When it comes to the realm of electronics, there’s a silent hero that often goes unnoticed – the printed circuit board assembly (PCB). Deceptively simple in appearance, these intricate mazes of circuits and components are the heart of virtually every electronic device we use. But what goes into creating these essential pieces of technology? Hold onto your hats, as we’re about to embark on an in-depth exploration of PCB design assembly, its significance, and the strategies to optimize its processes.
Key Takeaways
- Proper component placement, spacing, and delivery in PCB design are critical factors that affect quality, functionality, and manufacturability, potentially impacting costs due to rework and redesign.
- The roles of soldering, inspection, and application of Design for Assembly (DFA) principles are essential for optimal performance, reliability, and cost-effectiveness in electronic devices.
- Challenges such as ensuring component availability, handling mixed assembly technologies, and proper board edge clearance can be addressed through careful planning, effective supply chain management, and adherence to design guidelines.
The Importance of PCB Design Assembly
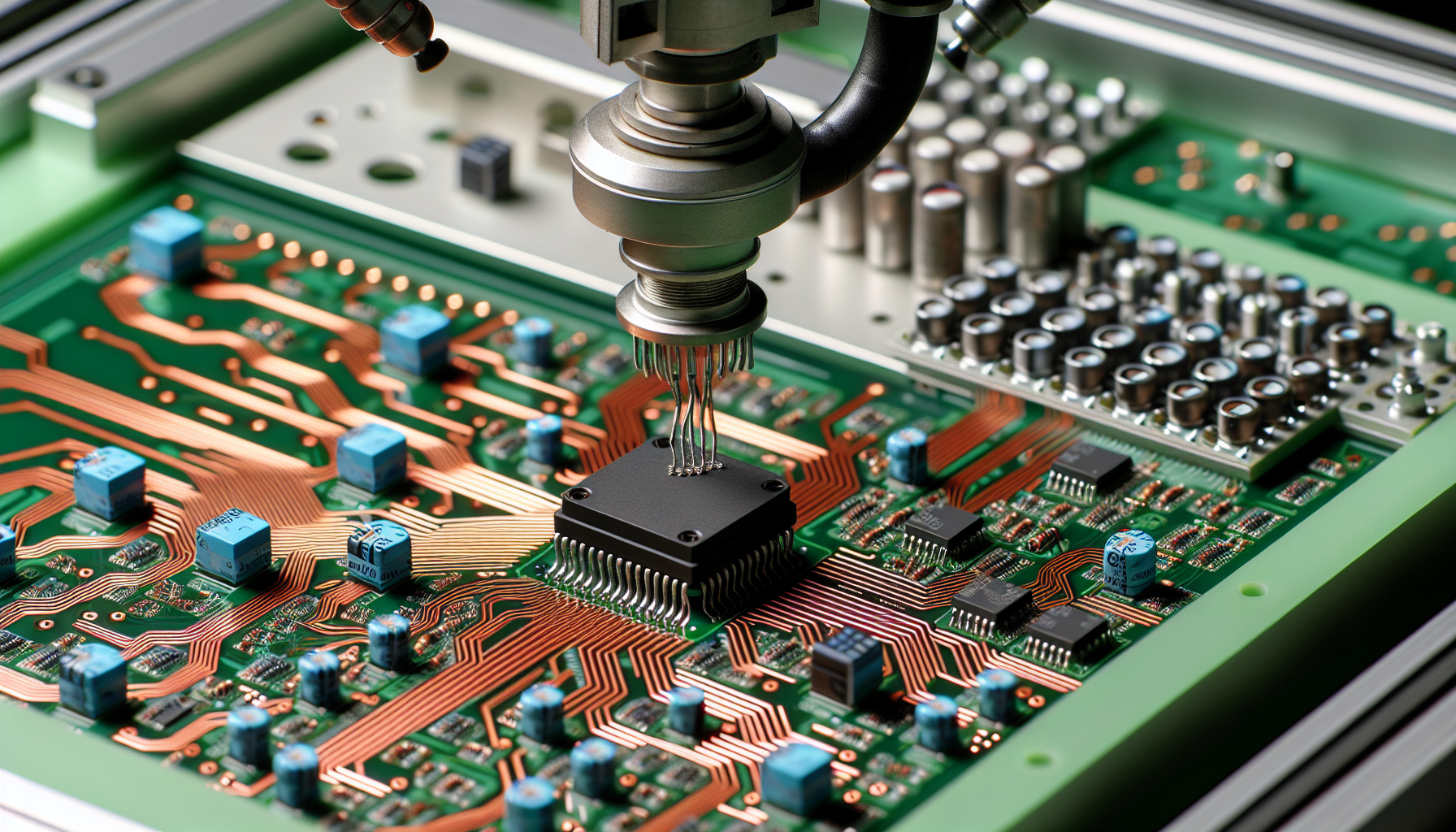
A world without PCBs is a world devoid of most modern conveniences. Imagine a day without your smartphone, laptop, or even your microwave oven. These devices, and countless others, owe their existence to printed circuit boards.
