The electronic components supply chain represents a highly dynamic and complex system that crosses continents, suppliers, manufacturers, and distributors. As manufacturing has become more globalized with just-in-time manufacturing coupled with an increased demand for advanced technologies, managing risks within this supply chain has become more essential than ever. Unexpected disruptions can create costly delays, revenue losses, and diminish customer satisfaction. This blog will aim to give a comprehensive analysis of identifying, managing, and mitigating risks in the electronics component supply chain to ensure business survival and growth.
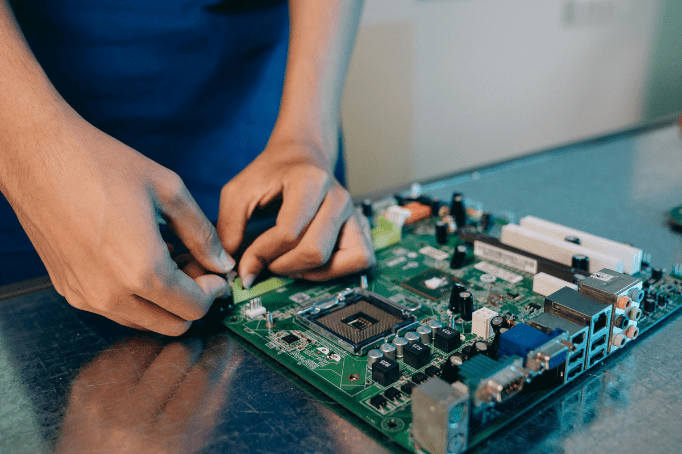
1. Understanding the Key Risks in the Supply Chain
It is important to be well conversant with various types of risks involved before establishing a risk management strategy in a company's electronic component supply chain. In general, these can be categorized along the following lines:
a) Supply disruptions
Supply disruptions happen when manufacturers or suppliers experience problems such as factory closure, natural disasters, or political instability. For instance, the shortage of semiconductors during the COVID-19 pandemic significantly affected the automotive and electronics industries.
b) Quality Issues
Poor or low-quality components may cause failures in products, recalls, and damage to the brand image. Maintaining quality consistency from multiple suppliers is challenging.
c) Counterfeit Components
Counterfeit electronic components are on the rise. Such counterfeit components do not meet the performance requirement but may compromise the safety and reliability of end products.
d) Cybersecurity Risks
Digitization of supply chains introduces the following cybersecurity risks: data breaches, ransomware attacks, and theft of intellectual property.
e) Financial Risks
There is financial instability for the suppliers or distributors, which can lead to bankruptcy or a breakdown in the supply chain.
f) Compliance
Environmental sustainability, trade tariffs, and import/export restrictions may also affect the flow of components across borders.
g) Transportation and Logistics Risks
Inadequate inventory management, high freight costs, or slow transportation may also delay components from reaching their destination at the right time.
2. Proactive Risk Management Strategies
Managing risks in an electronic component supply chain is best approached proactively and holistically. The following strategies are key to risk management by businesses.
a) Diversify Your Supplier Base
Relying on a single supplier can be risky. Develop relationships with multiple suppliers across different regions to reduce dependency and safeguard against localized disruptions.
b) Conduct Thorough Supplier Audits
Evaluate your suppliers for quality, reliability, and financial stability. Regular audits can help identify potential red flags before they escalate into bigger issues.
c) Leverage Technology for Visibility
Invest in supply chain management software to get end-to-end visibility into your operations. Real-time data and analytics can help you monitor inventory levels, track shipments, and identify potential bottlenecks.
d) Quality Control Measures
Implement strict quality control measures to ensure that all components meet industry standards. Ensure that the suppliers collaborate with you so that quality is maintained throughout the cycle of production.
e) Strategic Partnerships
Work closely with your suppliers and distributors to build trust and transparency. Long-term partnerships may bring about better communication, improved quality, and reduced risks.
f) Implement Cybersecurity Best Practices
Protect your supply chain from cyber threats by investing in robust cybersecurity measures. Encrypt sensitive data, conduct regular security audits, and train your team on best practices.
g) Maintain Buffer Stock
While just-in-time inventory systems are efficient, maintaining a buffer stock of critical components can help you avoid disruptions during unexpected supply shortages.
