Choosing between IGBT and silicon carbide (SiC) technology can be pivotal for your power electronics performance. With SiC on the rise for its efficiency and thermal advantages, this article examines IGBT silicon carbide distinctions, highlighting why and where SiC might outperform traditional IGBT solutions.
Key Takeaways
- IGBTs are suitable for high-voltage, high-current applications due to their combined properties of MOSFETs and bipolar junction transistors, whereas SiC MOSFETs offer superior performance in high power applications with their high thermal conductivity and efficiency.
- The power electronics industry is witnessing a shift from IGBTs to SiC MOSFETs, driven by advancements in manufacturing, efficiency, and the ability of SiC devices to operate at higher temperatures and reduce switching losses.
- Choosing between IGBT and SiC MOSFET technologies involves consideration of voltage/current requirements, switching frequency, thermal management, and system cost-effectiveness, with SiC MOSFETs increasingly favored for their efficiency and high-speed switching capabilities.
Understanding IGBTs and Silicon Carbide in Power Electronics
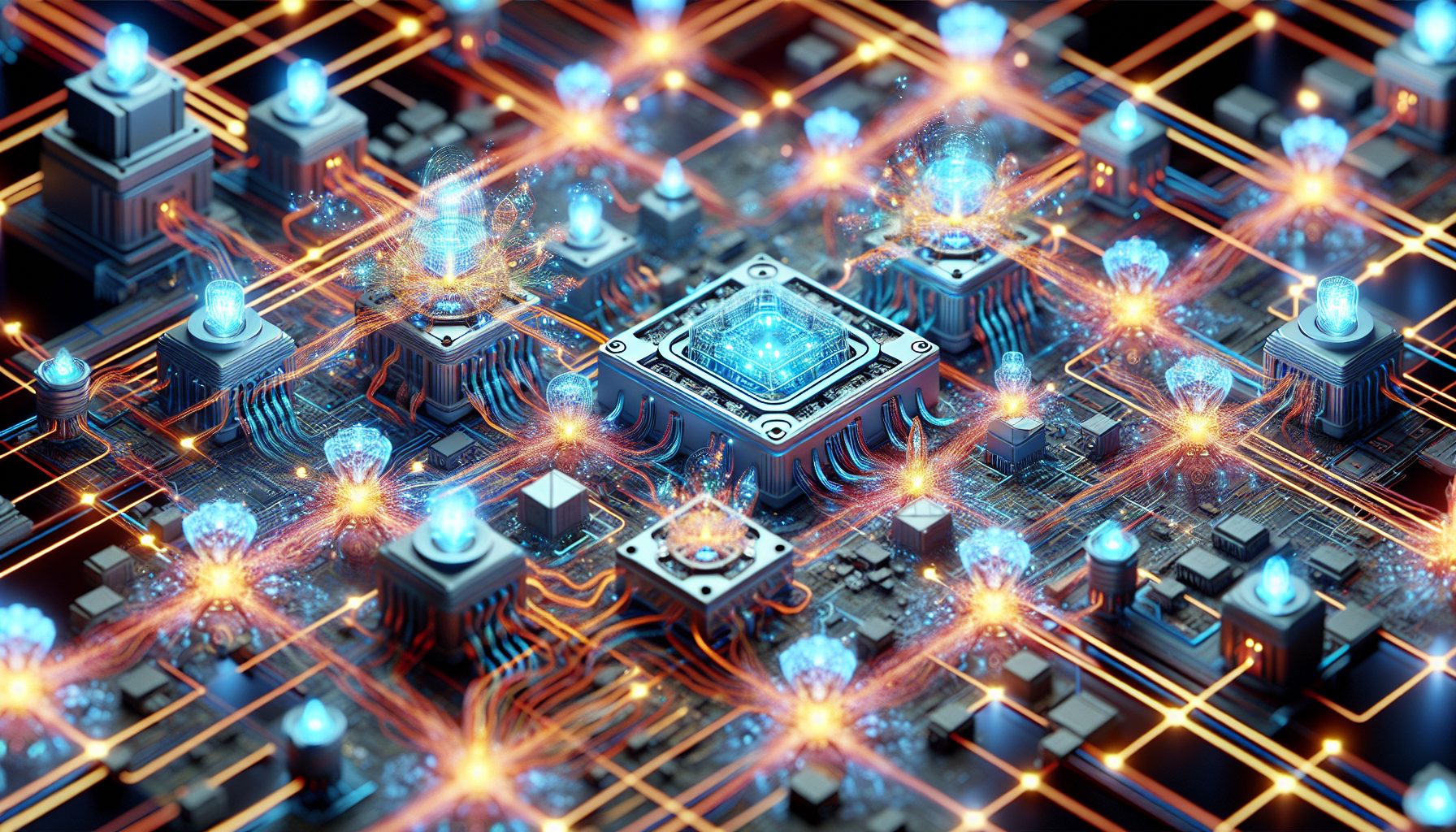
Modern power electronics circuits heavily rely on power semiconductor devices like IGBTs and SiC MOSFETs. They are the workhorses that make it possible to convert and control electrical energy efficiently and reliably. So, what are these devices, and why are they so important in the realm of power electronics?
