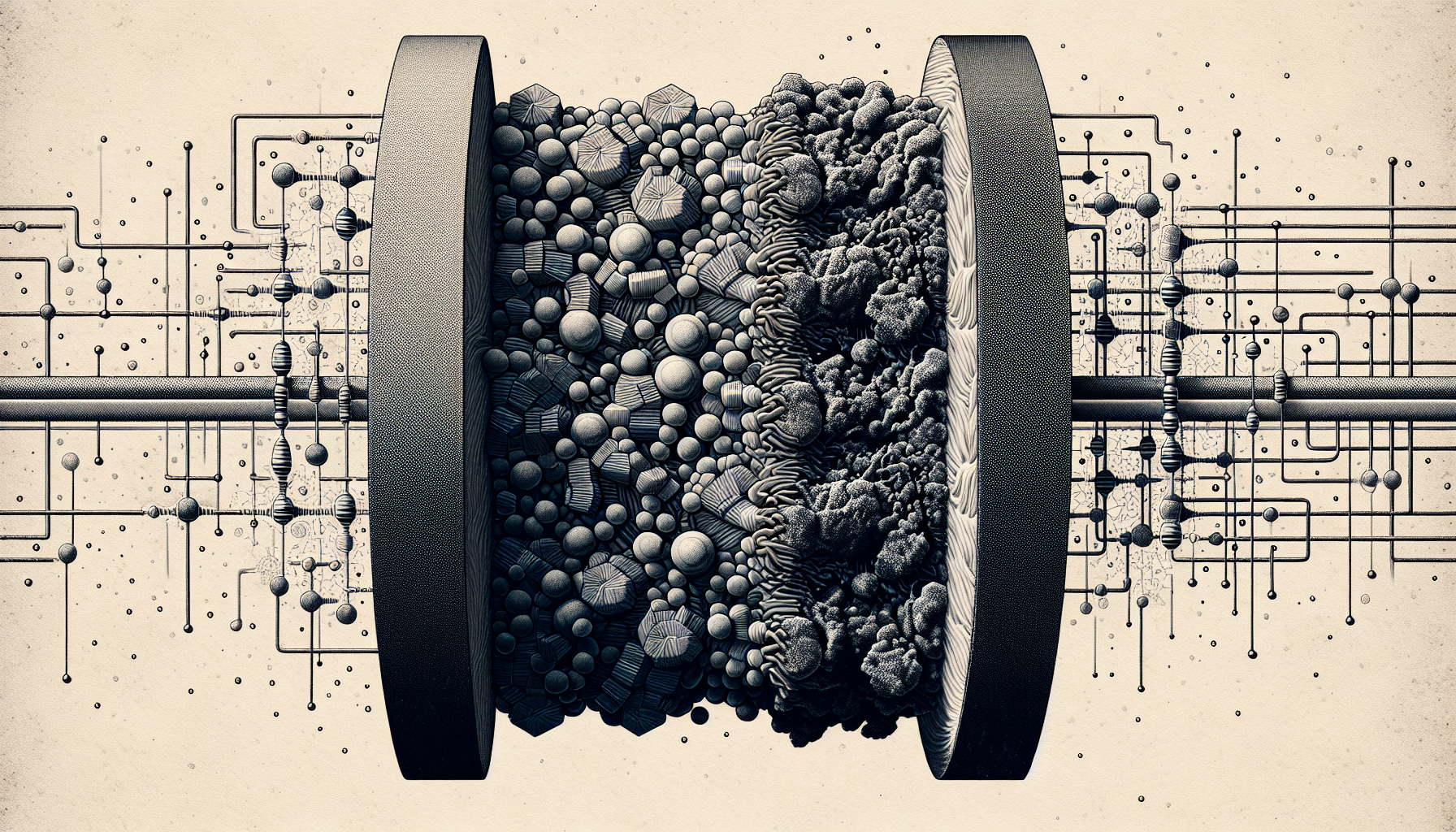
Carbon composite resistors, also known as carbon comp resistors, are marvels of miniature engineering. They are composed of fine carbon particles bonded together with a nonconducting binder, typically ceramic and resin. The combination of these materials creates a resistor that is both versatile and effective.