The PCB assembly process is a critical step in the manufacturing process of electronic devices. This process involves:
- Placing various electronic components on the bare board
- Following the printed circuit board design
- Soldering the components onto the board
- Testing the assembled PCB for functionality
The printed circuit board assembly process adds life to the bare PCB, transforming it into a fully functional PCB that can be integrated into an electronic device.
One might question, why is proper component delivery so important in PCB assembly? The success of circuit board design assembly largely hinges on adequate component delivery. It ensures timely availability and accurate integration of components during the assembly process. This directly impacts the performance of the final product’s printed circuit boards.
Aside from component delivery, even simple factors such as part-to-part spacing significantly impact the quality of the PCB assembly. Ensuring adequate part-to-part spacing in printed circuit boards design assembly is crucial to prevent shorts, malfunctions, and the need for re-design and re-fabrication. These issues can lead to substantial time and financial losses. Hence, it’s vital to maintain proper spacing in PCB design.
Role of PCB Assembly in Electronic Devices
Comprehending the role of PCB assembly in electronic devices equates to delving into the DNA of technology. The significance of PCB assembly in electronic devices is paramount, as it plays a critical role in connecting and supporting various electronic components within the device, ultimately enabling the device’s functionality. Without effective PCB assembly, the individual components of your device would remain just that - individual and disconnected.
If PCB assembly is the DNA of technology, then soldering is the glue that binds it all together. Attaining the right soldering temperature is crucial in PCB assembly services. It must be high enough to ensure the solder melts properly, creating sturdy and reliable connections between components and the PCB. Reaching an optimal temperature, usually around 500°F, secures all the components’ connections, substantially boosting the device’s overall durability and performance.
