Are you curious about the fundamentals of through hole technology and its role in electronics manufacturing? Through hole technology involves inserting electronic component leads into pre-drilled holes on a printed circuit board and then soldering them in place to create strong mechanical connections. This guide will walk you through the what, how, and why of through hole technology, distinguishing it from surface mount technology and exploring its enduring relevance in various industries.
Key Takeaways
- Through hole technology remains a fundamental approach in electronics manufacturing due to its ability to create strong mechanical bonds, which is particularly important for applications exposed to environmental stresses and requiring high reliability.
- The precision and stability afforded by through hole components such as axial and radial lead components enable versatility in design and mounting, catering to various roles within electronic circuits and accommodating demands for high thermal and mechanical stress.
- While through hole technology offers the advantages of robustness and ease of repair, it is often more costly and less efficient in terms of space compared to surface mount technology, making it less suitable for applications where compact size and cost reduction are primary objectives.
Understanding Through Hole Technology
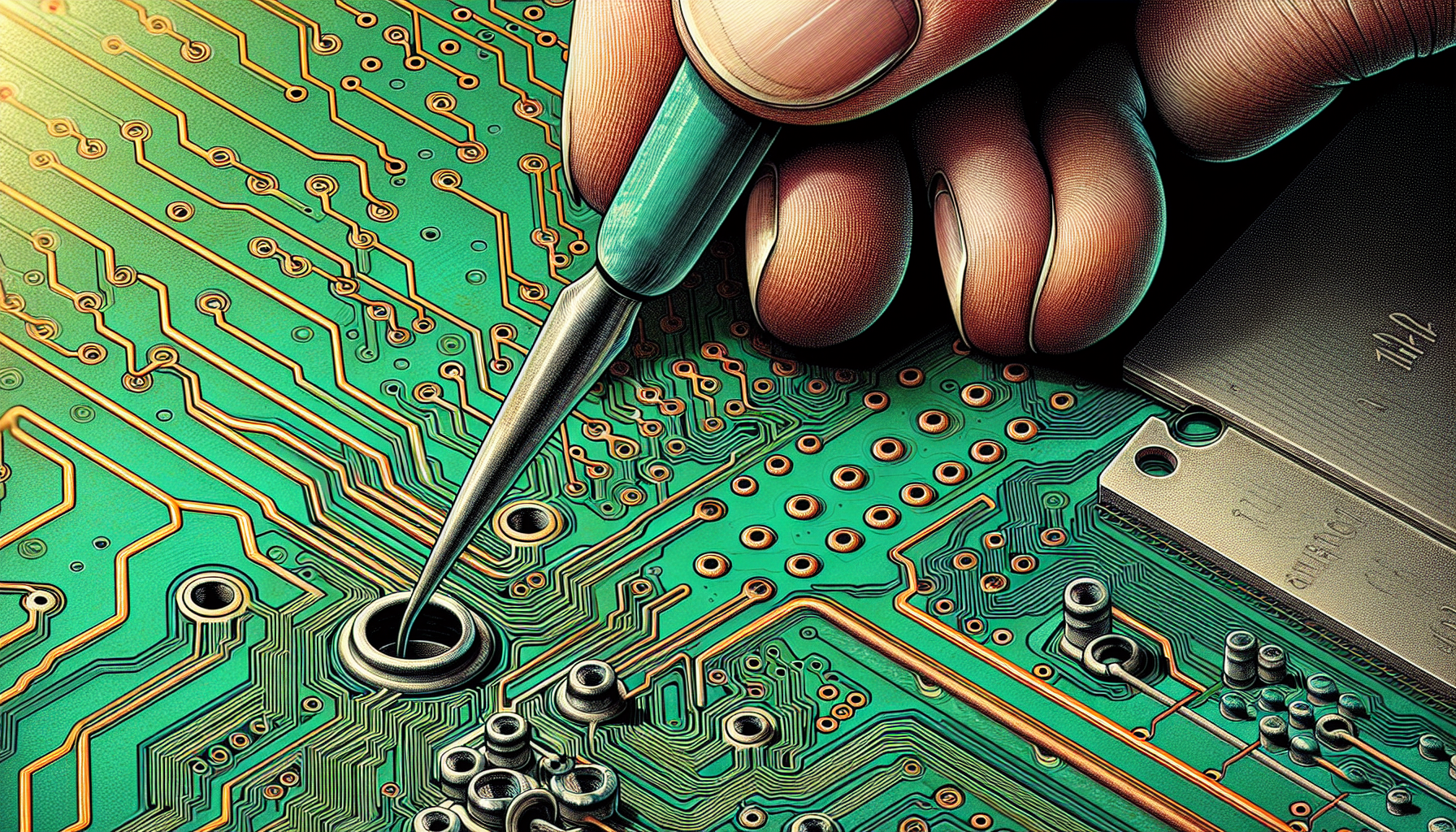
Through hole technology requires a hands-on approach. Electronic components are inserted into pre-drilled holes on a printed circuit board (PCB) and then soldered from the opposite side. This assembly method forms the backbone of electronics manufacturing, a standard that has been relied upon for decades before the emergence of surface mount technology. The enduring nature of through hole components stems from their ability to form strong mechanical bonds, making them ideal for devices subject to various environmental stresses.