In the early days of their manufacture, some versions of carbon composition resistors were produced without any protective coating, despite their porous bodies. This porousness is a direct result of their manufacturing process, which involves blending and pressing carbon particles. It’s a testament to the resilience and adaptability of these resistors that they could function effectively even without a protective shell.
This adaptability has ensured the continued relevance of carbon composite resistors in the world of electronics. Despite the emergence of other types of resistors, such as metal or carbon film, carbon composite resistors continue to play a crucial role in many applications.
Exploring the Anatomy of Carbon Composition Resistors
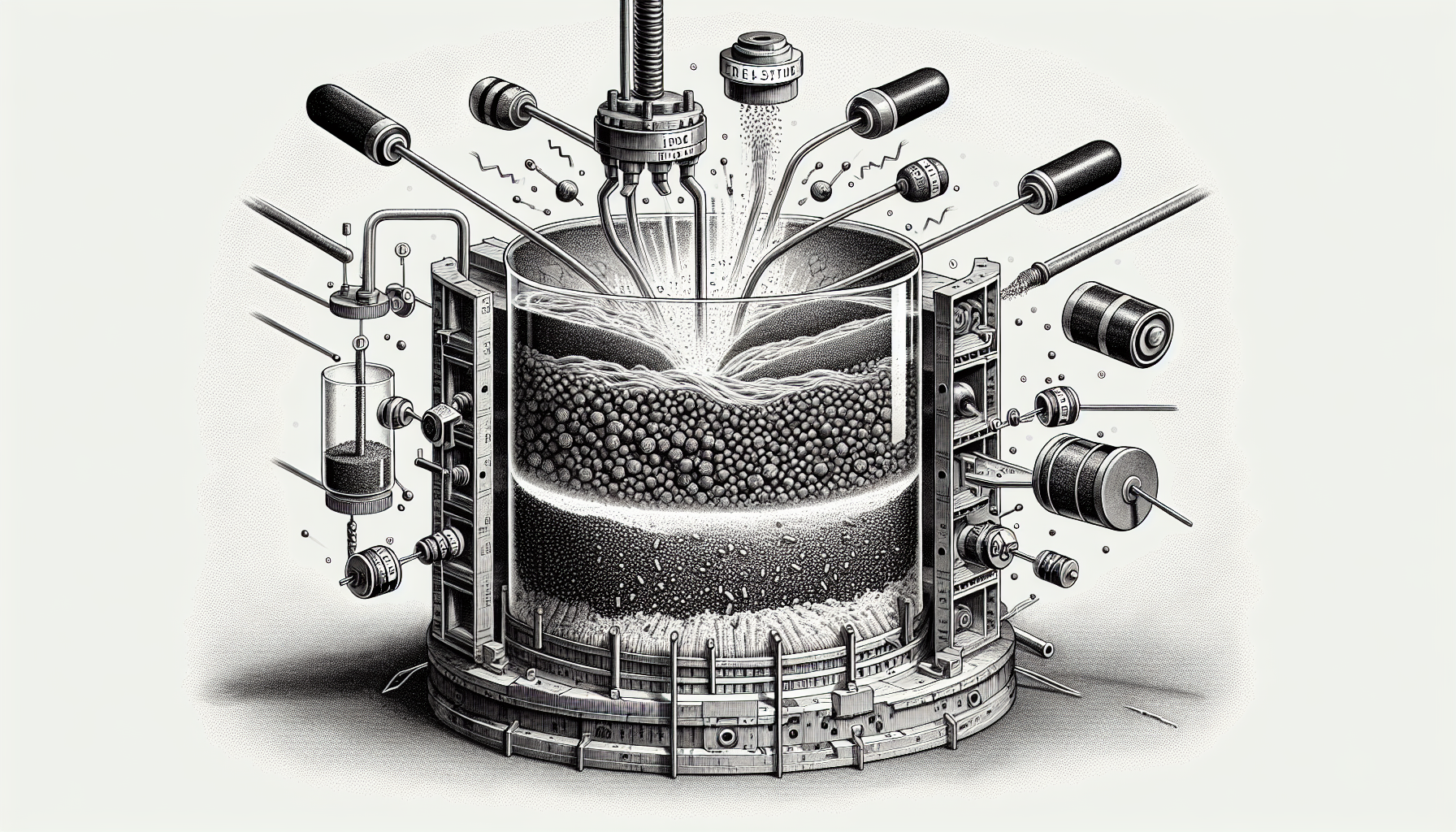
Now that we’ve introduced carbon composite resistors and their basic construction, let’s delve deeper into their anatomy. We’ll explore the intricacies of their manufacture, from the blending of their constituent materials to the final touches that prepare them for use.
