Navigating the world of electronic component connectors can be daunting, yet these small parts are integral to any electronic system’s functionality. From data transfer to powering devices, connectors come in numerous shapes and sizes, each suited for a specific task. In this comprehensive guide, discover how to identify, utilize, and select the perfect connector to ensure the efficacy of your electronic projects.
Key Takeaways
- Electronic connectors are specifically designed components that interconnect circuits within devices, ensuring efficient electricity and signal transmission with features like polarity, guiding keys, and mechanical locks.
- Different types of connectors, such as USB, HDMI, and RCA, cater to a variety of applications, reflecting their crucial role in powering devices and managing data and audio/video transmission across various technologies.
- Choosing the right connector for a project requires careful consideration of electrical and mechanical specifications, with attention to factors such as voltage, current ratings, contact resistance, environmental conditions, and compliance with industry standards.
Understanding Electronic Connectors
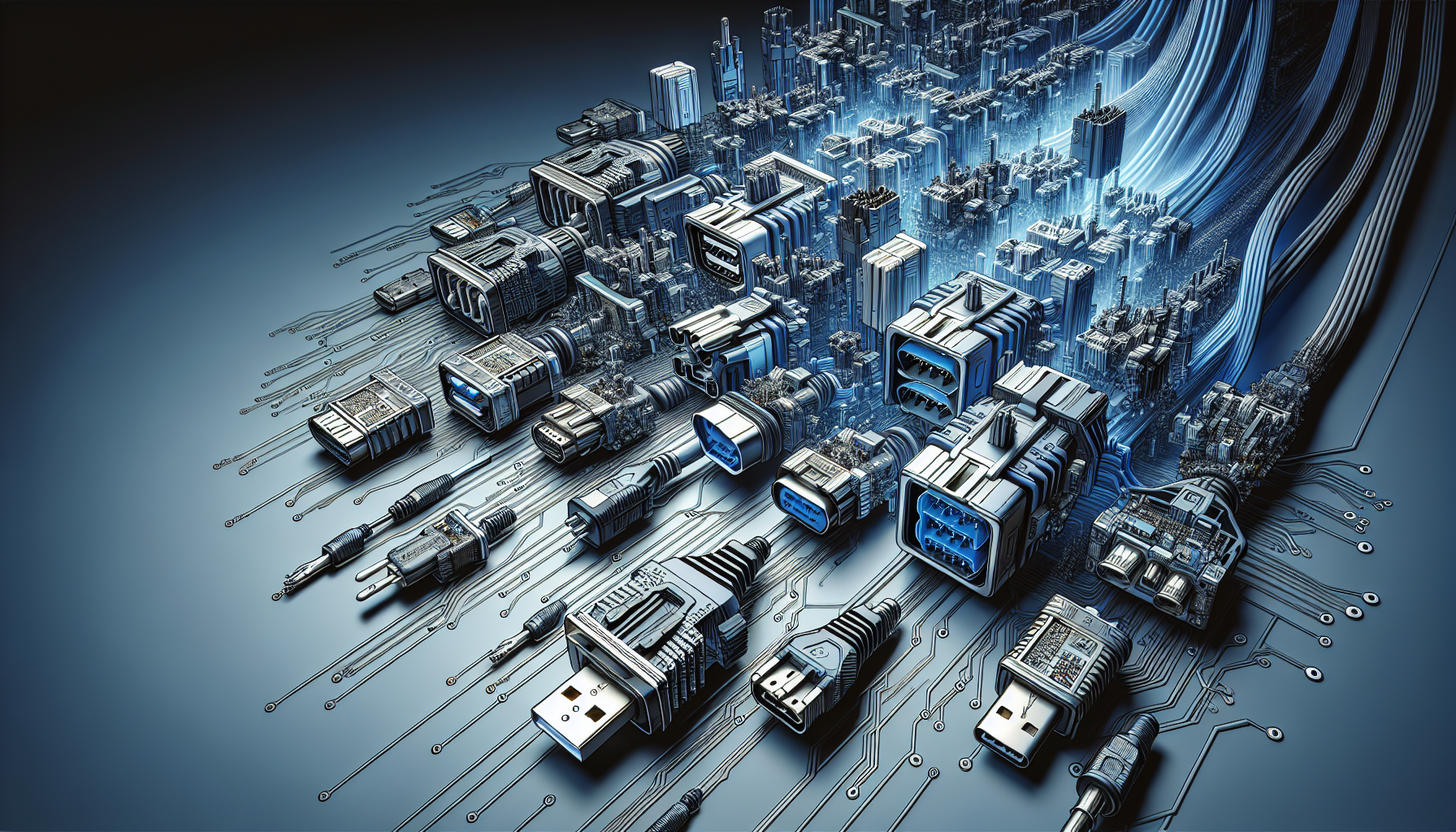
At the heart of every electronic device lies an electrical circuit, a network of interconnected components, and bridging these circuits are electronic connectors, the critical components that ensure a smooth transmission of electricity and signals. These connectors