Through hole technology is not just about strength; it’s also about versatility and repairability. Through hole mounting allows components to be manually adjusted or replaced, simplifying prototyping and allowing for easy modifications. Such flexibility is indispensable in industries that demand robust and long-lasting electronic assemblies.
In contrast to surface mount technology, which places surface mount components on the PCB’s surface, through hole technology secures components by inserting their leads through the board itself, providing an unmatched level of durability.
The Role of Through Hole Components
Through hole components are the stalwarts of PCB assembly, offering invaluable benefits in situations that can put electronics through their paces—think connectors or transformers that must endure significant mechanical stress. During the prototyping phase, these components are particularly prized by design engineers for their ease of use with breadboard sockets, making them a go-to for testing and adjustments.
Devices requiring reliable operation under challenging conditions like high voltage, power, and heat often incorporate through-hole technology. This makes through hole components a common sight in applications where performance and durability are critical, such as in the medical or aerospace sectors. Furthermore, their larger size relative to surface-mounted components also means they can handle more thermal stress, which is crucial in demanding applications. However, surface mount devices have gained popularity in recent years due to their compact size and ease of assembly.
Drilling Holes for Through Hole Assembly
When preparing a PCB for through hole assembly, precision is key in the pcb assembly process. The process starts with drilling holes in specified areas to fit the component leads. This initial step is critical as the drilled holes must be precise not only to ensure the pins fit securely but also to align perfectly with the board’s design and functionality. The hole size, in particular, is a crucial consideration, as it must be just right to allow for a snug fit of the component pins.
Careful planning and execution of the hole drilling process are essential for a successful assembly. The exact placement of each hole affects the overall performance of the electronic assembly, as any misalignment can lead to functionality issues or even short-circuits. It’s a meticulous task that sets the stage for the strong and resilient connections that through hole technology is known for.