Factors Affecting PCB Assembly Quality
In PCB assembly, quality reigns supreme. How components are placed on a PCB greatly affects the quality of PCB manufacturing. It’s not as easy as simply sticking components wherever there’s space. Factors such as:
- signal integrity
- power distribution
- thermal management
- manufacturability
all need to be considered to optimize component placement.
The inspection process is another key element with a significant influence on the quality of PCB assembly. This process aids in identifying and rectifying defects or issues early on, thereby enhancing the overall soldering process and guaranteeing that the final product meets the necessary quality standards. In essence, a thorough inspection process acts as a quality control checkpoint, ensuring that the PCB assembly is free from defects and ready to perform its intended function.
Essential Elements of PCB Design Assembly
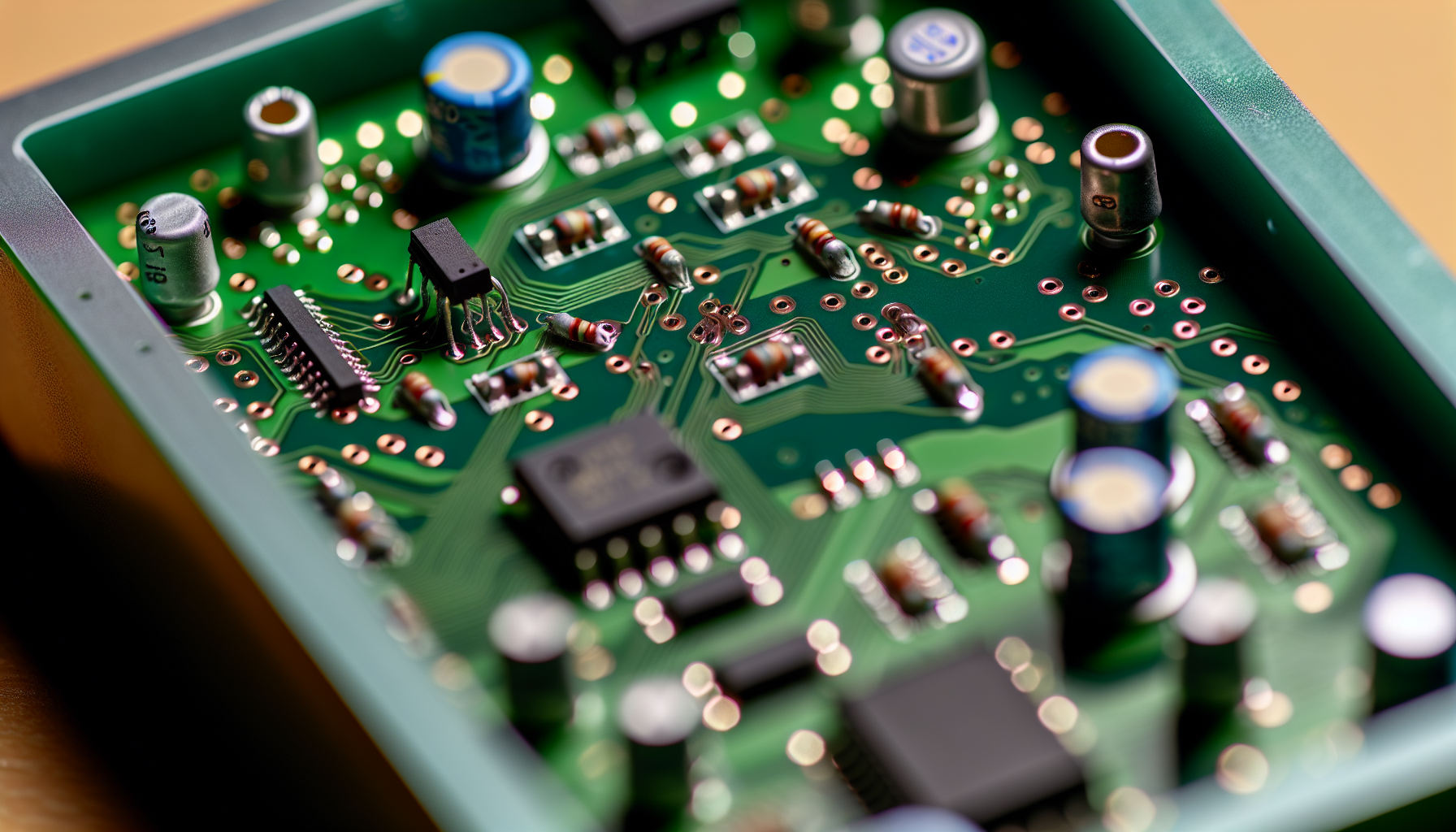
Having understood the significance of PCB design assembly and the factors that affect its quality, we can now delve into the key elements constituting the PCB assembly process. When it comes to PCB design assembly, there are three main elements that hold the key to a successful assembly process: component placement strategies, soldering techniques, and inspection and testing.
Choosing a suitable package size is vital in PCB assembly. It can help avoid complications during the PCB fabrication process and free up additional space on the board. For instance, it is advantageous to opt for a 0402 size capacitor/resistor over a 0201 whenever feasible, as it ensures improved handling and placement during assembly. This seemingly small decision can have a huge impact on the assembly process, influencing everything from manufacturability to the overall performance of the final product.
Utilizing machines for the pick and place process is another crucial aspect of the PCB assembly process. Machines offer enhanced accuracy and consistency compared to human labor, leading to a more dependable soldering and assembly procedure. This level of precision is crucial in preventing mistakes that could otherwise lead to malfunctioning devices or expensive rework.