are not just chunks of metal; they’re meticulously designed with gendered components—male connector pins or plugs and female connector sockets—that interlock to form a secure connection. This connection is further refined with user-friendly features such as guiding keys for proper alignment and mechanical locks that click into place reassuringly when the connectors are mated. Polarity plays a pivotal role, allowing connectors to be connected in only one orientation, a safeguard that maintains the integrity and functionality of the electronic circuit.
As we delve into the world of electronic connectors, it’s important to recognize the diversity and specificity of these components. From the ubiquitous USB connectors that have become a staple in consumer electronics to the specialized XLR connectors used in professional audio setups, connectors are as varied as the applications they serve. Each connector type is a result of careful consideration by electronic connector manufacturers, who must balance electrical requirements, mechanical sturdiness, and user convenience.
The quest for high-quality electronic components often leads us to connectors, the gatekeepers of electronic efficiency. They are:
- the bridges between insulated electrical cables and printed circuit boards
- the links that join electronic circuits, including integrated circuits
- the pathways that allow for seamless electronic connections
As we proceed, bear in mind the critical role of connectors in everything from powering devices to transferring data, and consider how even the smallest connector can have a significant impact on the functionality of an electrical device.
Common Types of Electronic Connectors
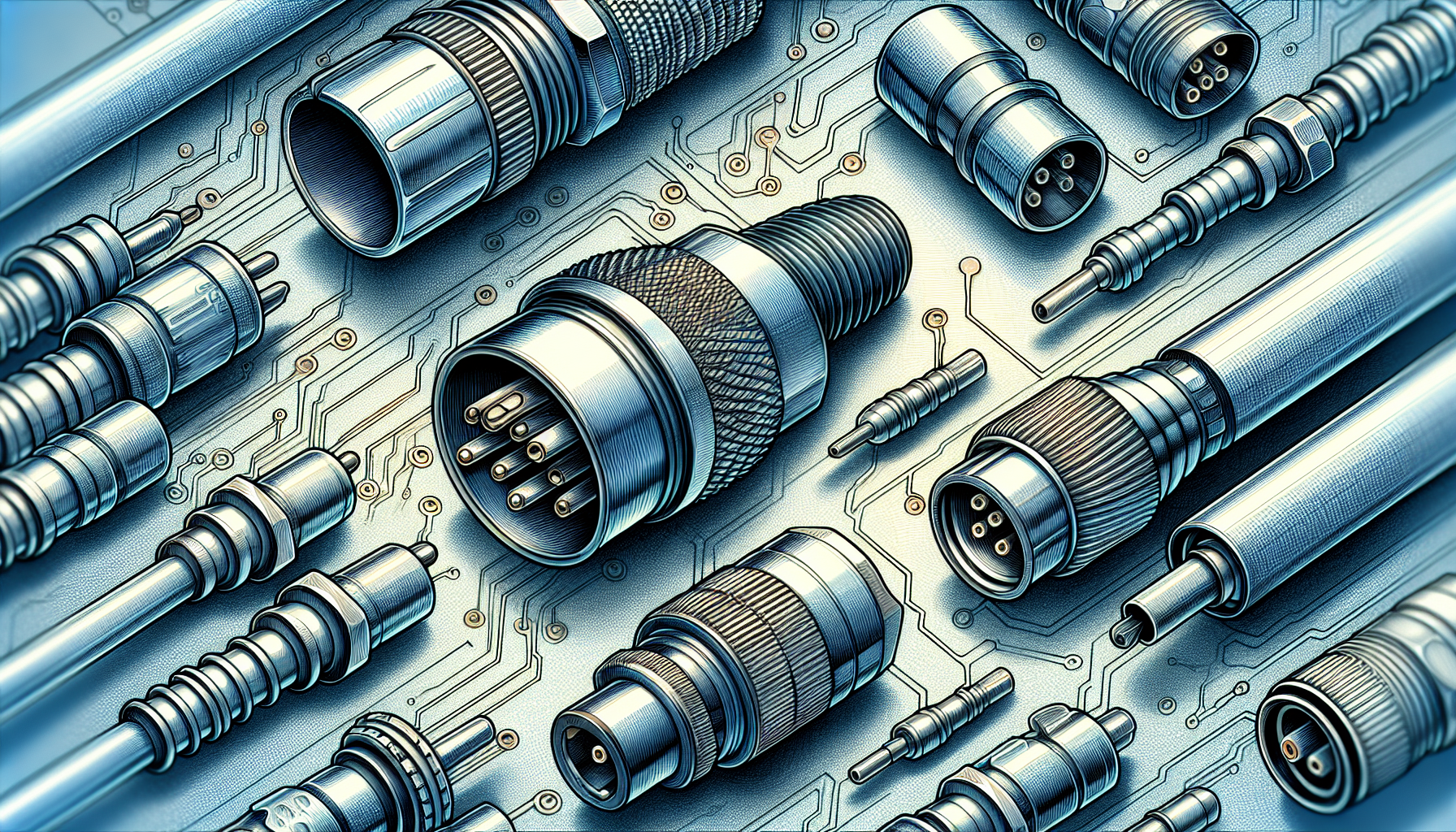
Stepping into the realm of electronic connectors reveals a vast landscape of connector types, each tailored for specific roles within the connectivity ecosystem. Some common types of connectors include:
- Power connectors: designed to carry electrical currents and provide power to devices
- NEMA connectors: a staple in North America, ensuring appliances can connect safely to the electrical utility
- RF coaxial connectors: with their critical role in analog signal transmission, they have become a mainstay in telecommunications, effectively reducing signal losses
These are just a few examples of the many types of connectors available in the market. Each type serves a specific purpose and is designed to meet the unique requirements of different applications.
In the consumer electronics space, barrel connectors are frequently spotted, providing a simple and reliable connection to external power sources. However, it is the ubiquity of USB, HDMI, and RCA connectors that truly showcases the versatility and necessity of these connectors in modern technology. Each connector type, from the power distribution system to the data transfer lanes, plays a unique role in the seamless operation of electronic devices and equipment.