Types of Through Hole Components
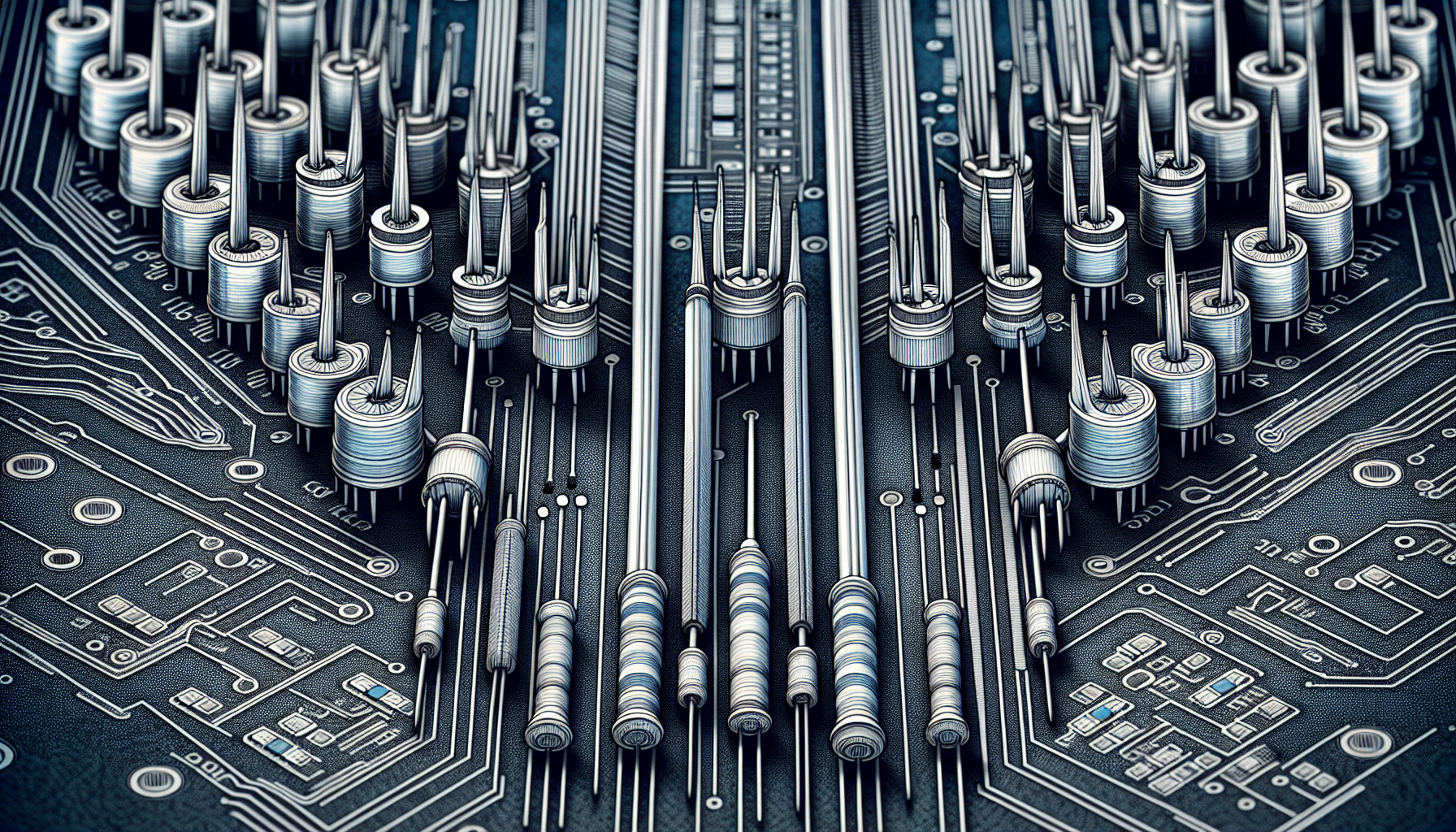
In the world of through hole technology, components of various shapes and sizes suit specific roles within electronic circuits. The most common types of through hole components are distinguished by their lead configurations: axial and radial. These designations not only affect how the components are inserted into the PCB but also their overall footprint, which is a key consideration in electronic circuit design.
Axial lead components have leads that exit from both ends, enabling them to span short distances on a PCB and providing a low-profile configuration when necessary. Radial lead components, on the other hand, feature leads emerging from one side, simulating a ‘plugin’ nature suitable for vertical mounting. Both types are integral to the vast array of through hole components found in electronic devices.
Passive Through Hole Components
Components like resistors and ceramic disk capacitors, known as passive through hole components, play a vital yet understated role in electronic circuits. Axial lead components like resistors frequently come in this form, with leads extending from both ends along the component’s longitudinal axis. They are a common sight on PCBs, serving essential functions without the need for an external power source.
Radial lead components differ in that their leads emerge from one side of the component body, often seen in ceramic disk capacitors and other passive elements. These components are favored for their compact nature and ability to fit into various electronic circuits, making them an indispensable part of the electronic component ecosystem.
Active Through Hole Components
Many electronic functions are driven by active through hole components, which act as the processors and controllers within a circuit. Integrated circuits (ICs), transistors, and high-power LEDs are prime examples of active components that are easy to integrate into PCBs, thanks to their through hole design. Such components are pivotal in managing data, amplifying signals, and providing illumination—roles that demand reliable and consistent performance.
Their ease of integration is a testament to the versatility of through hole technology, which facilitates the incorporation of a wide range of active components into electronic systems. As a result, through hole technology remains a vital aspect of electronics manufacturing, enabling the creation of devices that are both sophisticated and robust.