Insulated Gate Bipolar Transistors, or IGBTs, combine the high input impedance of MOSFETs with the efficient conduction of Bipolar Junction Transistors, making them ideal for high-voltage, high-current applications. The operational characteristics of IGBTs are determined by the voltages between the collector, emitter, and gate terminals, facilitating modes of forward blocking and conduction. IGBTs are fundamentally voltage-controlled devices, evident from their output characteristics that depict the relationship between the collector current and the collector-emitter voltage.
On the other hand, we have silicon carbide MOSFET power devices. These silicon carbide (SiC) MOSFETs are gaining ground in power electronics due to their exceptional physical and electrical properties. Indeed, SiC MOSFETs contribute significantly to the field’s evolution, heralding a new era of high-speed switching and high power density.
The Role of IGBTs in Power Conversion
IGBTs play an integral role in many high-voltage applications where power conversion is a crucial process. Their ability to handle large power transfers and their fast switching capabilities make them well-suited for high-voltage power conversion systems. But what exactly makes them so efficient in these applications?
The efficiency of IGBTs in power supplies, particularly for high-voltage and high-current applications, is enhanced by their low on-state voltage drop and swift switching. These characteristics allow them to handle the rapid transitions between voltages and currents that occur in power conversion processes, reducing power losses and improving overall system efficiency.
Moreover, in renewable energy systems, IGBTs are instrumental in:
- Converting variable DC power into usable AC power
- Optimizing the energy conversion process
- Maintaining effective power point tracking
- Controlling the switching of power devices
- Manipulating the output voltage of a power supply
- Determining the speed and direction of a motor
Advantages of Silicon Carbide in High Power Applications
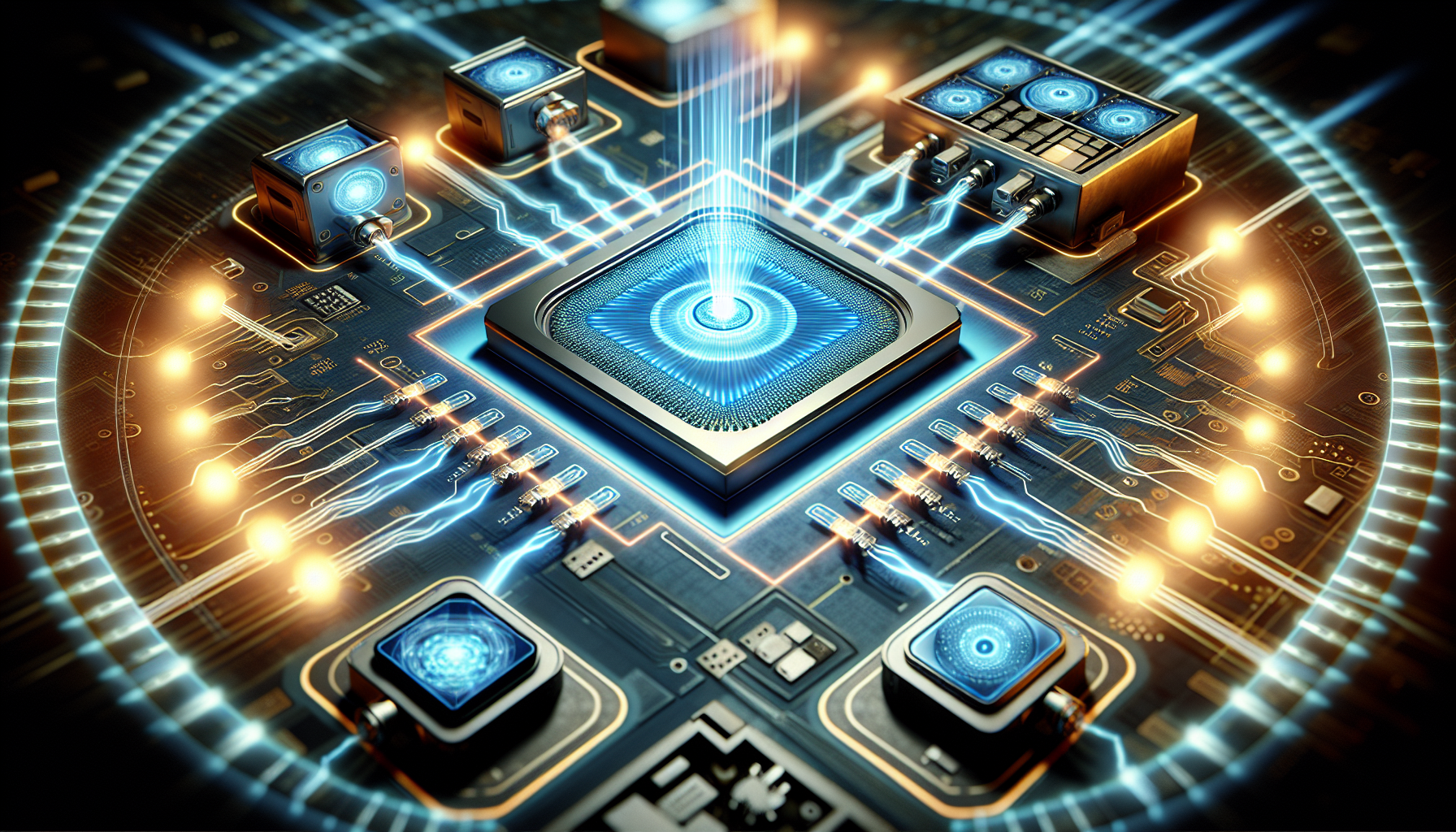