Component Placement Strategies
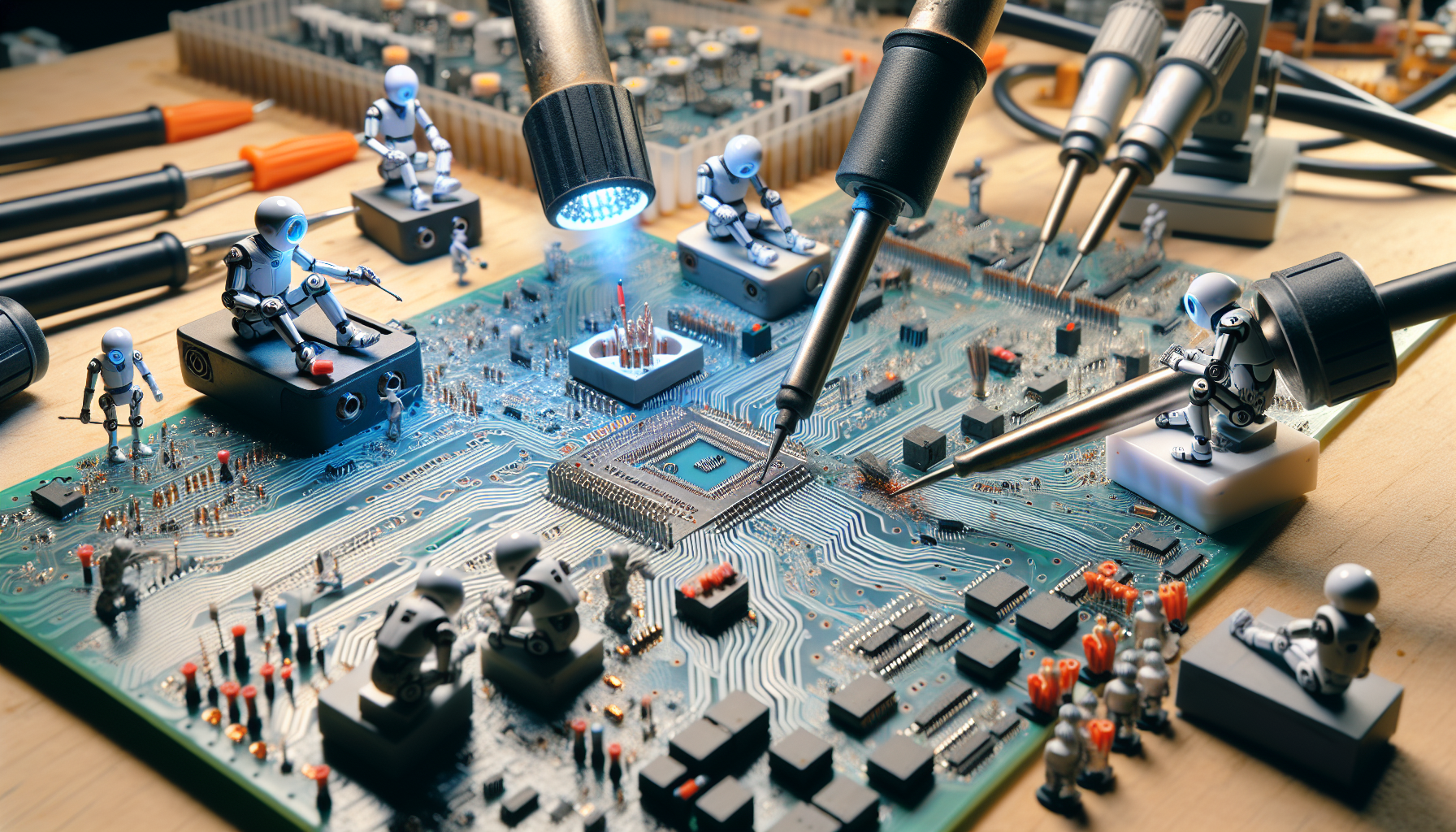
Analogous to a meticulously planned city of electronic components, component placement in PCB assembly is of paramount importance, much like city planning. The recommended best practices for component placement include:
- Grouping components by function
- Using a standard orientation for the components
- Separating different areas from each other
- Considering PCB fabrication considerations to improve signal quality and performance.
So, how do we decide on the placement of components in a PCB design? This is achieved by carefully managing multiple compromises to achieve the best overall PCB layout. This involves:
- Keeping space between components and the PCB edge
- Taking into account the shape, size, and restrictions of each component
- Placing through-hole components on the top side of the PCB to reduce assembly steps and optimize the PCB assembly process.
Soldering Techniques
As previously discussed, soldering acts as the adhesive that binds the components of a PCB together. Various soldering techniques commonly utilized in PCB assembly encompass:
- Wave soldering
- Reflow soldering
- Hand soldering
- Soft soldering
- Hard soldering (silver soldering)
- Braze soldering
Each of these techniques has its own advantages and is used based on the specific requirements of the PCB.
Traditional and modern soldering techniques serve different purposes in PCB assembly. Traditional techniques, like through-hole assembly (THA), require inserting component leads through holes and soldering on the opposite side of the PCB. On the other hand, modern techniques, such as surface mount technology (SMT), entail mounting components directly onto the PCB surface using solder paste and reflow soldering. The choice of soldering technique depends on factors such as existing capabilities, materials, requirements, temperature, humidity, material, manufacturability design of the PCB pad, mold design, solder beads, mark points, printing direction, and equipment accuracy. The application of a solder mask can also influence the selection of soldering techniques.