Material Mix and Molding
The heart of carbon composition resistors lies in their resistive material, which consists of fine carbon particles mixed with other components. This blend of graphite, ceramic dust, and resin forms the core of the resistor, also known as the resistive element. This blend isn’t just haphazardly combined. It’s carefully balanced and mixed to ensure the final product has the right characteristics.
Once this blend is prepared, it’s pressed under high pressure and temperature into its final form to create the resistor body. This process isn’t merely a matter of shaping; it’s a transformation. The pressure and heat cause the materials to bond on a molecular level, changing the composite from a mere mixture into a cohesive, functional whole.
The result is a solid, cylindrical shape that forms the body of the carbon composition resistor. But this isn’t the end of the process. This newly formed body still needs to be connected to the rest of the electronic components it will serve.
Attaching Leads and Coating
To facilitate the passage of electricity, wire leads are attached to each end of the cylindrical carbon composition resistor body. These leads provide the mechanical contact necessary for the resistor to function properly. Metal caps are fitted on both ends of the carbon composition body to facilitate the attachment of these wire leads.
But connecting the resistor to the rest of the circuit isn’t enough. The resistor’s porous body, while a testament to its unique manufacturing process, is vulnerable to damage and degradation. To protect it, a coating is applied to the resistor body. This coating ensures insulation resistance and durability, safeguarding the resistor’s functionality over its lifespan.
This process of attaching leads and applying coating gives the carbon composition resistor its final form. But there’s one more critical step in the manufacturing process: determining the resistor’s resistance value.
Finalizing Resistance Values
The resistance value of carbon composition resistors is determined by the length of the resistor body and the composition of the graphite mix within the carbon rods. This value is crucial as it determines the amount of electrical current the resistor can handle.
The process of finalizing the resistance value is a delicate balancing act. The length of the resistor body must be carefully adjusted to create the desired path for current flow. Simultaneously, the composition of the graphite mix within the carbon rods can be altered to fine-tune the resistance value.
