Smart manufacturing is considered the fourth industrial revolution, also known as Industry 4.0, this fact marks a meeting point between physical production and digital technologies. This is through automation, IoT, data analytics, artificial intelligence, and machine learning among others. With the transformation of industries towards smart, efficient and intelligent systems, integrated circuits (ICs) are looking at a great future for the next generation of manufacturing. This blog will explain why ICs are essential in the world of smart manufacturing and how they perform everything from connectivity to process optimization.
The Role of Integrated Circuits in Smart Manufacturing
Integrated circuits or ICs are small and intricate systems composed of many components such as transistors, diodes and resistors that are located on a single silicon bridge. It is the computerized control circuit of the electronic devices it’s involved in functions like computing, communication and control. Many technologies necessary for smart manufacturing are supported by ICs and these include sensors, actuators, controllers and communication modules.
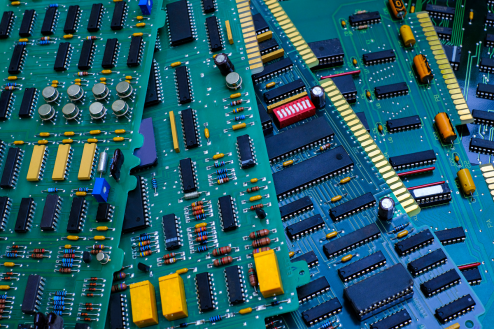
Enabling Real-Time Data Collection and Processing
Smart manufacturing is noted for the application of strategies that involve information control to enhance productivity. Measurement devices are installed within a machine or a system for acquiring information that is essential to the course of its operation like temperature, vibration, pressure, and others. These sensors are powered by ICs making it possible to take data constantly in real time. These ICs are required for compiling raw data collected from various points in the production line into useful information that can be used to monitor the health of equipment for their condition prediction and to fine-tune operations.
As the data is the new Industry 4.0, ICs offer the computational power that is normally needed to analyze large amounts of data in a way and within the time frame required. Advanced ICs like microcontrollers & DSPs allow continuous processing and if it’s big data from smart manufacturing systems, confirm that it is processed near the edge rather than the Central Data Centre. This reduces the response time and also guarantees that crucial changes are made within the shortest time possible hence enhancing the flow of operations.
Supporting the Internet of Things (IoT) in Manufacturing
Manufacturing is one of the major applications of IoT which is referred to as smart manufacturing. IoT products in a manufacturing context gather information, inter-operate and can be monitored and operated centrally. ICs are said to be essential for IoT devices in the provision of connectivity, processing functionality and energy management functionality. ICs are essential for the IoT ecosystem as it is hard to imagine how a huge number of interrelated devices could be managed and operated if it were not for these components.
ICs help to connect sensors, actuators or other devices to the overall IoT chain, thus allowing machines to interact on their own. Thus, through ICs, IoT devices can send collected data to cloud-based centralized servers or more distributed edge computing nodes enabled for real-time analytics and decision-making. These integrated circuits also help to consume less power as is important in applications where the devices are expected to run for long periods while requiring minimal maintenance.
Facilitating Machine-to-Machine (M2M) Communication
Smart manufacturing implements extensive use of machine-to-machine (M2M) communication where machines in a manufacturing facility communicate with other machines to facilitate various manufacturing functions. ICs play a significant role in M2M communication by providing the means of wireless transmission, networking and signal processing within machines. These chips allow the various equipment components to work together and run the manufacturing process with minimal supervision.
For instance, the moment one machine finishes its work it can alert the successive machine to commence its work. Without the ICs of the machinery to do the processing and commanding of stakes, such a level of automation and simplified communication will not be possible.
Boosting Artificial Intelligence and Machine Learning Applications
AI and ML are highly important in smart manufacturing since these two technologies enable industrial machines to learn data and act depending on it in a way that does not require added human interaction. In the case of equipment control, systems powered by artificial intelligence can process data on the equipment and determine potential failure with the help of intricate formulas that will reduce the time and costs to a minimum.
Hardware accelerators, in particular, GPUs, FPGAs, and ASICs, used in line with specialized ICs offer the computation capacity required in AI and ML for manufacturing. These ICs help in the training and implementation of AI models for applications in predictive maintenance, defect identification and other applications that are useful in manufacturing.
The incorporation of ICs also enables choosing optimal AI/ML algorithms for direct integration into the hardware, which leads to increased speed and better accuracy. Advanced ICs which are well suited for AI, can analyze large data structures from machines and sensors in real-time, and make intelligent decisions for enhancing the flow of production.
Improving Energy Efficiency in Manufacturing Processes
In the age of sustainability, it is a significant issue for manufacturers to make a product more energy efficient. ICs have a major impact on the efficient use of power in production systems in smart factories. Using ICs designed for power management, the consumption of energy in machines can be regulated depending on the information received and the systems can be turned off or their power levels can be decreased during certain periods.