Inspection and Testing
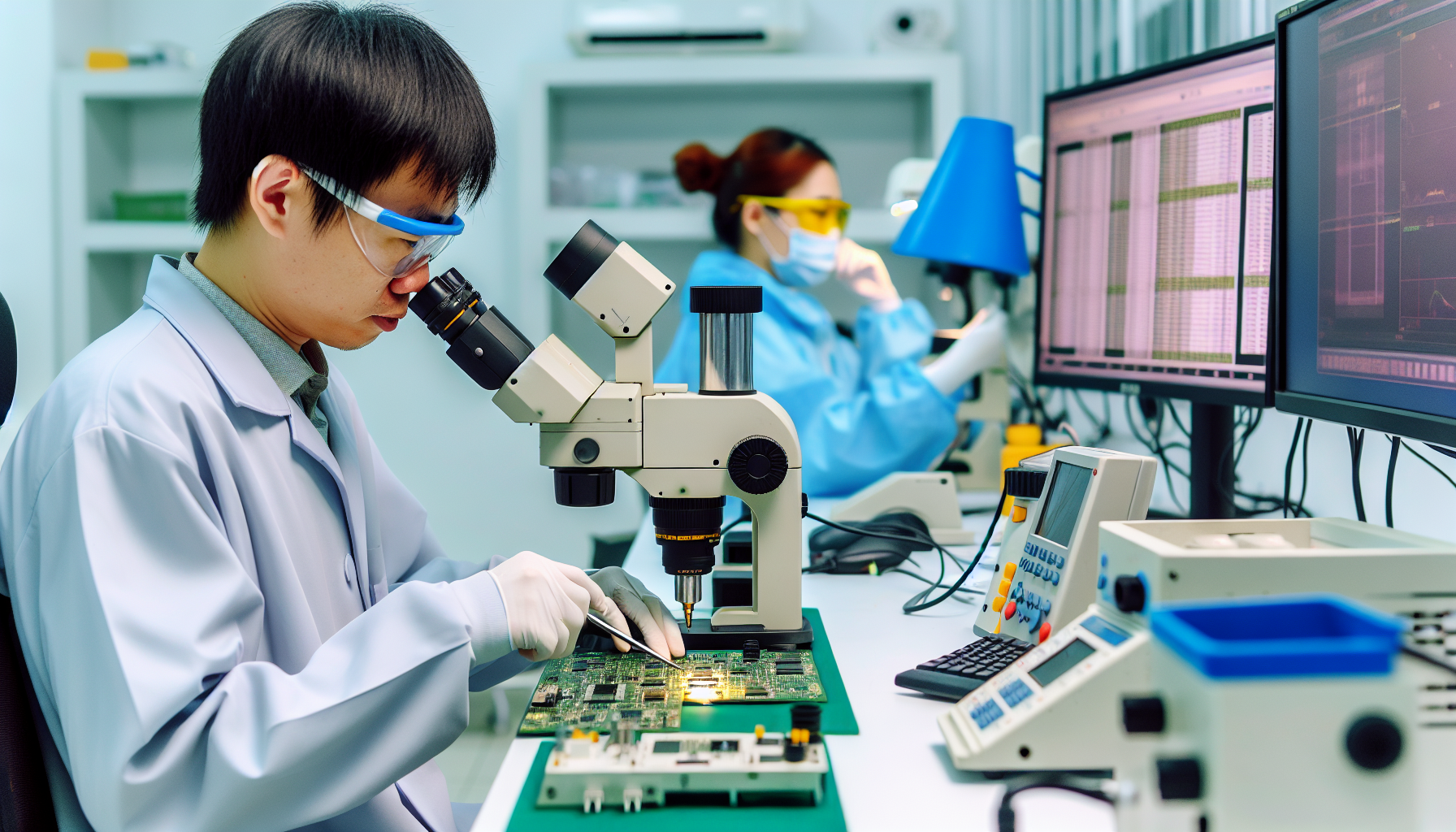
Quality control holds the utmost importance in PCB assembly, necessitating the role of inspection and testing. The inspection methods employed in PCB assembly encompass:
- Manual visual inspections
- Automated optical inspections
- Automatic laser tests
- X-ray inspections
Each of these methods has its own advantages and is used based on the specific requirements of the PCB and the components used.
Testing constitutes another essential part of PCB assembly. Prevalent testing methods utilized in PCB assembly encompass:
- In-circuit testing
- Flying probe testing
- Automated optical inspection (AOI)
- Burn-in testing
- X-ray inspection
Additionally, functional testing is conducted at the conclusion of the manufacturing process to verify the proper operation of the PCB assembly. In short, inspection and testing ensure that the PCB assembly meets the necessary quality standards and is ready to perform its intended function.
Design for Assembly (DFA) Principles
Moving away from the essential elements of PCB assembly, let’s now delve into the principles of Design for Assembly (DFA). DFA is a methodical approach taken during the design stage of a PCB that takes into account the assembly process with supplementary components. This approach enables PCB designers to consider factors such as part-to-part spacing, component selection during the design phase, and the reduction of part count while promoting modularity, all of which play a crucial role in enhancing the manufacturability of the PCB.
Neglecting board assembly can result in substantial complications, such as improper component placement, potentially leading to product malfunction or performance challenges. Hence, considering assembly during the PCB design process is of prime importance. This is where DFA principles come into play. By following these principles, designers can ensure a smoother manufacturing process, improved equipment compatibility, and reduced errors, ultimately leading to cost-effective manufacturing.