Once the desired resistance value is achieved, the completed resistor is marked with its particular resistance value for identification. This marking ensures that each resistor can be easily identified and used in the appropriate applications, bringing the manufacturing process of the carbon composite resistor to a close.
Performance Characteristics of Carbon Composition Resistors
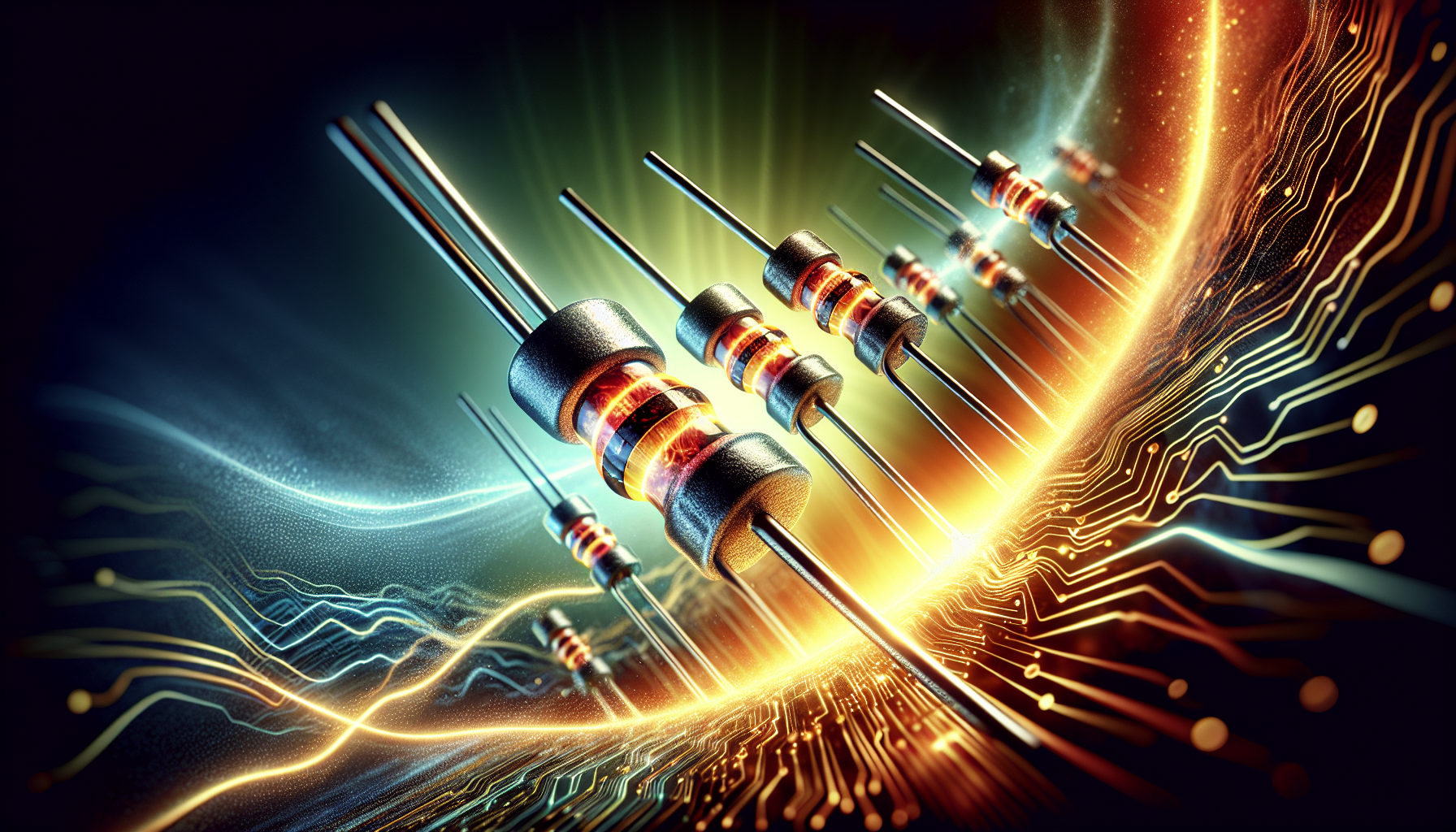
The performance of carbon composition resistors can be summarized by three key characteristics: their ability to handle high energy pulses, temperature sensitivity, and low inductance. These characteristics stem from their unique construction and composition.
Carbon composition resistors, also known as carbon resistors, are renowned for their capability to withstand high energy pulses. This feature makes them suitable for use in various electronic applications carbon composition resistors. This capability is attributed to their greater thermal mass and conducting carbon particles, which allows the entire body of the resistor to conduct energy. This high energy pulse capability makes carbon composition resistors ideal for applications involving high power surges or fluctuations.
However, carbon composition resistors are also noted for their temperature sensitivity, with a strong negative temperature coefficient. This means that their resistance can shift significantly at extreme temperatures, within an operating range of approximately -40 to 150 degrees Celsius. They also exhibit low inductance due to their construction from solid carbon and ceramic material, which limits inductance primarily to the lead components. These characteristics make carbon composition resistors a versatile choice in the world of electronics.
The Unique Advantages and Disadvantages
Like any electronic component, carbon composition resistors come with their own set of advantages and disadvantages. Understanding these can help you decide when and where to use these resistors.
One of the main advantages of carbon composition resistors is their cost-effectiveness. They are less expensive to manufacture at higher resistance values compared to wirewound resistors. They also come in a range of dissipation values, from 1/8 W to 1/4 W, which makes them suitable for various low power applications.
However, they are not without their drawbacks. Carbon composition resistors exhibit higher noise levels when current is passed through them, which can be a significant drawback in some applications. They are also sensitive to temperature fluctuations, which can cause mechanical changes and lead to variations in resistance value.