USB Connectors
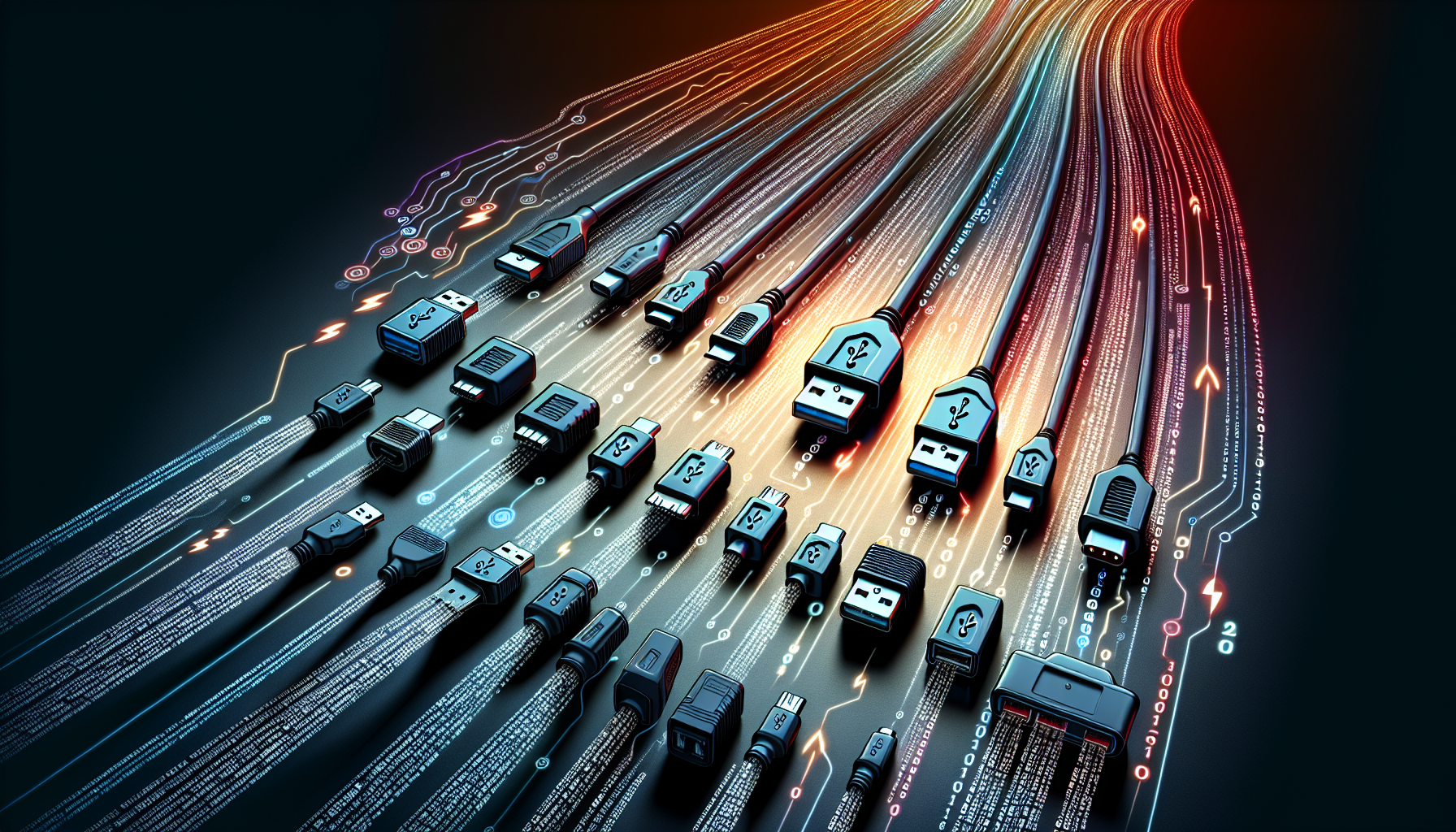
Venturing into the world of USB connectors, we encounter the challenge of navigating a complex array of types, each with its own set of capabilities and compatibilities. The micro USB B connector, for example, has enabled the creation of slimmer mobile devices while supporting USB On-The-Go, allowing for the connection of external devices to smartphones. The USB-C connector, however, is a versatile chameleon, compatible with multiple versions of USB and suitable for both host controller ports and devices.
USB-C has risen as a powerhouse, boasting data transmission speeds up to 10 Gbps, a substantial 100W of power delivery, and alternate modes that cater to DisplayPort and HDMI audio/video signals. It’s no surprise then, that the USB 3.1 C cable, with its reversible design and ability to carry currents above 500mA, is becoming the connector of choice for future-forward devices.
Meanwhile, internal connector cables, such as those for USB 3.0 and 3.1, serve as the unseen conduits linking motherboards to front panel ports with the help of a USB A male connector, a testament to the evolution of USB technology.