Mounting Techniques for Through Hole Components
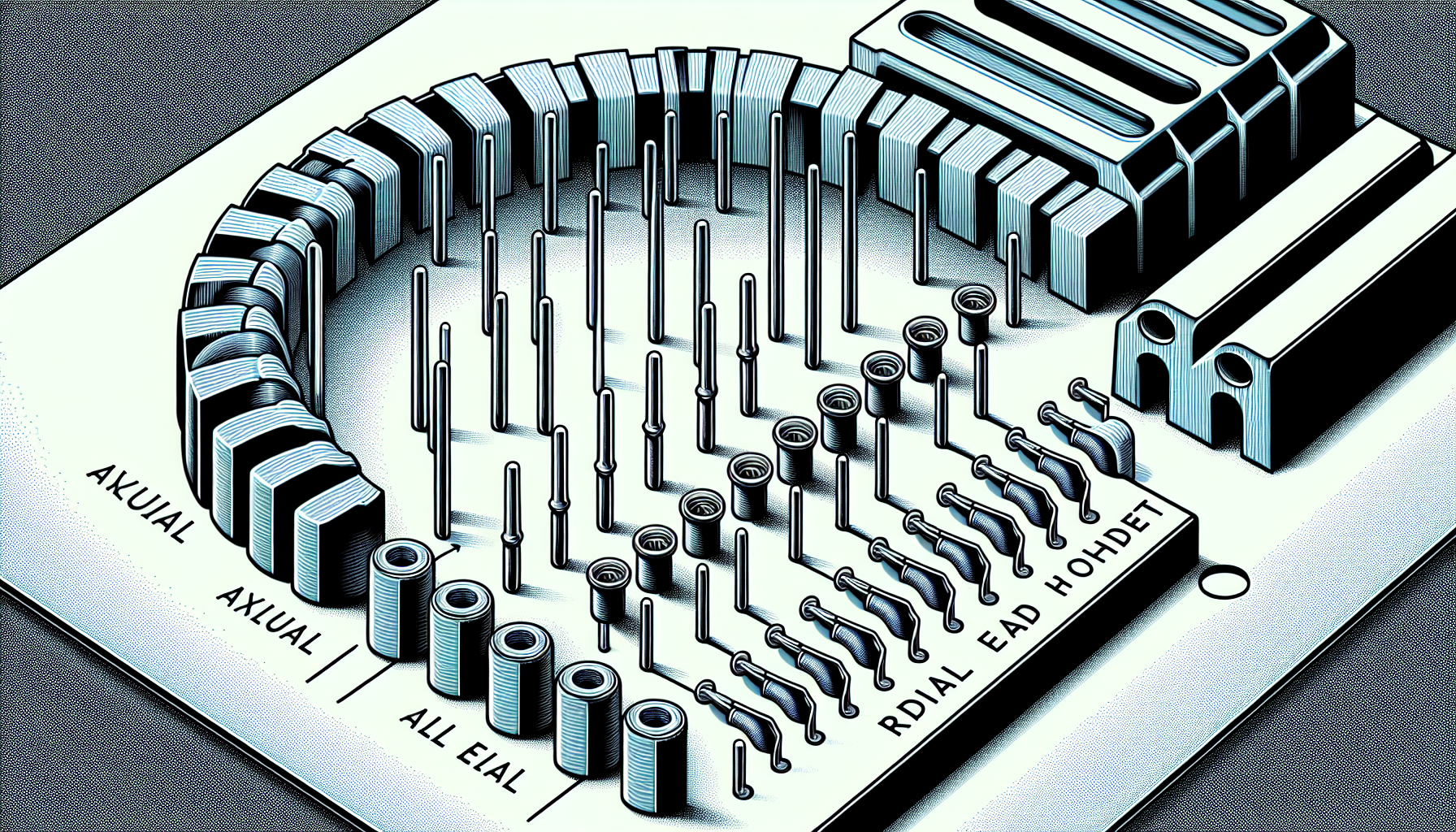
Precision and stability are the key factors in mounting techniques for through hole components. Axial and radial leads provide two distinct methods of securing components to a PCB, and each has implications for the overall design and layout of the board. Axial lead components, for example, have leads that run in a straight line through the component, exiting from either end, which can be advantageous for certain circuit configurations.