Compared to other resistor types, carbon composition resistors have the following characteristics:
- Less effective insulation resistance, at around 10^9 ohms
- May not be suitable for scenarios that require low noise
- May not be suitable for scenarios that require stable resistance values over time
Niche Applications for Carbon Composition Resistors

Despite their limitations, carbon composition resistors have carved out a niche for themselves in certain applications. Their unique characteristics make them the ideal choice for specific scenarios.
For instance, carbon composition resistors play a crucial role in:
- Protecting sensitive measurement equipment attached through surge or discharge protection
- Handling high energy pulses
- Being an essential component in high voltage power supplies where stability and high energy pulse withstanding are critical.
Furthermore, carbon composition resistors demonstrate their high energy pulse capability in applications beyond powering electronic systems. They are particularly favored in applications that involve welding and medical defibrillators due to their ability to withstand high energy pulses. These specific applications highlight the versatility and resilience of carbon composition resistors.
Comparing Resistor Types: Where Does Carbon Composite Stand?
While carbon composition resistors have their unique strengths, they are just one type of resistor in a diverse landscape. To fully understand their place, it’s essential to compare them with other types of resistors.
In the past, wirewound and carbon composition resistors were the primary types available until the 1960s. The industry then shifted towards other types like carbon film and metal film resistors. These newer types of resistors offered better temperature stability, lower noise, and were more suitable for high frequency or radio frequency applications compared to carbon composition resistors.
However, that doesn’t mean carbon composition resistors were rendered obsolete. Despite their limitations, they remain less expensive and can be produced at higher resistances than wirewound resistors. For circuits requiring higher stability than what carbon composition resistors can deliver, alternatives such as:
- metal film resistors
- metal oxide resistors
- thin film resistors
- thick film resistors
- wirewound resistors
may be necessary.
This comparison shows that while carbon composition resistors may not be the best fit for every scenario, they continue to hold their own in the world of electronics.
Preserving Your Carbon Composition Resistors
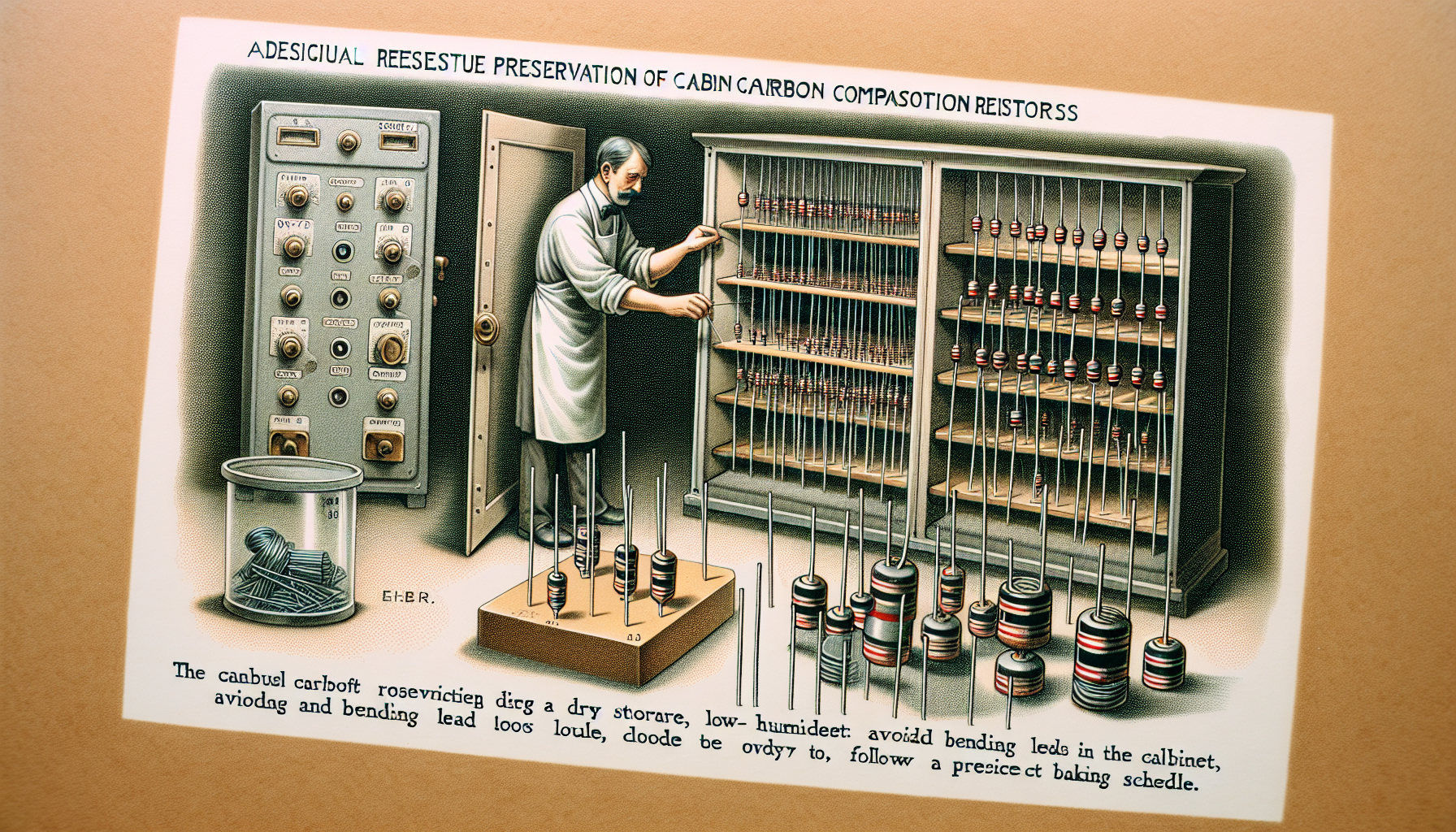
Given their unique characteristics and applications, it’s crucial to know how to properly maintain your carbon composition resistors. Proper maintenance can ensure they continue to perform effectively over their lifespan.