HDMI Connectors
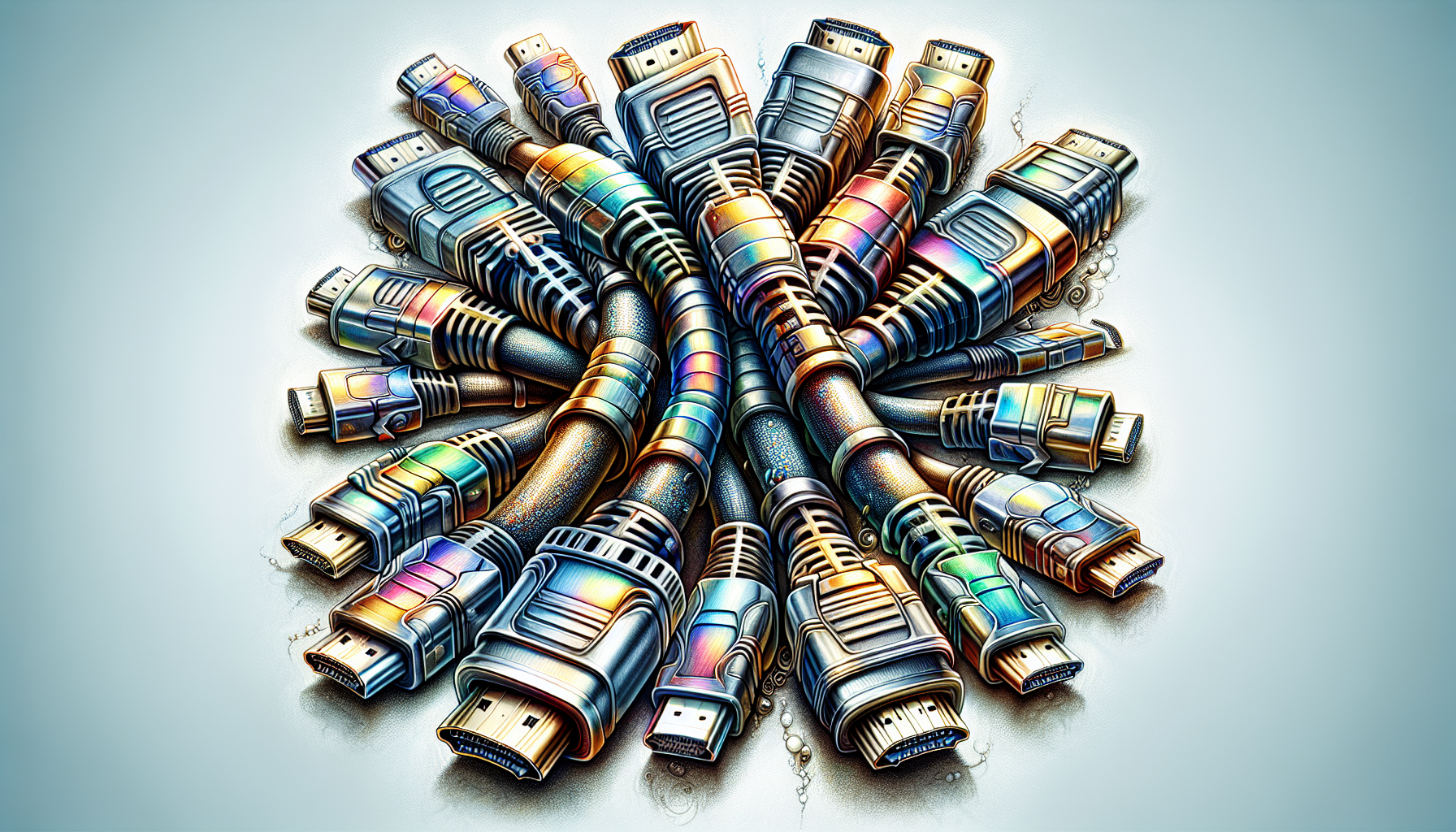
HDMI connectors take center stage when high-quality audio and video transmission is the order of the day. Serving as a vital interface, these connectors enable HDMI cables to carry uncompressed digital signals from a variety of sources to display devices or receivers. Their versatility is evident as they connect an array of devices, including:
- projectors
- game consoles
- TVs
- set-top boxes
Since their introduction, HDMI connectors have evolved, with revisions enhancing their ability to support ever-increasing audio and video quality.