Radial lead components, with leads that come out from one side, are designed for quick insertion into PCBs by automated machines. They occupy less space on the board and have a fixed lead spacing, making them particularly suitable for high-density applications where space is at a premium. Both types of mounting techniques contribute to the diversity and flexibility of through hole technology in accommodating a wide range of electronic components.
Axial Lead Components
Axial lead components are versatile in their mounting options, making them ideal for various mounting components scenarios. They can be mounted horizontally for a low-profile fit, or vertically to save space on the PCB—a technique that is especially useful when addressing spacing constraints. Before mounting, the component leads are bent at a right angle using precision tools, ensuring a snug fit into the drilled holes on the board.
Once soldered into place, the leads of axial components are trimmed to remove excess length, but with careful consideration to leave enough material to maintain a robust connection. This meticulous approach to mounting axial lead components ensures uniformity and reliability in the final electronic assembly, reflecting the enduring quality of through hole technology.
Radial Lead Components
Radial lead components are characterized by their:
- Compact design
- Ease of assembly
- Leads that emerge from one side of the component body, allowing for vertical mounting
- Ideal for conserving space on the PCB
- Popular choice in electronics manufacturing, particularly in applications where high component density is essential.
Their design allows for quick and efficient insertion into PCBs, often facilitated by automated assembly machines. This not only speeds up the manufacturing process but also ensures greater accuracy and consistency in component placement. Thus, radial lead components represent a crucial facet of through hole technology, one that combines practicality with performance.
Soldering Through Hole Components
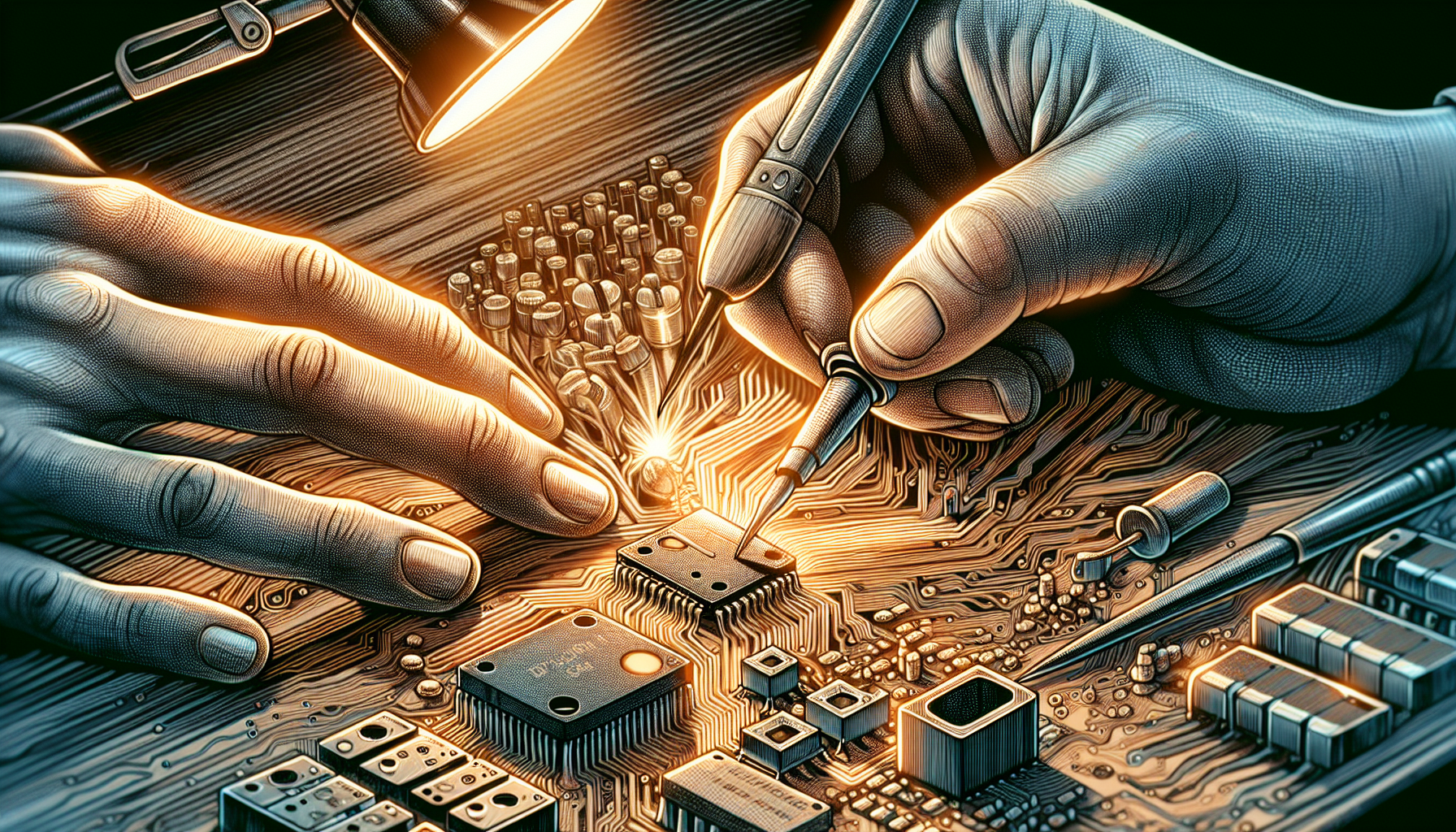
The soldering process, which creates strong and durable electrical connections, is crucial for securing through hole components to a PCB. The process involves inserting component leads through pre-drilled holes and soldering them to pads on the opposite side of the PCB — a technique that calls for precision and care. The leads are first cleaned with flux, which not only cleans them but also enhances thermal conductivity, ensuring that the solder flows smoothly and creates a secure bond.