Energy-efficient ICs also make it possible to design low-power IoT devices that are very crucial in a smart factory when it comes to energy consumption. For example, have their application as power-sensitive components like sensors and communication modules which can function on low power thus enhancing the battery life of wireless devices and minimal maintenance.
Enhancing Flexibility and Customization in Production
The idea of smart manufacturing can be defined as the approach that provides increased flexibility in terms of quickly responding to increased or decreased demand, alterations in product design, and other changes in the manufacturing process. With the use of ICs, manufacturers can design complex production lines that can be easily reconfigured for different products or production requirements.
To support such dynamic changes microcontrollers and programmable Integrated circuits are available to give the flexibility required in manufacture. The ICs present in these machines can be firmware updated or reprogrammed which implies that the machines’ operational parameters can be modified without any intervention. This flexibility is very important in fields such as automotive, aerospace and electronics industries.
Ensuring Safety and Reliability in Manufacturing
It plays an important role in highly automated industries to eliminate risks that may cause harm to the machines and systems. ICs are incorporated in safety-critical systems where they are employed to prevent failure or an accident. Some examples of the use of microcontrollers in smart sensors and controllers include ICs that can identify changes in temperature or vibrations and alert the system that an error has occurred then shut down the equipment to avoid further damages or even accidents.
Furthermore, the application of ICs helps to increase the reliability of machines through a predictive maintenance model. The application of ICs enables the monitoring of the condition of machinery and equipment so that a failure is detected before it occurs as well as initiation of preventive measures to avert the breakdown. This enables the reduction of time that the machines are not in use and enhances the reliability of the manufacturing process.
Enhancing Automation with Robotics and Autonomous Systems
Robots and other forms of automation are critical to smart manufacturing, due to the ability of these systems to work faster, more accurately and consistently than their human counterparts. They are the nucleus of robotic systems since they contain the computational capabilities required in motor control, integrating sensors and real-time decision-making processes.
For instance, ICs that are applied in motion controllers make it possible for the robots to move with high precision while the ICs applied in vision systems help the robots to capture the events in their vicinity. This makes it possible to design highly autonomous systems that may either cooperate with humans or work on their own enhancing production efficiency and minimizing human factors in production processes.
With the increased technological integration of Robotics Systems, there will always be a need for unique ICs that would be capable of handling complicated analyses for the enhancement of autonomy. These ICs will be critical for the development of robotics and enabling the creation of smart manufacturing environments.
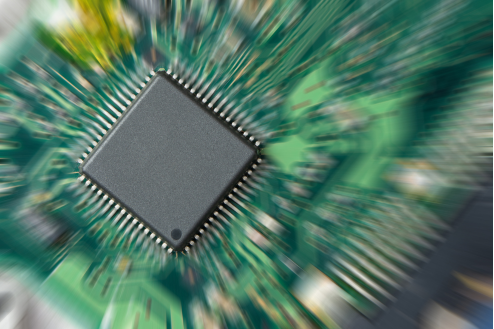
Supporting Advanced Supply Chain Management and Traceability
The next generation of smart manufacturing combines supply chain practices and better track abilities to push the next level of digitization and intelligence outside of the manufacturing setting. Application-specific integrated circuits are used to track products at every stage of the supply chain to help manufacturers track everything starting from the procurement of raw materials up to the delivery of the final product.
RFID tags and smart labels through Integrated Circuits provide identification means that can track goods in real-time while they are in the supply chain. The ICs make tracking of products more efficient, better stock control, reduction in wastage and increased accountability. Also, the ICs incorporated in packaging can secure products against imitation, which is key in firms including medical products and fashion accessories manufacturers.
Paving the Way for 5G and Beyond
Smart manufacturing is expected to adopt the next generation of wireless communication, 5G which will offer very fast, reliable and low-latency communication. ICs play an essential role in realizing 5G communication in manufacturing settings. Application-specific ICs for 5G enable machines, sensors and other devices to communicate at very high speed which is indispensable for real-time analysis and operation control.
Furthermore, due to the lower latency of 5G networks, manufacturing systems can be more flexible and dynamic, thereby opening the door to more complex applications like control of remotely operated robots, utilization of augmented reality tools for machines’ maintenance and even AI decision making in real-time. With the increasing deployment of 5G networks, these 5 G-induced ICs will be central in the advancement of further smart manufacturing technologies.
Conclusion
Integrated circuits are the backbone of smart manufacturing that plays a critical role in the manufacturing process today that is often unnoticed. From data conversion and management in terms of machine interface communication, and artificial intelligence in decision-making to energy management in smart manufacturing systems, ICs are indispensable components in next-generation manufacturing systems. As Industry 4.0, bringing ICs into the picture will keep them at the top by enabling higher levels of automation and conservative growth in manufacturing. The role of these technologies cannot be overestimated without the ICs, one cannot rationally think how smart, connected, and autonomous factories of the future would work.