Despite the advantages of IGBTs, Silicon Carbide (SiC) MOSFETs are gaining recognition in high power applications. These devices leverage the unique properties of silicon carbide, a wide bandgap material known for its high thermal conductivity and high withstand voltage, to deliver superior performance in high power applications.
One of the key areas where SiC MOSFETs shine is in the automotive industry, specifically in the development of electric vehicles. Here, SiC MOSFETs are utilized for their fast switching capabilities, allowing for more compact inverters that can handle higher voltages. This not only improves the efficiency of electric vehicles but also extends their range, making electric vehicles more competitive with their fossil fuel counterparts.
In addition to their superior switching performance, SiC MOSFETs also boast the following advantages:
- Higher thermal conductivity, enabling them to operate at higher temperatures
- Robust thermal management, making them suitable for high power applications
- Reliable operation even under high power loads
These advantages make SiC MOSFETs a preferred choice for many power electronics engineers.
Transitioning to SiC: Understanding the Shift in Power Modules
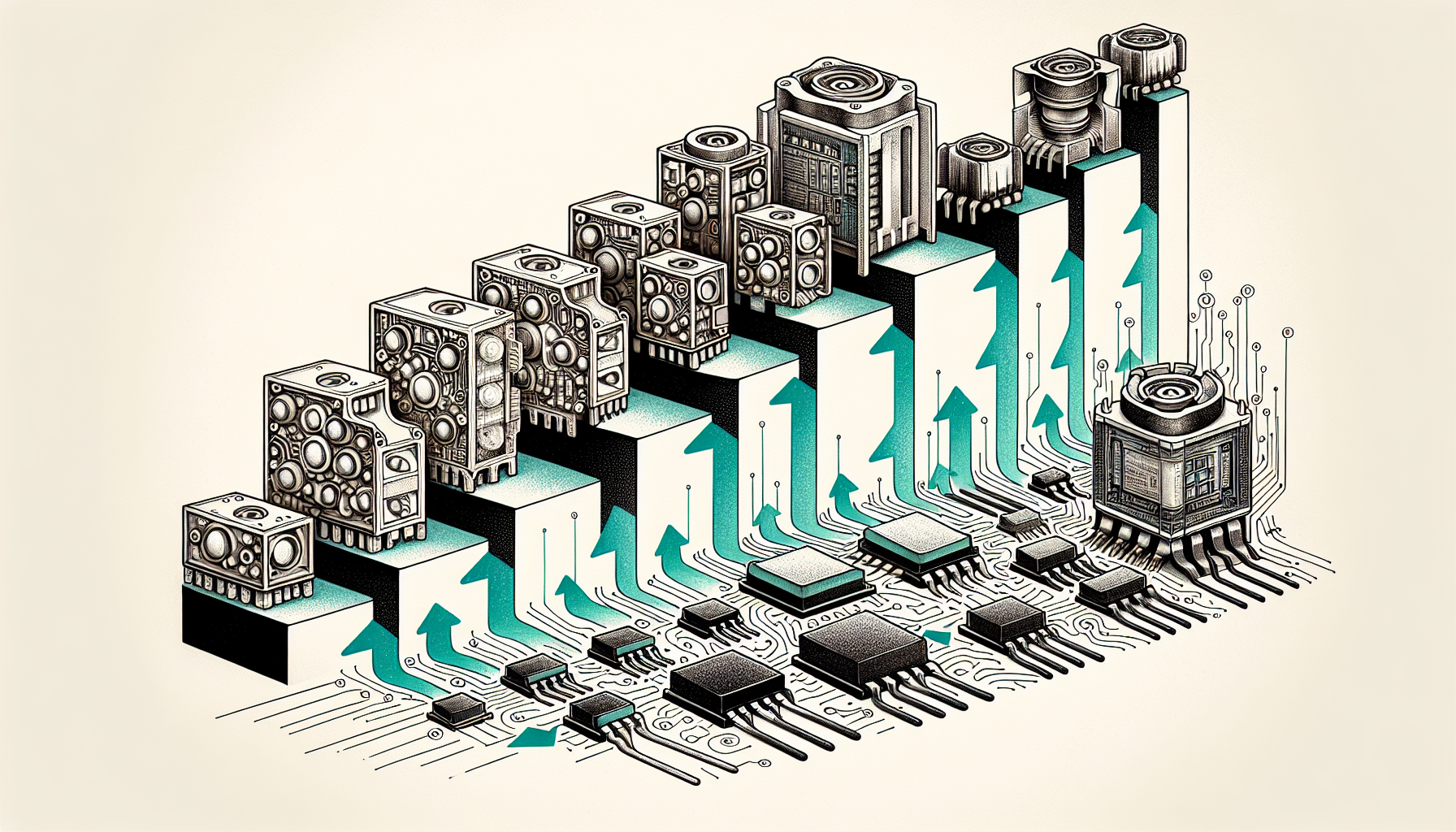
A noticeable shift from traditional Insulated Gate Bipolar Transistors (IGBTs) to Silicon Carbide (SiC) MOSFETs in power modules is taking place in the power electronics industry. This transition is driven by several factors, including advancements in manufacturing, product offerings, and demonstrated efficiency improvements of SiC devices.
One key driver behind this transition is the potential for a substantial reduction in the cost of manufacturing SiC power devices. This is made possible by the introduction of larger 150-mm diameter SiC wafers, which enable more devices to be fabricated per wafer, thereby reducing the cost per device. Additionally, companies like STMicroelectronics are pushing the boundaries of the SiC market with products offering higher temperature tolerances and reduced losses, ushering in a new era of power electronics.
Research has also demonstrated a clear efficiency increase in systems using SiC-IGBTs, substantiating the improvements in power density and efficiency. These advancements in manufacturing, product offerings, and demonstrated efficiency improvements are key drivers behind the industry’s ongoing transition to SiC MOSFETs in power modules. This shift signifies a major leap forward in the power electronics industry, opening up new possibilities for increased efficiency and performance in a wide range of applications.