The HDMI landscape is dotted with various connector types, including:
- Type A: the common connector type
- Type C: the compact connector type
- Type D: the diminutive connector type
- Type E: used in automotive applications
While Type B connectors are rarely seen in consumer products, Type E connectors carve out a niche in automotive applications, showcasing the connector’s versatility. The anatomy of HDMI cables typically features male connectors at both ends, ready to interface with their female counterparts recessed into the connected equipment.
RCA Connectors
RCA connectors, with their distinctive color-coded connections, are a familiar sight in the audio and video signal transmission world. They have proven themselves versatile, carrying signals for component and composite video, stereo audio, and even digital audio via S/PDIF, with colors like yellow, red, and white guiding users for easy setup.
The male RCA connectors found on cables and the female connectors located on devices form a reliable and straightforward connection system.
Connector Components and Design Considerations
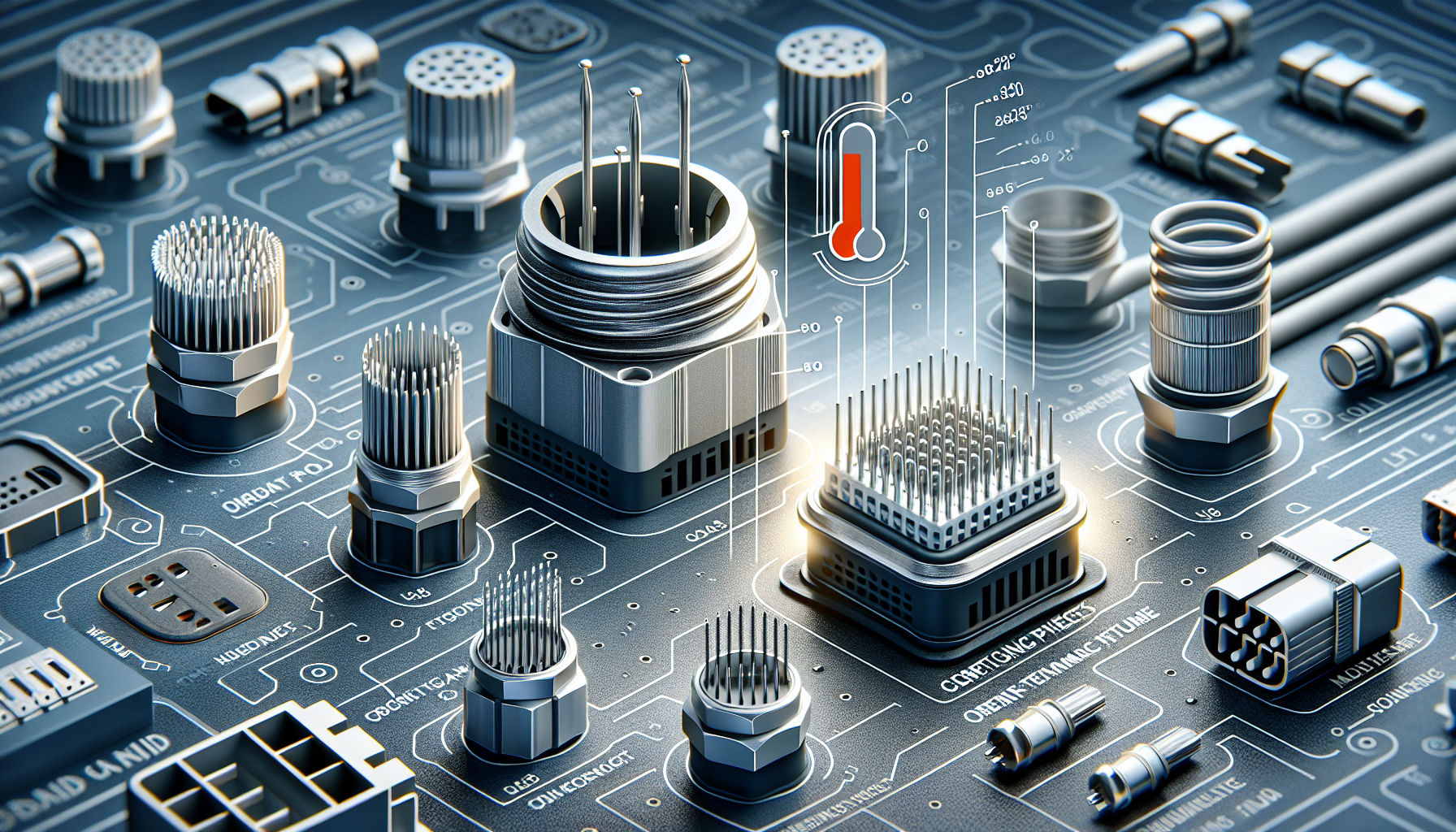
When dissecting electronic connectors, we find that they consist of two primary elements: contacts and housing. Contacts are the metal parts where the electrical magic happens, forming the connection that allows signals to pass through. Housing, encompassing either a plug or a receptacle, provides the structural support that cradles these vital contacts. Connector design is not a frivolous task; it demands a thorough consideration of factors such as contact pitch, which influences the number of contacts per connector area and the likelihood of electrical arcing.