3. Advanced Risk Mitigation Techniques
As supply chain risks evolve, businesses must adopt advanced strategies to stay ahead of potential challenges.
a) Implement Blockchain Technology
Blockchain will make the supply chain much more transparent and traceable. It records every transaction, and the businesses can ensure that components are not from any counterfeited because of an immutable ledger.
b) Utilize AI and ML
AI and ML will predict the potential risk through historical data and identify some patterns. They can also better optimize inventory management along with a better forecast of demand.
c) Develop a Business Continuity Plan
A good business continuity plan is an assurance that your business will run even in the event of major disruptions. This includes identifying alternative suppliers, maintaining emergency stock, and having a crisis response team.
d) Conduct Stress Testing
Simulate worst-case conditions regularly to identify vulnerabilities in your supply chain. With this, you can develop contingent plans and strengthen weak links.
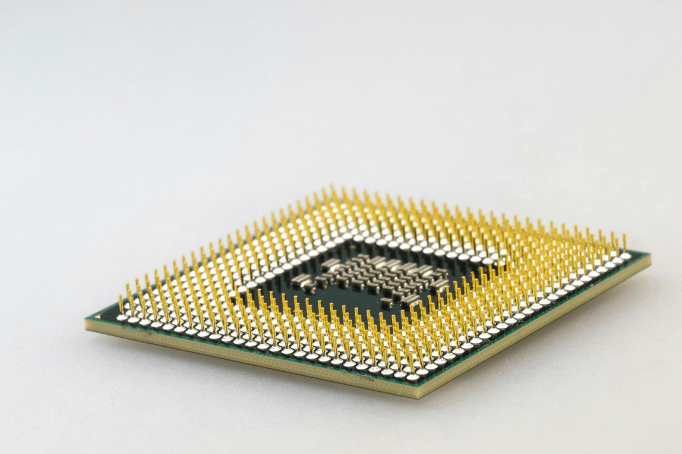
4. Collaboration and communication
Risk management in the supply chain of electronic components is not a one-man show. That is, it requires interaction among several stakeholders, including your suppliers, manufacturers, distributors, and customers.
a) supplier collaboration
Work closely with your suppliers to improve forecasting accuracy and share critical data. Collaboration planning can help mitigate risks and improve efficiency.
b) Internal Communication
Ensure that all departments within your organization are aligned on supply chain priorities. Regular communication between procurement, production, and logistics teams can prevent misalignment and reduce risks.
c) Customer Communication
Keep your customers informed about the potential delays or issues in the supply chain. Transparent communication builds trust and helps maintain good relationships.
5. Case Studies: Lessons from the Industry
a) The Semiconductor Shortage
The global shortage of semiconductors brought to the fore the risks of over-dependence on a limited number of suppliers. Companies that had diversified their supplier base or maintained buffer stock were better placed to weather the crisis.
b) The Impact of Natural Disasters
The Japanese earthquake and tsunami in 2011 disrupted the supply of electronic components worldwide. Companies with alternate suppliers or disaster recovery plans could recover faster.
6. Future Trends in Supply Chain Risk Management
The electronic components supply chain is dynamic, and here are some emerging trends that companies should watch out for:
a) Focus on Sustainability
With the focus on the environmental sustainability of businesses, more and more companies are turning to supply chains that are green and responsible. This includes procuring components from sustainable suppliers and decreasing carbon footprint.
b) Shift Toward Regional Manufacturing
Many firms have shifted their manufacturing base towards regional sourcing to mitigate risks associated with globalization.
c) More Investment in Resilience
Businesses are focusing more on building robust supply chain networks than becoming efficient and investing in high-end risk management technology.
7. Building a Resilient Supply Chain
To build a resilient supply chain, businesses must go beyond risk management to embrace a more comprehensive resilience framework. This includes:
a) Scenario Planning
Conduct stress tests and simulate various risk scenarios to identify vulnerabilities in your supply chain. This proactive approach allows you to develop contingency plans and respond effectively to disruptions.
b) Focus on Sustainability
Sustainability is increasingly becoming a key consideration in supply chain management. Work with suppliers who adhere to environmental and ethical standards, and strive to minimize the environmental impact of your supply chain operations.
c) Adopt Regional Manufacturing
Shifting from a fully globalized supply chain to a regionalized model can reduce lead times, improve control, and minimize the impact of global disruptions.
d) Develop a Business Continuity Plan (BCP)
A strong BCP guarantees that your business can continue operations in the face of supply chain disruptions. This includes the identification of alternative suppliers, establishing crisis management teams, and maintaining emergency stock.