Yet, the application of DFA principles extends beyond merely reducing part count and enhancing modularity. It also involves reducing complexity, standardizing components, and balancing cost and performance. By doing so, we can optimize the PCB design for better manufacturability, improved functionality, and reduced production costs.
Reducing Complexity
Diminishing complexity in PCB design assembly parallels simplifying a tangled equation - it renders everything more manageable and understandable. Simpler PCB designs can result in decreased errors during assembly, leading to reduced rework and higher yield rates. This directly contributes to improved manufacturability and cost-effectiveness.
Minimizing the complexity of PCB designs can expedite the production process by enhancing the comprehensibility and ease of assembly of the boards, ultimately leading to quicker turnaround times. Furthermore, a streamlined PCB design generally enhances the robustness of products by reducing the likelihood of manufacturing defects, thereby enhancing the reliability and longevity of the final product. Therefore, strategies such as utilizing fewer components, minimizing routing congestion, and selecting components with simpler assembly methods can be employed to optimize the manufacturing process.
Standardizing Components
In PCB assembly, consistency is paramount. This is when the standardization of components becomes crucial. Standardizing components in PCB design assembly is crucial for enhancing signal quality and performance, minimizing design development time and cost, and guaranteeing the compatibility and availability of components.
The use of standardized components offers numerous advantages, such as readily availability, affordability, known reliability, higher power and density designs, high performance and user safety, effective component placement, and reduced design development time and cost. Furthermore, standardizing components reduces the frequency of reel changes for fabricators, facilitates footprint verification, and enhances manufacturing scheduling by preventing sourcing delays. Thus, standardizing components plays a crucial role in supply chain management, ensuring that designs are furnished with essential components and facilitating reduced lead times on product orders.
Balancing Cost and Performance
In PCB design assembly, cost and performance mirror two sides of the same coin. The cost of PCB assembly can be influenced by factors such as:
- The type of material
- The size of the board
- The number of layers
- The density of components on the PCB board
Typically, more layers and higher component density lead to increased costs.
On the other hand, the performance of a PCB assembly, as indicated by factors such as material selection, design complexity, and overall product performance expectations, can also have an impact on its cost. Elevated performance standards typically result in higher costs due to the requirement for advanced materials and intricate designs. Therefore, striking the right balance between cost and performance is a delicate dance that requires careful consideration of various factors and trade-offs.
Tips for Enhancing PCB Design Assembly
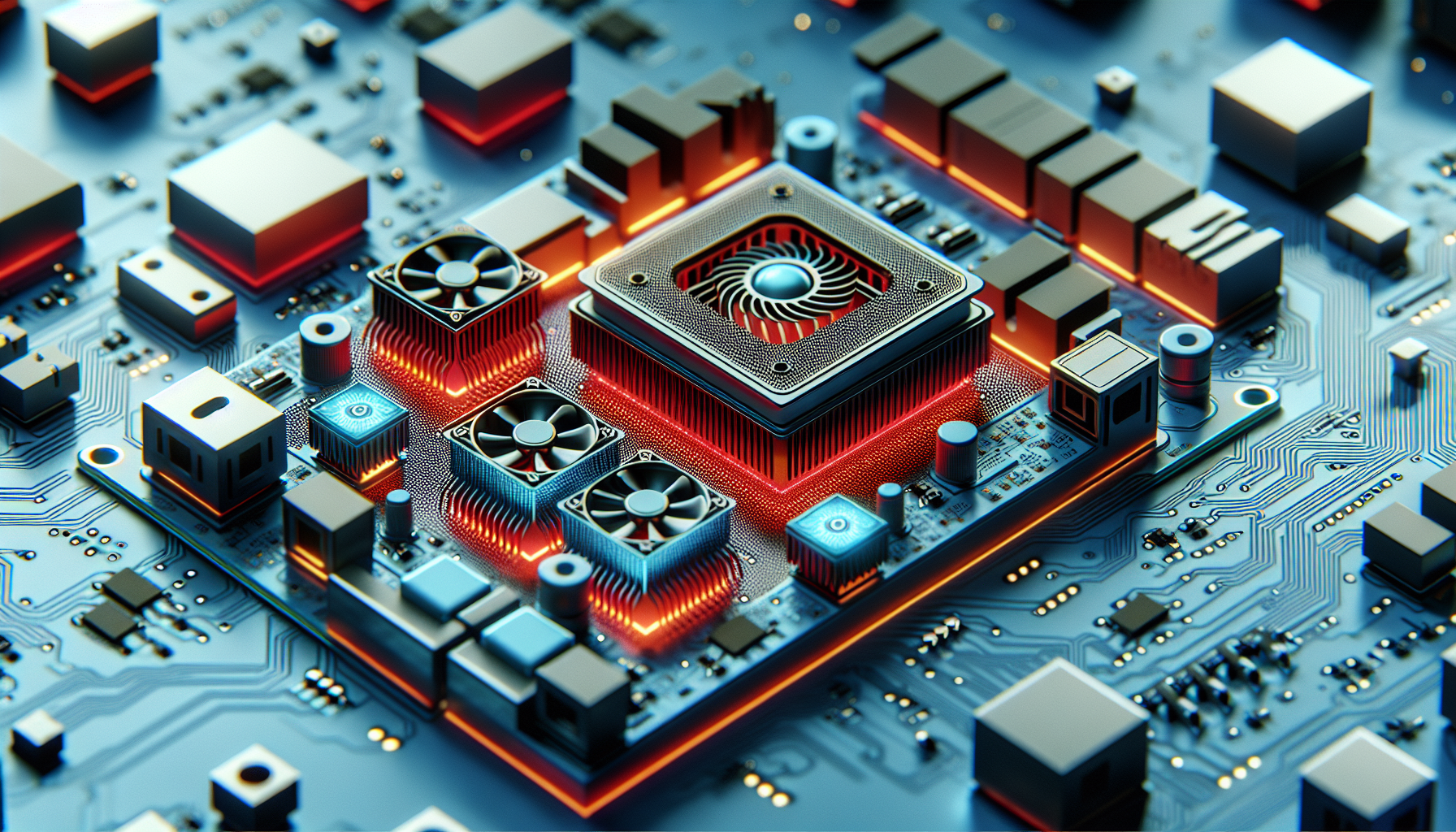
Although the principles of DFA lay a robust foundation for PCB design assembly, further strategies can be implemented to augment the process. These include thermal management, material selection, and designing for testability.
Effective thermal management in PCB design assembly involves the implementation of various techniques and components to mitigate heating issues and enhance thermal efficiency. This can be achieved by utilizing thermal vias, incorporating materials with superior thermal properties, and implementing heat dissipation strategies.