High-voltage applications bring their own set of challenges, such as:
- the need for insulation
- larger pin spacing
- careful consideration of the circuit board size, pin count, wire gauge, and contact sizes
- locking mechanisms and strain relief to ensure durability
- assessment of mating cycles
- environmental factors like ambient temperature and contact plating
These factors all contribute to the design and functionality of high-voltage connectors.
In essence, wire connectors are designed to stand the test of time and environment, ensuring secure connections and the longevity of the electronic equipment where connectors are used.
Connector Mounting and Termination Techniques
The installation of electronic connectors is an art that requires precision and knowledge of various mounting and termination techniques. One such technique involves the use of a surface mount connector, which aligns connector leads with mounting pads on the same side of the PCB, employing soldering methods like re-flow or wave soldering to secure the connector. Meanwhile, through-hole soldering takes a more traditional approach, with connector terminals inserted through pre-drilled PCB holes and soldered on the opposite side for a sturdy connection.
Crimp terminations favor ruggedness and reliability, demanding high-quality crimping tools for effectiveness. Insulation displacement connectors, on the other hand, rely on sharp blades to pierce wire insulation, creating a secure connection without the need for wire stripping. When working with insulated electrical cable, other techniques, such as spring-clamp and push-in terminal blocks, cater to quick terminations, while screw and wire wrap connectors are adaptable to various wire configurations and are especially suited for high-frequency applications.
Press fit connectors offer a solderless option, reducing costs and requiring precision for uniform contact, and barrier terminal blocks maintain connection integrity in high-vibration environments.
Applications of Electronic Connectors
The applications of electronic connectors span across a multitude of industries, underpinning the functionality of devices and equipment with their ability to ensure consistent data transmission and power supply. In the automotive sector, connectors are the linchpins within complex wiring systems, integral to the operation of critical components like the engine and fuel systems. The surge towards electric vehicles has further accentuated the need for electronic connectors that marry precision with cost-effectiveness.
Rugged and waterproof connectors, with their high IP ratings, thrive in harsh conditions where moisture, dust, temperature extremes, and physical impacts are common. The medical field, too, relies heavily on electronic connectors within devices and equipment, where consistent and accurate data transmission and uninterrupted power are non-negotiable for patient care and medical procedures. The burgeoning demands of sectors like 5G communications, electric vehicles, and Industry 4.0 are driving growth in the global connector market, spurring the need for innovative connector technologies.
Choosing the Right Connector for Your Project
Selecting the right connector for a project is a pivotal decision that hinges on understanding both electrical and mechanical requirements. Factors such as voltage and current ratings, contact resistance, and signal integrity are the electrical specifications that define a connector’s suitability for a particular application. Mechanical considerations include the connector’s ability to withstand the temperature range in which it will operate, a factor that can greatly influence performance.
Environmental exposure also comes into play, necessitating connectors that are resistant to chemicals and compliant with industry standards like RoHS and REACH. Furthermore, it’s crucial to choose connectors with a lifespan that matches the application’s expected duration, effectively managing costs without compromising on reliability. By carefully considering these factors, one can ensure that the selected connector not only meets the immediate needs but also delivers sustained performance over time.