Once the components are secured in place, each lead is soldered to its corresponding pad using a soldering iron and solder. The result is a solder joint that, if done correctly, has a bright appearance and a properly formed fillet, indicative of a high-quality connection. These joints are the lifeline of the electronic assembly, ensuring that each component functions as intended and contributes to the overall performance of the device.
Preparing the PCB for Soldering
Successful soldering requires a clean PCB. The board is thoroughly wiped with isopropyl alcohol to remove any contaminants that could impede the soldering process. This step ensures that the PCB surface is pristine and ready for the components to be mounted. The leads of the components are also cleaned to ensure that they are free from any residues that could affect the quality of the solder joints.
Tinning, a process where a small amount of solder is applied to the iron tip and PCB pads, prepares both surfaces for the upcoming soldering. Flux is applied to both sides of the PCB to clean and improve thermal conductivity, but solder is only added to the underside where the actual soldering will take place.
After soldering, a final cleaning with isopropyl alcohol and an inspection ensure that each joint is smooth and shiny, confirming a proper and quality connection.
Solder Joint Inspection
Once the soldering is complete, every joint must be examined to confirm it meets the standards for reliability and functionality. Inspecting the quality of solder joints is essential, as it can reveal any potential issues that might compromise the integrity of the electronic assembly. For Class 2 and Class 3 PCBs, a solder fill rate of 75% is the benchmark for a sound mechanical and electrical connection, providing a good balance between strength and conductivity.
The annular ring, which is the area around the drilled hole on the PCB, also plays a crucial role in the durability of the joint. It must be sufficiently large to allow for a strong solder connection, ensuring that the component will remain securely in place even under stress. These inspections are non-negotiable, as they guarantee the longevity and reliability that through hole technology is revered for.