Why SiC MOSFETs are Gaining Traction
What’s causing SiC MOSFETs to gain traction in the power electronics industry? One of the key reasons is their improved performance and efficiency in electric vehicle inverters. By handling higher voltages and frequencies, SiC MOSFETs can deliver substantial efficiency improvements in these applications.
Compared with Silicon IGBTs, SiC MOSFETs enable a 70% reduction in switching losses, offering a 6% improvement in overall power consumption and enhanced short-circuit withstand time. These improvements are largely due to the superior physical and electrical properties of silicon carbide, which allow SiC MOSFETs to operate at higher voltages and temperatures without performance degradation.
Furthermore, companies like WeEn Semiconductors are spearheading advancements in SiC MOSFET technology, leading to remarkable enhancements in power semiconductor capabilities. As a result, silicon carbide’s higher voltage and temperature capabilities are playing a pivotal role in the global push toward vehicle electrification. By enabling more efficient and reliable power conversion and control, SiC MOSFETs are helping to drive the future of electric vehicles and renewable energy systems.
Comparing Power Losses: IGBT vs. SiC MOSFET
SiC technology excels in reducing switching losses when compared to IGBTs, making it stand out. In fact, SiC MOSFETs can deliver up to a 70% reduction in switching losses when replacing Si IGBTs in power inverters. But how does this translate to real-world performance and efficiency improvements?
Experimental results have shown that SiC technology, including SiC JFETs, offers several advantages over IGBT devices:
- Significantly reduces switching losses compared to IGBT devices
- Improves energy efficiency, enabling power electronics systems to operate more efficiently and reliably
- Demonstrates a higher switching speed and notably lower loss than traditional Si-IGBT
These benefits highlight the advantages of SiC technology in power electronics applications.