8. Case Studies: Lessons from Industry Leaders
a) Apple's Supply Chain Strategy
Apple is a master in sophisticated supply chain management, with many suppliers for key components and strong relationships with contract manufacturers. Diversification of this kind mitigates risks and ensures business continuity.
b) The Semiconductor Shortage
In the wake of the global chip shortage, companies with strategic inventory policies and diversified supplier networks fared much better than those that depended on a single source.
9. Emerging Trends in Supply Chain Risk Management
The future of supply chain risk management is determined by emerging technologies and changing market dynamics. Emerging trends include:
a) Digital Twin Technology
Digital twins create a virtual replica of your supply chain, enabling real-time monitoring and testing of different risk scenarios.
b) Increased Automation
Automation in procurement, logistics, and quality control can reduce human error and improve supply chain efficiency.
c) Focus on Nearshoring
Nearshoring, or sourcing components closer to home, is gaining popularity as companies seek to reduce dependency on distant suppliers and mitigate global risks.
10. Strategies to Manage Risks in the Supply Chain
Managing these risks effectively involves a combination of proactive planning, collaboration, and the adoption of advanced technologies. Here are some strategies to consider:
a) Diversify Your Supplier Base
It is risky to depend on a single supplier or region for critical components. A diversified network of suppliers spread across different geographic locations reduces the dependency on any single source and minimizes the effect of regional disruptions.
b) Increase Supply Chain Visibility
Visibility is the key to effective risk management. Employ digital supply chain management tools that help track the movement of components in real time, monitor inventory levels, and anticipate potential bottlenecks.
c) Carry Out Periodic Audits on Suppliers
Rate your suppliers against financial stability, control of quality processes, and delivery timelines. Such periodic checks identify vulnerabilities in the process and align the suppliers to achieve your business goals.
d) Invest in Cyber Security
Cyber threats in your supply chain can be neutralized with proper security. Implement the use of firewalls, encryption, and multi-factor authentication to prevent any form of attack on your systems and sensitive data.
e) Ensure Strategic Inventory Levels
Though just-in-time inventory models can be efficient, having a buffer stock of critical components might help mitigate the overall impact when unexpected supply chain disruptions occur.
11. Understanding Risks in the Electronic Components Supply Chain
The electronic component supply chain has a distinct set of challenges. Of course, some of them include:
a) Supply Chain Disruptions
Global supply chains are susceptible to disruptions from natural disasters, pandemics, geopolitical tensions, and trade restrictions. The COVID-19 pandemic, for example, exposed the fragility of global supply chains, resulting in broad shortages of semiconductors and other components.
b) Component Shortages
It so often happens that demand for electronics runs ahead of supply, more specifically at peak growth points of technologies. For instance, the ever-growing demand for electric automobiles and smart devices has fueled periodic chip shortages.
c) Counterfeit Components
The growth in counterfeit electronics poses a significant threat. Faulty parts can cause failure in systems, shorten the lifecycles of products, or compromise safety, thus bringing harm to revenue and brands.
d) Logistical Problems
Delays in transportation, port congestion, and increasing freight costs lead to bottlenecks in the supply chain, delaying production timelines and delivery schedules to customers.
e) Cybersecurity Risks
In light of the digitization of the electronic component supply chain, cyber threats like data breaches and ransomware attacks pose huge risks. Hackers targeting a firm's supply chain management systems may create operational or intellectual property security breaches.
f) Regulatory and Compliance Risks
Changes in trade policies, environmental regulations, and labor laws can upset global sourcing strategies. Compliance with these regulations adds another layer of complexity.
Conclusion
Managing risks in the electronic component supply chain is a multi-dimensional and proactive challenge that calls for strategically proactive action. Businesses will have an opportunity to build a resilient, growth- and innovation-supporting supply chain if proper key risks are understood, technology is adopted, and collaboration is created. As the industry evolves, it will be crucial to remain so and adopt new trends or practices for sustainable long-term success.
Proper risk management, rather than focusing only on disruption, aims at creating an edge. Well-prepared supply chains will always mean that one will respond effectively to challenges and give customers the best value as a product of delivery while standing in a good position in the international markets.