Comparing Through Hole and Surface Mount Technologies
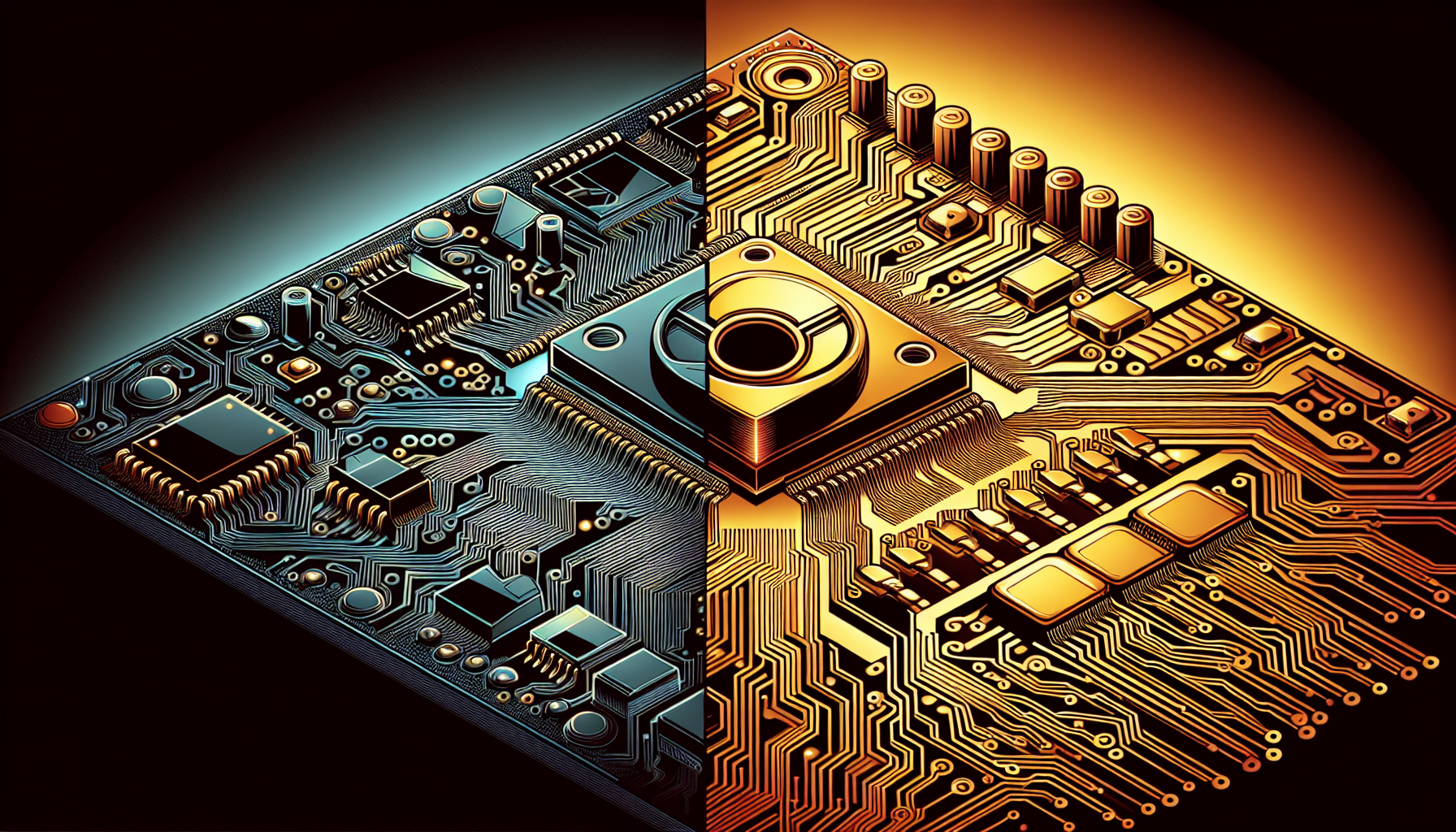
The decision between through hole and surface mount technologies typically depends on the specific needs of the electronic device. Through-hole components are inserted into plated through holes on the PCB, whereas surface mount technology (SMT) components are attached directly to the surface without the need for mating holes. This fundamental difference has significant implications for PCB design, with through-hole providing strong connections and SMT offering higher component density and cost efficiency.
While SMT caters to the trend towards miniaturization and allows for more compact device designs, it does present some challenges in terms of quality control and repairability. Components must be precisely identified and placed, and cleanliness during the assembly process is critical to prevent defects.
Through hole technology, despite leading to larger PCB sizes and cost, maintains its relevance due to its superior performance under mechanical or thermal stress, making it indispensable for certain applications.
Advantages of Through Hole Technology
One of the greatest strengths of through hole technology is its strong mechanical bonds. These bonds provide greater reliability and mechanical strength, essential for components on a PCB that must endure rigorous use or harsh environments. The ability to manage higher levels of current and voltage also makes through hole components suitable for high-power applications, where they can reliably handle the demands placed upon them.
Another significant advantage of through hole technology is the ease of repair and component replacement it offers. Faulty parts can be identified and substituted without much difficulty, which is especially beneficial during the prototyping phase and for maintenance purposes. This accessibility makes through hole technology a practical choice in many scenarios, despite the advancements in SMT.