One key aspect of maintaining carbon composition resistors is proper storage. These resistors can experience resistance changes up to 10% due to moisture absorption. Therefore, they should be stored in low humidity areas or dried through convection oven conditioning. Furthermore, avoid bending the leads of carbon composition resistors too close to the body or applying excessive strain, which can cause resistance shifts.
Preconditioning carbon composition resistors through a schedule of baking, like 25 hours at 100°C for 1/8W or 130 hours for 2W, can help remove moisture and stabilize resistance values. Also, avoid exposing these resistors to excessive heat during soldering to prevent a permanent shift in resistance values. Through these practices, you can maximize the durability and performance of your carbon composition resistors.
Summary
Throughout our exploration, we’ve discovered the intricate world of carbon composite resistors. From their unique manufacturing process and characteristics to their niche applications and comparisons with other resistor types, we’ve unveiled the depth of their complexity and versatility.
While they may not always be the best fit for every application, carbon composite resistors continue to play a vital role in the world of electronics. Their unique ability to handle high energy pulses and their cost-effectiveness make them an essential component in specific scenarios. As we venture further into the world of electronics, it’s clear that the humble carbon composite resistor will continue to hold its own.
Frequently Asked Questions
What is a carbon resistor?
A carbon resistor is a type of fixed resistor used to adjust voltage in DC circuits and limit current in AC circuits. It is made of a ceramic carrier with a thin pure carbon film around it. Today, they are rarely used due to low stability and high cost.
How do you make a carbon composition resistor?
To make a carbon composition resistor, you need to blend graphite, ceramic dust, and resin into a resistive material, then press the mixture into sticks under high pressure and temperature, and centrally press connecting wires into both ends of the resistor.
Do carbon comp resistors sound better?
No, carbon comp resistors do not sound better as they tend to create more noise, hiss, pops, and sizzle in amps, which only increases over time. The noise generated is notably less than metal films resistors.
Why carbon composition resistor is mostly used?
Carbon composition resistors are mostly used in high-voltage applications due to their ability to withstand high energy pulses and their small size. This makes them suitable for environments of high stress and they are commonly used in machines such as power transformers and high-voltage communication devices.
How do carbon composition resistors compare to other types of resistors?
Carbon composition resistors are not as popular as carbon film and metal film resistors because the latter offer better temperature stability, lower noise, and are more suitable for high frequency applications. Therefore, carbon composition resistors are not as commonly used as they were before the 1960s.