The selection of materials for PCB design assembly is another crucial consideration as it directly influences the electrical performance of signal traces, as well as the overall performance, reliability, and cost of the final product. Therefore, paying close attention to material selection during the design phase is imperative.
Thermal Management
In PCB design assembly, heat can be both a friend and an adversary. On one hand, it’s essential for the soldering process, but on the other hand, excessive heat can lead to component failure and reduced device performance. Therefore, effective thermal management is crucial for maintaining the ideal operating conditions for your electronic device.
The implementation of effective thermal management strategies in PCB design assembly is crucial for regulating the temperature of electronic components, reducing heating concerns, and enhancing thermal performance. This can be achieved by:
- Adopting a combination of active and passive cooling techniques
- Incorporating materials with superior thermal properties
- Implementing heat dissipation strategies
In essence, effective thermal management ensures that your electronic device can operate at its best, even under the most demanding conditions.
Material Selection
Material selection, a vital aspect of PCB design assembly, can dramatically impact the final product’s performance and reliability. The selection of PCB materials plays a crucial role in determining the overall performance, longevity, and reliability of electronic devices. Inadequate material selection can result in diminished lifespan and performance, while high-quality materials can contribute to improved performance and extended lifespan.
Selecting the right materials for your PCB can also have a significant impact on thermal management. The PCB material influences the resistance in copper traces and vias, leading to potential increase in heat production and reduction in power. Furthermore, the thickness and width of copper pads play a crucial role in PCB thermal design effectiveness.
Additionally, the thermal conductivity of the PCB substrate material is a key factor in heat dissipation. In cases where PCBs generate excess heat, additional cooling techniques such as:
- heat sinks
- heat pipes
- fans
- thick copper
may be necessary.
Designing for Testability
Incorporating testability into PCB design assembly is a crucial step that can substantially boost the manufacturing process’s efficiency. Incorporating testability in PCB assembly design enhances fault detection by utilizing methods that more effectively identify faults such as:
- short circuits
- open circuits
- incorrect placement
- faulty components
This allows for early problem identification prior to full-scale production.
Incorporating design for testability in PCB assembly helps in identifying issues early in the manufacturing process, which in turn reduces the need for rework or testing of fully assembled boards. This leads to improved yields and overall product quality, ultimately contributing to reduced production costs. Therefore, techniques such as adopting a Design for Testing (DFT) approach, considering test point requirements throughout the design process, and using testability methods to isolate potential problems can greatly enhance the efficiency and cost-effectiveness of the PCB assembly process.
Common Challenges and Solutions in PCB Design Assembly
Although the process of PCB design assembly can be intricate and rewarding, it comes with its own set of challenges. Common challenges faced in PCB design assembly include component availability, handling mixed assembly technologies, and ensuring proper board edge clearance.