Disadvantages of Through Hole Technology
Through hole technology, despite its advantages, does present certain drawbacks. The most significant is the higher production costs associated with the additional labor and machinery required for drilling holes and inserting components. This labor-intensive process can make through hole technology less cost-effective, especially for mass production where efficiency and speed are crucial.
Furthermore, through hole technology limits component density on a PCB. The need for space to accommodate the leads means that through hole assemblies are inherently larger than their SMT counterparts, which can place components closer together. This limitation is a significant disadvantage in an industry where the trend is towards miniaturization and making devices as compact as possible.
Applications of Through Hole Technology
Applications prioritizing strength and reliability over miniaturization often utilize through hole technology. It’s suited for bulky or heavy components such as electrolytic capacitors and semiconductors, which require strong mechanical support. This makes it the preferred choice in sectors where durability and longevity are non-negotiable, such as aerospace, defense, and medical equipment.
The robust nature of through hole assemblies ensures their presence in high-reliability industries and in scenarios where electronic devices are exposed to high stress or environmental challenges. Though surface mount technology has become prevalent, there remains a clear and defined role for through hole technology in the world of electronics manufacturing, especially in applications where component size and cost reduction are not the primary concerns.
High-Reliability Industries
Industries that require high reliability and can’t afford failures often depend on through hole technology due to its robust connections that can withstand extreme conditions. Aerospace and defense sectors, for instance, depend on through hole components to ensure performance and reliability in demanding environments. In the realm of medicine, through hole technology plays a crucial role in life-saving devices such as patient monitors and life-support systems, where precision and adherence to stringent regulatory standards are imperative.
Similarly, in the automotive industry, the reliability of vehicle electronics, including engine controls and safety mechanisms, often hinges on the robust construction of through hole technology. Industrial applications, too, benefit from this technology in high-power electronics like robotics and motor drives, which must handle high currents and voltages without faltering. In these sectors, the durability offered by through hole technology is not just preferred but essential.
Large-Scale Electronics
The advantages of through hole technology are evident in the field of large-scale electronics. In the automotive industry, for example, systems that must perform reliably under harsh conditions—like engine controls and safety features—often utilize through hole components for their superior durability. Industrial electronics also capitalize on the robustness of through hole technology, particularly in situations where handling high power and voltage is a requirement.
The preference for through hole technology in these contexts highlights its continued relevance in the electronics industry. While it may not be the go-to solution for devices where size and cost are of utmost concern, for applications that demand high reliability and the ability to endure mechanical and environmental stress, through hole technology remains the pillar of electronic hardware design.
Summary
Through hole technology has stood the test of time, proving that its value in creating durable and reliable electronic assemblies cannot be understated. From its role in high-reliability industries to its application in large-scale electronics, through hole technology remains an integral part of the electronics manufacturing landscape. Its ability to provide strong mechanical bonds, high power handling capabilities, and ease of repair makes it indispensable in many contexts.
As technology continues to evolve, the balance between the traditional through hole approach and modern surface mount technology will undoubtedly shift. However, the choice between them will remain dependent on the specific needs of each application. Through hole technology, with its unique advantages, will continue to play a crucial role in the electronics industry for applications where robustness and reliability are paramount.
Frequently Asked Questions
What is the through-hole soldering process?
Through-hole soldering is the process of mounting components to a PCB using physical leads that are inserted through holes in the circuit board and soldered to the opposite side to secure the component in place.
What is the difference between SMT and through-hole?
In conclusion, through-hole components provide stronger connections between layers for high-reliability products, while SMT components are secured only by surface solder, making them more suitable for less stressful environments.
What is a through-hole in drilling?
A through hole is a hole that goes through the entire workpiece, as opposed to a blind hole, which does not pass through the entire workpiece and has only a certain depth.
How do axial and radial lead components differ in through hole technology?
In through hole technology, axial lead components have leads extending from both ends, allowing for horizontal or vertical mounting, while radial lead components have leads emerging from one side, enabling vertical mounting and saving space on the PCB.
Why is through hole technology still used in high-reliability industries?
Through hole technology is favored in high-reliability industries like aerospace, defense, and medical due to its durable connections that can withstand extreme conditions, ensuring dependable performance in critical applications.