Choosing between IGBT and SiC MOSFET technology entails evaluating key aspects such as power density, operational temperatures, and thermal management, where SiC has the advantage. For instance, with the adoption of SiC-based inverters, electric vehicles can achieve significantly extended ranges and reduced charging times in systems up to 800 V. Therefore, despite the higher upfront costs of SiC MOSFETs, the efficiency gains and performance improvements they deliver can make them a cost-effective choice in the long run.
Key Factors Influencing the Selection Between IGBT and SiC MOSFET
Several key factors must be considered when choosing between IGBTs and SiC MOSFETs. These include voltage and current requirements, switching frequency, and operating temperature range. Each of these factors can significantly impact the performance and efficiency of power semiconductor devices, making them important considerations in the selection process.
For instance, SiC-IGBT modules turn on almost six times faster than traditional Si-IGBT modules, highlighting their superior switching speed. This can be a significant advantage in applications where high-speed switching is required, such as in motor drive systems. Experiments on SiIGBT and SiCIGBT modules under RL loads focused on turn-on and turn-off delay times, significant for assessing switching performance.
On the other hand, IGBTs are typically chosen for their high current handling capability and fast switching speed, which are crucial for high power applications. In motor drives, for instance, IGBTs are commonly used for converting DC voltage into variable AC voltage to regulate motor speed, optimizing performance, and efficiency. Therefore, the selection between IGBT and SiC MOSFET as a power semiconductor device depends on several factors, each of which can significantly impact the performance and efficiency of power electronics systems.
Assessing Voltage and Frequency Requirements
Considering voltage and frequency requirements is essential when choosing between IGBTs and SiC MOSFETs. Both devices have unique voltage and frequency handling capabilities, which can significantly impact their performance in high power applications.
IGBTs, for instance, are well-suited for high-power motor drive applications due to their capability to handle high voltages with a relatively low voltage drop. This makes them a preferred choice in applications where high-voltage handling is a critical requirement. On the other hand, SiC MOSFETs are becoming popular in power electronics due to their ability to handle higher voltages and frequencies.
However, it’s important to note that while both IGBTs and SiC MOSFETs offer unique advantages in terms of voltage and frequency handling, the selection between these devices should not be based solely on these factors. Other factors, such as power density, thermal management, and cost, should also be taken into account to ensure the most suitable choice for a particular application.
Thermal Management Considerations
Another significant factor to consider when choosing between IGBTs and SiC MOSFETs is thermal management. In high power applications, effective thermal management is essential to ensure reliable operation and prevent device failure.
SiC MOSFETs offer several advantages over traditional silicon IGBTs in high-power applications like electric vehicles:
- Better heat dissipation
- Higher levels of integration
- Higher thermal conductivity, allowing them to operate at elevated temperatures without thermal runaway
These features make SiC MOSFETs ideal for applications where robust thermal management is required.
However, the higher operating temperatures of SiC MOSFETs also bring forward challenges, such as the need for materials and designs that can handle increased thermal cycling. Thus, while SiC MOSFETs offer clear advantages in terms of thermal management, these benefits must be weighed against the potential challenges and costs associated with their implementation.
Designing with SiC: Gate Driver and Circuit Integration
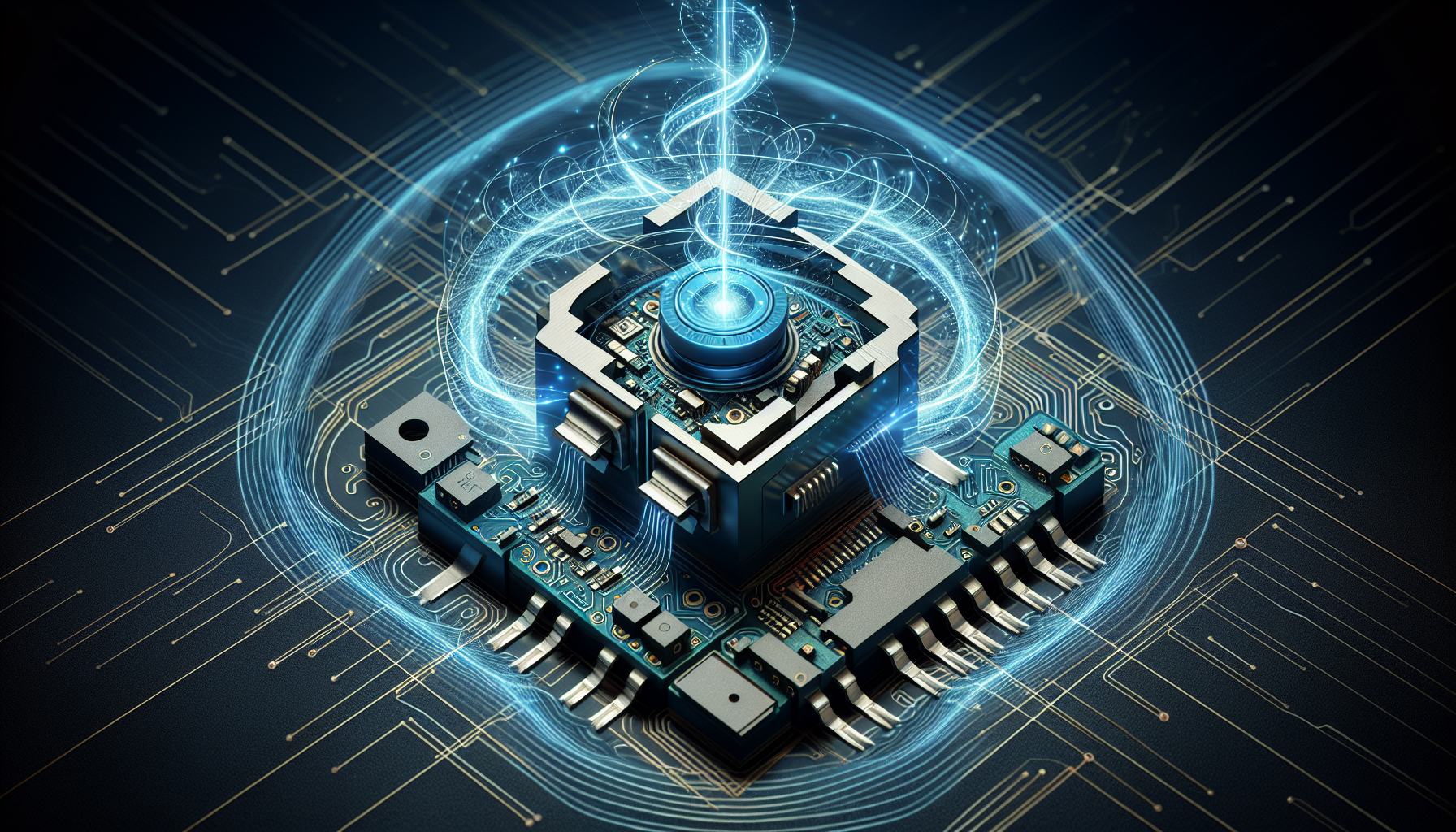
Several critical factors, such as gate driver and circuit integration, are involved when designing circuits with SiC MOSFETs. These factors can significantly impact the performance and robustness of SiC MOSFETs in high-speed switching environments.
Selecting the right gate driver is a key aspect of designing with SiC. The gate driver plays a crucial role as it impacts the performance enhancement achievable with SiC power devices. Different gate driver topologies can be utilized for SiC power devices, including a simple two-level voltage gate driver or a more complex driver for SiC off-JFETs.
Moreover, the gate driver circuit for SiC IGBT switches should prevent Miller current and can incorporate multiple drivers to manage power device control. This illustrates the importance of considering specific circuit elements that can manage the high-speed characteristics of SiC MOSFETs in order to maintain reliability and performance.
Optimizing Gate Drive Signal for SiC MOSFETs
A significant part of designing with SiC MOSFETs is optimizing the gate drive signal. The gate drive signal controls the switching of the SiC MOSFET, and its optimization can significantly impact the performance of the device.
If the gate-to-emitter voltage reaches the threshold voltage of the SiC MOSFET, it can cause the device to turn on unintentionally, potentially resulting in a dangerous short circuit across the DC bus voltage. Therefore, gate-driver design for SiC MOSFETs must account for the following factors:
- Required gate-to-emitter voltage
- Galvanic isolation between low and high voltage circuits
- Inclusion of a Miller clamp to prevent false switching due to parasitic capacitance.
The original gate resistances in SiC MOSFET applications were selected to achieve the fastest possible switching times, emphasizing the importance of gate drive optimization. In addition, PWM signals are utilized to control the gate of SiC MOSFETs, ensuring precise switching operations within the circuit.
Ensuring Robustness in High-Speed Switching Environments
While designing circuits with SiC MOSFETs in high-speed switching environments can pose challenges, it’s vital to maintain reliability and performance. High-speed switching can generate high voltage and current transients, which can potentially damage the device if not properly managed.
SiC MOSFETs are particularly well-suited for applications that necessitate high-frequency switching, offering enhanced precision in motor control. However, these high-speed characteristics also require specific circuit elements that can manage the rapid transitions between voltages and currents.