To avoid significant delays in PCB assembly, it’s crucial to verify component availability before starting the PCB design. Component shortages can lead to manufacturing delays and prolong the design process for new products, making it more intricate and time-consuming. Therefore, effective supply chain management is key in guaranteeing component availability for PCB assembly.
In PCB design, mixed assembly technologies refer to the integration of surface mount technology (SMT) and through-hole technology (THT) on a single PCB. This presents its own set of challenges, but by employing strategies such as utilizing modular design and designing for automation, these challenges can be effectively managed.
Component Availability
One of the main challenges in PCB design assembly is ensuring component availability. Delayed or unavailable components can significantly derail the PCB assembly process, leading to increased production times and costs. Therefore, verifying component availability before starting PCB design is crucial to prevent substantial delays in PCB assembly.
To effectively manage component availability, several strategies can be employed. These include:
- Paying close attention to component spacing
- Selecting components during the design phase
- Segregating lead and lead-free components during assembly
- Utilizing alternative components
- Diversifying the supply chain
- Cultivating strong relationships with suppliers
- Regularly monitoring component availability
- Planning for component obsolescence
By employing these strategies, PCB designers can ensure a smooth and efficient assembly process, minimizing delays and maximizing productivity.
Handling Mixed Assembly Technologies
The integration of surface mount technology (SMT) and through-hole technology (THT) in a single PCB is a common practice in PCB design assembly. However, handling mixed assembly technologies presents its own set of challenges. These include the need for different assembly processes for SMT components and THT components, as well as the need for different equipment and procedures for each technology type.
However, these challenges can be effectively managed by employing certain strategies. These include:
- Ensuring clear and unobstructed signal return paths for all signals
- Maintaining a lower impedance ground
- Keeping the design simple for double-sided mixed boards
- Paying attention to component spacing
- Selecting components during the design phase
- Segregating lead and lead-free components
- Communicating with the PCB assembler early on
- Proper planning and design to accommodate the varying requirements of each component
By adopting these strategies, PCB designers can effectively manage mixed assembly technologies, ensuring a smooth and efficient assembly process.
Ensuring Proper Board Edge Clearance
Another crucial aspect of PCB design assembly is ensuring proper board edge clearance. Board edge clearance in PCB design assembly refers to the minimum distance between any components and the PCB’s edge. It is important to maintain this clearance to prevent any impact on the board’s functionality and reliability. Typically, parts should be set back around 0.125 inches from the edge, while taller parts may require up to 0.250 inches.
Following the recommended guidelines for board edge clearance can help prevent issues during manufacturing and operation. These guidelines encompass clearances for holes, V-groove scores, and component-to-edge distances. Adhering to these guidelines is crucial for preventing issues during manufacturing and operation. Therefore, strategies like maintaining a minimum distance of 0.020 inches between the edge of the hole and the edge of the board, a distance of 0.05 inches between the components and the center of the V-groove score, and a general guideline for component clearance around the edge of a printed circuit board of 0.100 inches, can ensure proper board edge clearance.
Summary
In conclusion, PCB design assembly is an intricate process that involves careful consideration of various factors, from component selection to thermal management, and from material selection to testability. By understanding the principles of Design for Assembly (DFA), implementing effective strategies for component placement, soldering, and inspection, and by addressing common challenges like component availability and mixed assembly technologies, we can optimize the PCB design assembly process to produce high-quality, reliable, and cost-effective electronic devices. Now, with these insights at your disposal, you’re well-equipped to navigate the intricate maze of PCB design assembly!
Frequently Asked Questions
What is a PCB assembly?
A PCB assembly, or printed circuit board assembly (PCBA), refers to the finished board with all components soldered and installed on a printed circuit board (PCB), which uses conductive pathways within a non-conductive substrate.
What is PCB design and manufacturing?
PCB design and manufacturing is the process of creating a fully functional printed circuit board assembly from a product concept, involving schematic capture, layout design, board fabrication, and PCB assembly. This complex two-step process optimizes electrical characteristics within design constraints to bring the product concept to life.
What are PCB assembly drawings?
PCB assembly drawings are diagrams that show the arrangement of components on a circuit board, including reference designators for identification. This helps in understanding the layout and placement of parts during the assembly process.
How much does it cost to get a PCB assembled?
The average cost of PCB assembly ranges from $0.02 to $0.05 per square inch, depending on design complexity and labor involved. Keep in mind that this price can vary based on factors like labor rates and overhead expenses.
What is the significance of PCB assembly in electronic devices?
PCB assembly is significant in electronic devices because it connects and supports various electronic components, ultimately enabling the device’s functionality.