Connector Maintenance and Care
The longevity and performance of electronic connectors are significantly influenced by how they are maintained and cared for. Here are some tips for maintaining and caring for electronic connectors:
- Regular cleaning using approved cleaners ensures that dust and dirt, which can lead to poor connections, are kept at bay.
- The application of silicone-based lubricants can help ward off corrosion without attracting further contaminants that cause additional corrosion.
- Dielectric grease, for instance, is an excellent choice for preventing electrolytic corrosion while maintaining the integrity of the electrical connection.
By following these tips, you can ensure that your electronic connectors remain in good condition and perform optimally.
Protective measures for connectors include:
- Applying products like Boeshield T9 every six months to provide ongoing protection against corrosion and keep connectors dry and functional.
- Using dielectric greases tailored for connectors to ease insertion and address contact issues, further safeguarding performance.
- Regularly inspecting for visible damage and using appropriate lubricants to reduce friction and wear, prevent overheating, and protect against operational byproducts.
These measures help ensure the longevity and optimal performance of connectors.
It’s important to note that exposure to harsh chemicals can hasten deterioration, emphasizing the need for preventative care.
Troubleshooting Common Connector Issues
Even with meticulous care, connectors can encounter failures, often due to environmental exposure, mechanical stress, and the wear and tear from continuous connecting and disconnecting. Environmental factors like moisture and vibration can compromise the reliability of electrical connectors, leading to product failures.
Mechanical stress, a byproduct of regular use, can also render connectors vulnerable to damage and necessitate troubleshooting.
Innovations in Electronic Connector Technology
In the fast-paced world of electronics, connector technology is not standing still. The drive towards miniaturization has led to connectors with smaller footprints and higher density, allowing for more connections in increasingly compact devices. High-frequency and high-speed connectors are at the forefront of 5G technology, demanding performance enhancements to keep up with rising data and transmission rates. Innovative materials such as advanced plastics and metal alloys are being harnessed to improve connector durability and reliability.
The integration of wireless transmission capabilities into connector technology, including rf connectors, is a nod to the expanding Internet of Things market, where connectivity is key. These advancements represent a leap forward in the connector industry, promising to meet the evolving demands of technology and signaling a future where connectors continue to play an indispensable role.
Summary
As we conclude this guide, it’s clear that electronic connectors are the unsung heroes that power, integrate, and define the capabilities of our electronic devices. From the basic understanding of their functions to the complex considerations in their design and application, connectors are the crucial links in the vast network of electronic components. The journey through the various types of connectors, their mounting and termination techniques, and their applications across industries underscores the importance of selecting, maintaining, and troubleshooting these components with care and precision.
The innovations in connector technology, driven by the trends of miniaturization and high-speed data transmission, demonstrate the dynamic nature of the field and its readiness to adapt to the future needs of an interconnected world. The knowledge imparted in this guide aims to equip you with a deeper appreciation and understanding of electronic connectors, inspiring you to harness their potential in your own projects.
Frequently Asked Questions
What are connectors in electronics?
Electronic connectors are devices that join electronic circuits by creating an electrical connection between parts of an electrical circuit or between different electrical circuits. They consist of a housing, terminals, and a male (plug) and a female (jack) component. They are used for installing, assembling, and supplying power to electrical devices.
What is the most common type of electrical connector?
The most common type of electrical connector is the crimp connector, which requires a crimp to properly install by bending a metal terminal around a stripped wire. Choose crimp connectors for your electrical needs.
What are P and J connectors?
P connectors refer to the most movable part of a connector pair, often designated as a plug, while J connectors refer to the least movable part, typically a jack. This convention follows IEEE/ANSI guidelines for connector designation.
What are the most important factors to consider when choosing an electronic connector?
When choosing an electronic connector, the most important factors to consider are the electrical and mechanical requirements, including voltage and current ratings, contact resistance, signal integrity, operating temperature range, and environmental exposure. These factors will determine the performance and reliability of the connector in a given application.
Can connectors affect the performance of electronic devices?
Yes, connectors can significantly impact the performance of electronic devices by causing signal loss, power disruptions, and potential device failure.