Designers must ensure that these elements, such as gate drivers and protection circuits, are properly selected and integrated to manage the high-speed characteristics of SiC MOSFETs. By doing so, they can ensure that the SiC MOSFETs can deliver their full performance potential without compromising reliability or longevity.
Case Studies: SiC MOSFETs in Action
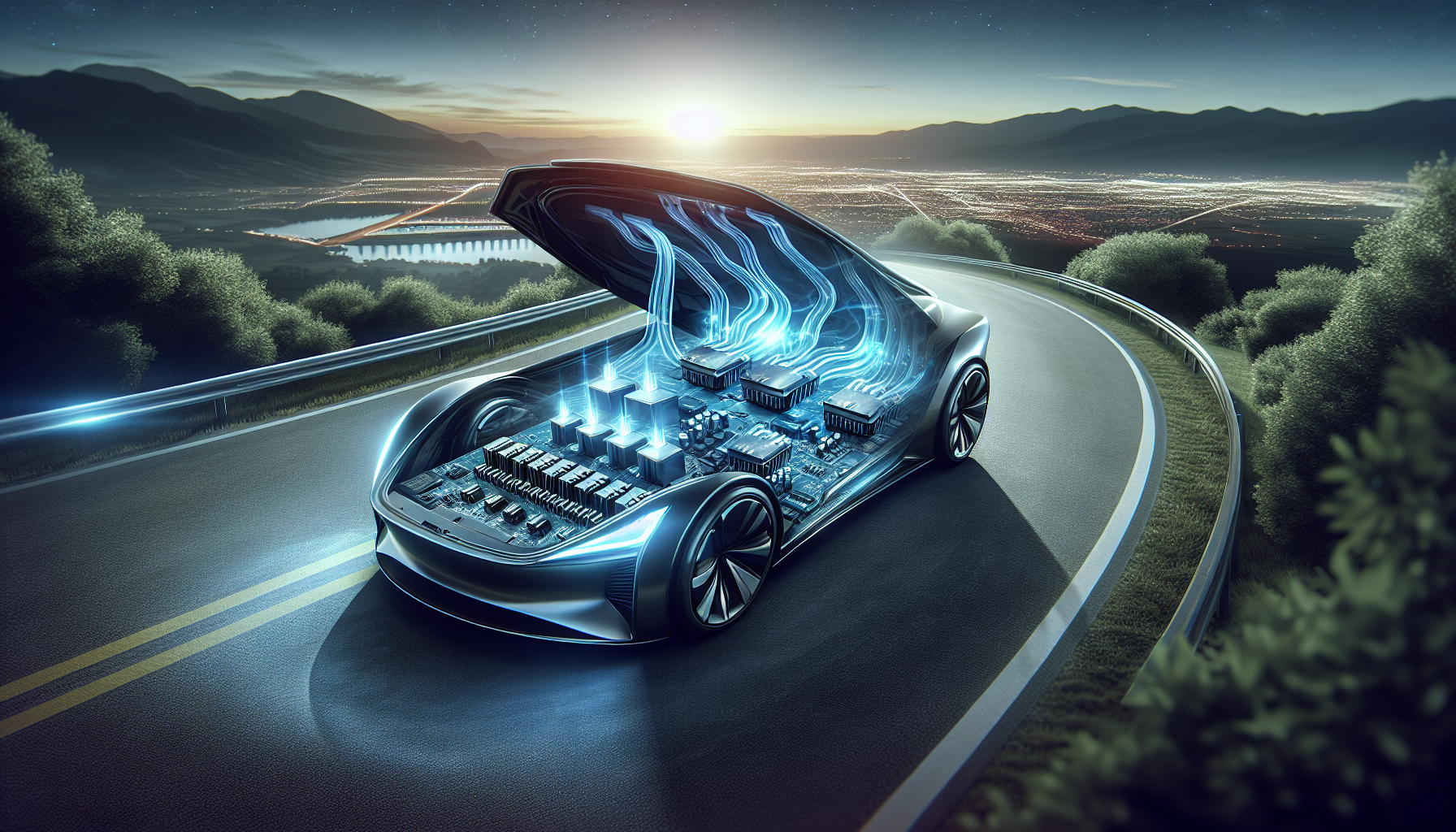
To better understand the benefits and applications of SiC MOSFETs, we’ll examine some case studies. These real-world examples highlight the impact of SiC MOSFETs in various high power applications, showcasing their potential to drive innovation and efficiency improvements.
In recent years, several companies, including onsemi and Rohm Semiconductor, have successfully implemented their SiC modules and SiC MOSFETs in EV traction inverters, marking significant design wins for SiC technology. The research leading to these SiC MOSFET-enabled EV traction inverters involved various generations of SiC technology including SiC-2G, SiC-3G, and SiC-4G power modules.
These developments underscore the potential of SiC technology to revolutionize power electronics, offering substantial efficiency improvements and cost reductions. Let’s delve deeper into these case studies to understand how SiC MOSFETs are driving innovation in electric vehicle traction inverters and renewable energy systems.
SiC MOSFETs Driving Innovation in Electric Vehicle Traction Inverters
The noteworthy role of SiC MOSFETs in spearheading innovation in electric vehicle traction inverters deserves special attention. By handling higher operating voltages and temperatures, SiC MOSFETs can deliver substantial efficiency improvements in these applications.
In addition to improving efficiency, SiC MOSFETs also contribute to enhanced performance in electrified propulsion systems. These devices provide:
- Improved switching efficiency
- Increased junction-temperature capabilities
- Improved short-circuit withstand time
- Lower on-resistance
Furthermore, the transition from 400-V to 800-V battery systems in electric vehicles, supported by SiC MOSFETs, is effective in enhancing driving range and reducing charging times.
Moreover, with the evolution of traction inverters through the integration of SiC MOSFETs and modules, the market for traction inverters is expected to reach $39 billion by 2028. Comparative studies, such as those using WLTC fuel-efficiency test standards, have shown that Rohm’s fourth-generation SiC MOSFETs can reduce power consumption by 6% when compared to IGBTs in the main inverter. This showcases the potential for improved energy efficiency in automotive applications.
Renewable Energy Systems Empowered by SiC Technology
Renewable energy systems are also significantly influenced by SiC technology. Efficiency improvements are critical for the advancement of renewable energy systems such as solar and wind power, and SiC MOSFETs contribute to these improvements by optimizing the performance of solar inverters and wind converters.
The use of SiC technology in renewable energy applications supports the evolution of these systems by:
- Improving efficiencies
- Potentially reducing costs over time
- Enabling higher power density
- Reducing switching waveforms oscillations
These advancements exemplify the revolutionary impact of SiC MOSFETs on the renewable energy sector.
These case studies underscore the transformative potential of SiC MOSFETs in various high power applications. Whether it’s electric vehicle inverters or renewable energy systems, SiC MOSFETs are proving their worth as efficient and reliable power semiconductors that can drive significant performance improvements and cost reductions.
Summary
In this exploration of power semiconductors, we’ve delved into the world of IGBTs and Silicon Carbide (SiC) MOSFETs. We’ve seen how these devices are revolutionizing power electronics with their unique advantages and applications in high-voltage and high-power systems.
IGBTs, with their high input impedance and efficient conduction, are ideal for high-voltage, high-current applications. They play a crucial role in power conversion systems, driving efficiency and performance improvements. On the other hand, SiC MOSFETs, with their superior physical and electrical properties, are gaining ground in high power applications, offering significant reductions in switching losses and improved heat dissipation.
As we transition into an increasingly electrified world, the importance of power semiconductors like IGBTs and SiC MOSFETs will continue to grow. Whether it’s in electric vehicles, renewable energy systems, or power converters, these devices will play a crucial role in managing and controlling electrical energy. By understanding their characteristics, advantages, and applications, we can better harness their potential to drive innovation and efficiency improvements in power electronics.
Frequently Asked Questions
Which is better IGBT or MOSFET?
The IGBT is better than the MOSFET because of its superior efficiency, reduced audible noise, and optimization for both low conduction and low switching loss. The IGBT has far less switching loss compared to the MOSFET.
What is silicon IGBT?
Si IGBT stands for silicon-insulated-gate bipolar transistors, while SiC MOSFET represents silicon carbide metal-oxide-semiconductor field-effect transistors, which are two types of power semiconductor devices. Both are used in various applications to control and regulate power systems.
What are IGBTs and why are they important in power electronics?
IGBTs, or Insulated Gate Bipolar Transistors, are important in power electronics because they combine the high input impedance of MOSFETs with the efficient conduction of Bipolar Junction Transistors, making them ideal for high-voltage, high-current applications. They play a crucial role in power conversion systems, driving efficiency and performance improvements.
How do SiC MOSFETs compare to IGBTs in terms of performance and efficiency?
SiC MOSFETs offer higher voltages and frequencies, improved heat dissipation, and reduced switching losses compared to IGBTs, making them well-suited for high power applications and driving efficiency and performance improvements.
How are SiC MOSFETs impacting renewable energy systems?
SiC MOSFETs are impacting renewable energy systems by optimizing the performance of solar inverters and wind converters, leading to efficiency improvements and potential cost reductions, ultimately driving significant performance enhancements.